Versiones intermedias: Evolución del diseño para reducir la inversión
En este artículo exploraremos cómo, tras el análisis profundo de los desafíos planteados por nuestro cliente, implementamos soluciones específicas para optimizar el diseño e industrialización de la rótula de Zamak.
A través de un proceso de colaboración estrecha, fuimos capaces de realizar ajustes que no solo mejoraron la funcionalidad y el acabado estético, sino que también permitieron una mayor eficiencia en la producción y redujeron los costes asociados.
Una vez se avanzó el intercambio de información con el cliente, transmitiendo los puntos comentados en el anterior artículo (Simplificar las piezas para moldeo o cómo podemos ayudarte a facilitar y reducir la inversión necesaria), los diseños fueron evolucionando tanto para la mejora del proceso como para la mejora de la funcionalidad del conjunto final.
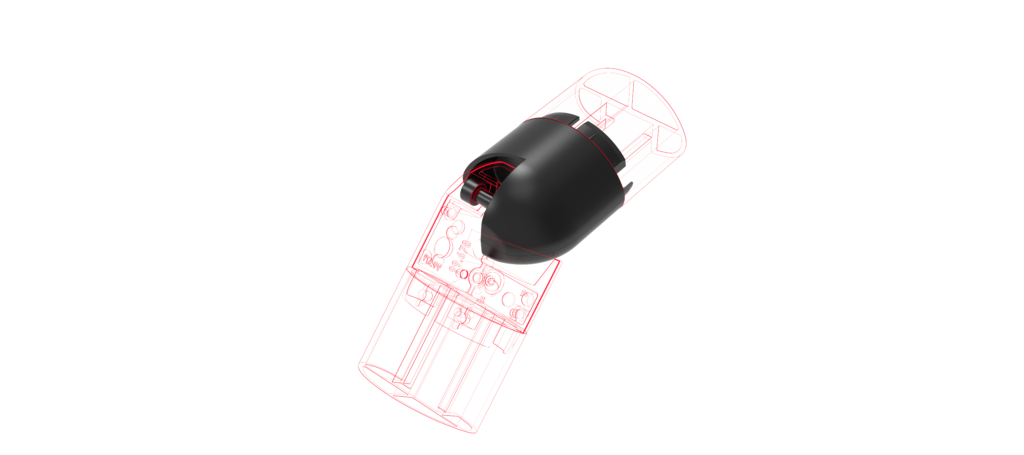
Evolución del diseño en esta fase intermedia:
- Vaciado de la pieza (tanto desde la parte inferior como desde la superior), para evitar los problemas de acumulación de masa (antes eran totalmente macizas).
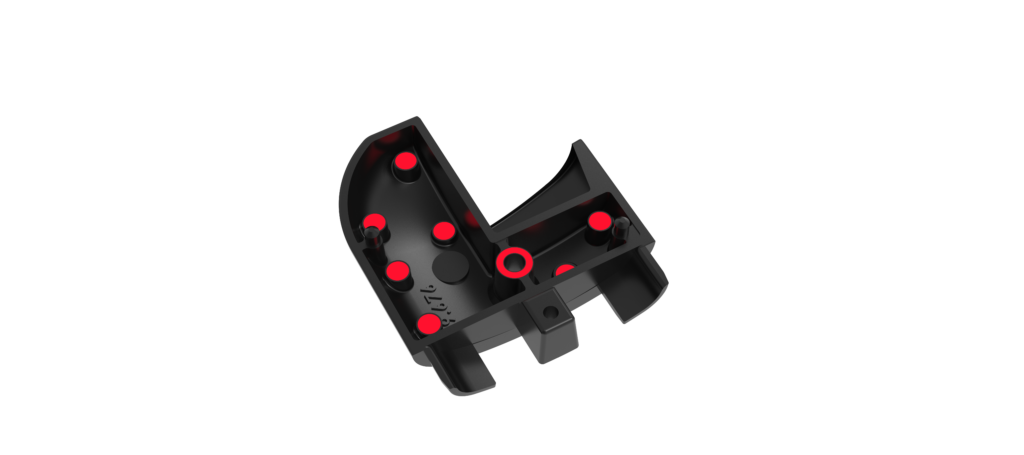
- Supresión de las geometrías imposibles de moldear: se corrigieron aquellas zonas de las piezas que quedaban “en sombra” para la dirección de moldeo y que no eran moldeables tampoco mediante correderas.
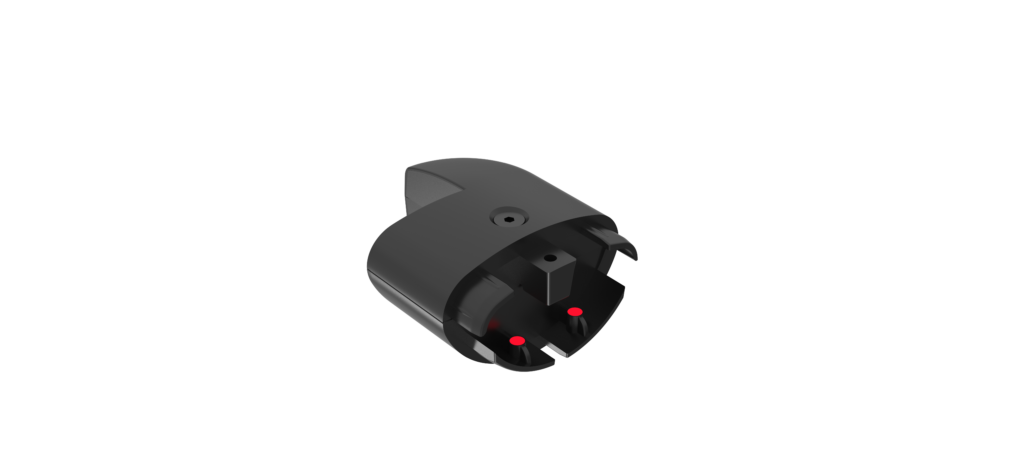
- Recorte de la punta (oculta en el montaje) para mejorar el moldeo y evitar interferencias en el movimiento de la articulación.
