Simplificar las piezas para moldeo o cómo podemos ayudarte a reducir la inversión necesaria
El éxito comercial de un producto de moldeo por inyección depende de la combinación de varios factores clave:
- Un diseño optimizado
- Una producción eficiente
- La elección del material adecuado
- Una marca bien posicionada
- Un servicio posventa de calidad.
Cada uno de estos elementos contribuye al desarrollo de un producto competitivo y confiable, capaz de responder a las demandas y expectativas del mercado.
Para lograr un diseño optimizado, es fundamental cumplir con las especificaciones funcionales y estéticas de la pieza, asegurando al mismo tiempo su viabilidad y eficiencia en el proceso de fabricación. Esto facilitará la industrialización, optimizará la producción y permitirá reducir tanto la inversión inicial como los defectos, el rechazo de piezas y, en consecuencia, los costes finales del producto.
Un ejemplo de esto podría ser el proyecto de industrialización de una rótula que hicimos hace un tiempo para un cliente y que describiremos a continuación.
En el caso que se va a comentar, dicho cliente nos envió una consulta para la fabricación de una rótula/ articulación compuesta por 2 piezas, fabricadas por HPDC (inyección/moldeo a alta presión) de zamak. Este proyecto, además, tenía como prioridad la completa funcionalidad de la rótula, junto a su acabado estético (por tratarse de una pieza vista).
En los primeros análisis realizados a las piezas, ya en la fase oferta del proyecto, se detectó lo siguiente:
Problemas en los diseños iniciales de cara al proceso de fabricación:
- Piezas muy másicas (el interior era completamente macizo). En fundición inyectada se debe optar por piezas tipo “pared”, para unificar los espesores y por ende la solidificación de la pieza, ya que una solidificación no uniforme genera deformaciones. Además, una pieza maciza posee un mayor volumen, que significa un mayor consumo de materia prima, lo que implica un mayor coste/ pieza.
- Zonas imposibles de moldear, por quedar “en sombra” respecto de la dirección primaria de moldeo y sin opción de moldeo lateral mediante correderas por interferencia con otras partes de la pieza.
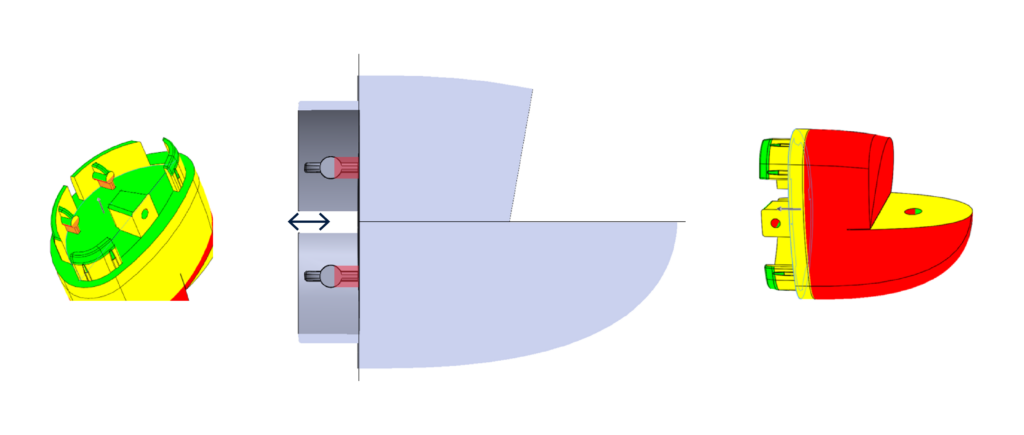
- Zonas, aunque posibles de moldear, que presentan un riesgo muy elevado para la vida del molde. Esto sucede cuando se generan zonas con geometrías en el acero débiles; en este caso, las correderas generarían un espesor muy bajo de acero respecto a la pieza. También existían otras zonas críticas, pero debidas a imperfecciones en el diseño de las superficies.
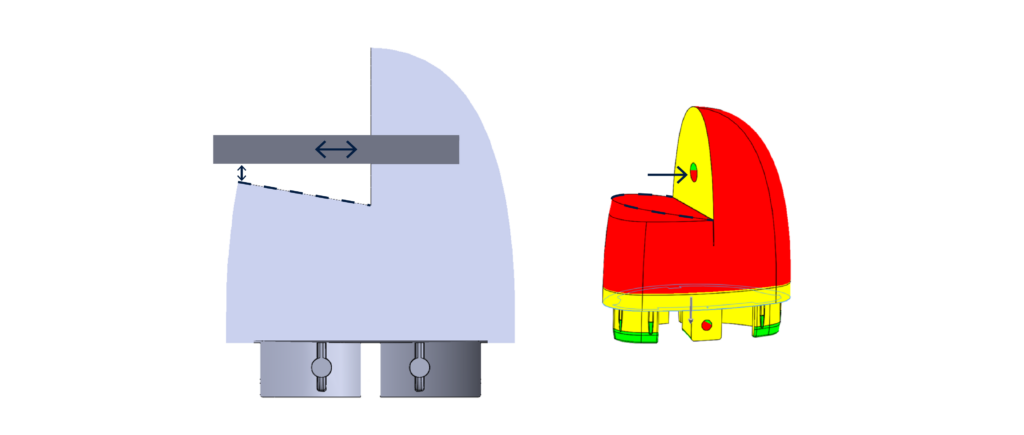
- Molde complejo por la necesidad de colocación de múltiples correderas. Las piezas presentaban múltiples zonas y taladros que no podrían ser moldeados en la dirección primaria de moldeo. Estas correderas generan a su vez marcas en la pieza en las zonas de “cierre”, y muchas de estas quedarían en zonas vistas/ estéticas.