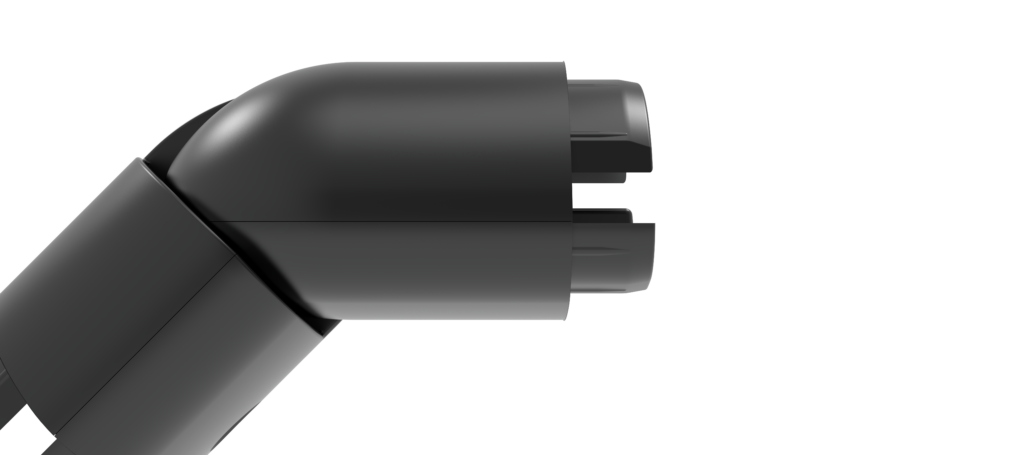
- Corrección de las imprecisiones en el diseño. En este estado intermedio ya no existen superficies mal unidas entre ellas, ni zonas de espesores imposibles.
Con todos estos cambios, las piezas ya eran moldeables, pero todavía quedaban puntos por corregir:
Por un lado, las piezas seguían teniendo la necesidad de contar con múltiples correderas (que dificultan y encarecen el molde, además de generar marcas en las piezas).
Por otro lado, seguía estando el problema de la presencia de líneas de unión/cierre del molde, alimentaciones, etc. en caras vistas (las piezas son estéticas en sus 360º) y, a todo esto, se debía sumar la generación de zonas débiles en el acero del molde especialmente en la zona de las correderas.
Además, debido a la necesidad de dar ángulos de salida a la pieza siguiendo este concepto de moldeo, la unión de esta con los perfiles sobre los que montaba no resultaba totalmente satisfactoria ya que se producía un cambio de dirección en el perfil de la unión, así como un “escalón”.
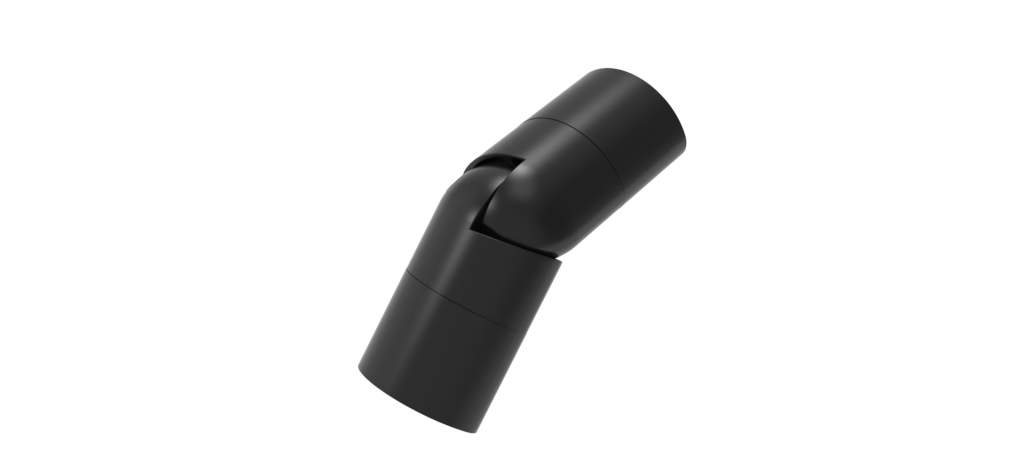
Si quieres ver cómo quedó la pieza final después de resolver todos estos desafíos, no te pierdas la última entrega de esta serie, donde te mostraremos en resultado final y cómo cada ajuste contribuyó a mejorar la calidad y funcionalidad del producto.
Contacta con nosotros
Te daremos asistencia para tus proyectos y resolveremos tus dudas lo antes posible