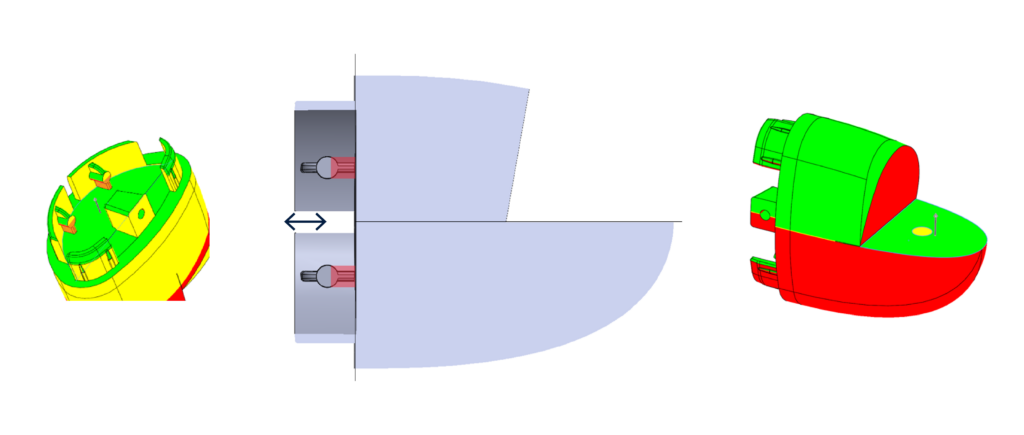
- Dificultad para expulsar la pieza del molde sin afectar a sus caras exteriores (piezas estéticas), así como para evitar líneas de cierre en ellas en cualquiera de las diferentes opciones de moldeo.
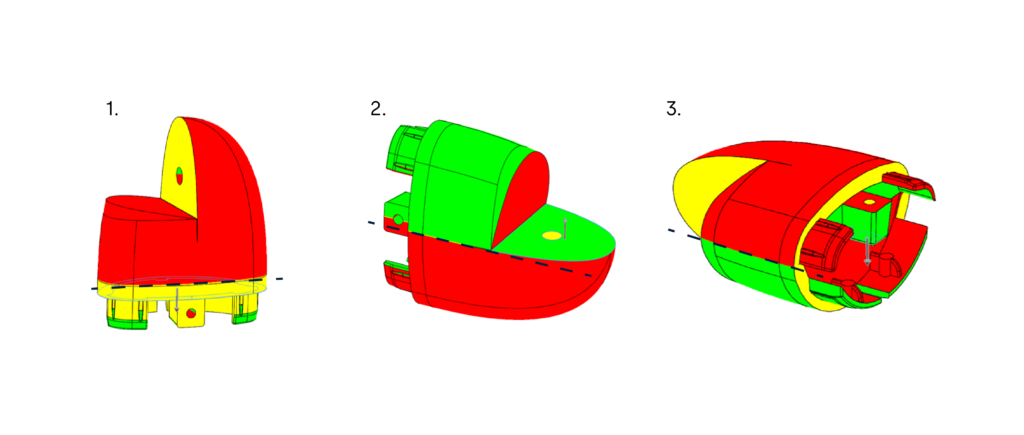
- Defectos en los diseños por falta de refinamiento. Este punto no suele tener importancia, pero siempre es necesario sacarlo a la luz cuanto antes para evitar problemas en fases posteriores.
En este caso, existían superficies que se unían generando “ranuras” no moldeables.
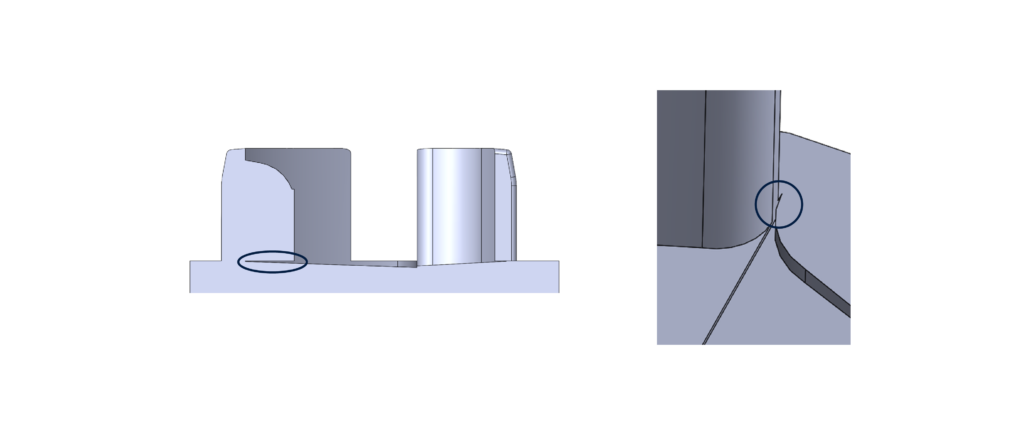
Ante estos problemas principales, se inició un diálogo cercano con el cliente para explorar diferentes opciones y propuestas. Este intercambio permitió comprender en mayor detalle el funcionamiento y el entorno de los diseños.
Este diálogo es clave para poder proponer soluciones que mantengan las características del producto final y logren mejorar su rendimiento y su optimización.
Si deseas conocer cómo avanzó este proceso y cómo abordamos cada desafío para llegar a una solución perfecta, te invitamos a registrarte en nuestro blog. Obtén acceso a contenido exclusivo, entrevistas y casos prácticos que detallan cómo transformamos cada reto en una oportunidad.
Contacta con nosotros
Te daremos asistencia para tus proyectos y resolveremos tus dudas lo antes posible