Simplifier les pièces à mouler ou comment nous pouvons vous aider à réduire l’investissement nécessaire
Le succès commercial d’un produit moulé par injection dépend de la combinaison de plusieurs facteurs clés:
- Une conception optimisée
- Une production efficace
- Le choix du matériau adéquat
- Une marque bien positionnée
- Un service après-vente de qualité.
Chacun de ces éléments contribue au développement d’un produit compétitif et fiable, capable de répondre aux exigences et aux attentes du marché.
Pour obtenir une conception optimisée, il est essentiel de respecter les spécifications fonctionnelles et esthétiques de la pièce, tout en garantissant sa viabilité et son efficacité dans le processus de fabrication. Cela facilitera l’industrialisation, optimisera la production et permettra de réduire à la fois l’investissement initial et les défauts, le rejet de pièces et, par conséquent, les coûts finaux du produit.
Un exemple de cela pourrait être le projet d’industrialisation d’une rotule que nous avons réalisé il y a quelque temps pour un client et que nous décrirons ci-dessous.
Dans le cas qui va être commenté, ce client nous a envoyé une demande pour la fabrication d’une rotule/articulation composée de 2 pièces, fabriquées par HPDC (injection/moulage à haute pression) en zamak. Ce projet avait également pour priorité la fonctionnalité complète de la rotule, ainsi que sa finition esthétique (car il s’agit d’une pièce visible).
Les premières analyses réalisées sur les pièces, dès la phase d’appel d’offres du projet, ont permis de détecter les éléments suivants:
Problèmes dans les conceptions initiales en vue du processus de fabrication:
- Pièces très massives (l’intérieur était complètement solide). En moulage par injection, il faut opter pour des pièces de type « paroi » afin d’uniformiser les épaisseurs et donc la solidification de la pièce, car une solidification non uniforme génère des déformations. De plus, une pièce massive a un volume plus important, ce qui signifie une plus grande consommation de matière première, et donc un coût plus élevé par pièce.
- Zones impossibles à mouler, car elles restent « dans l’ombre » par rapport à la direction principale du moulage et sans possibilité de moulage latéral à l’aide de coulissantes en raison d’interférences avec d’autres parties de la pièce.
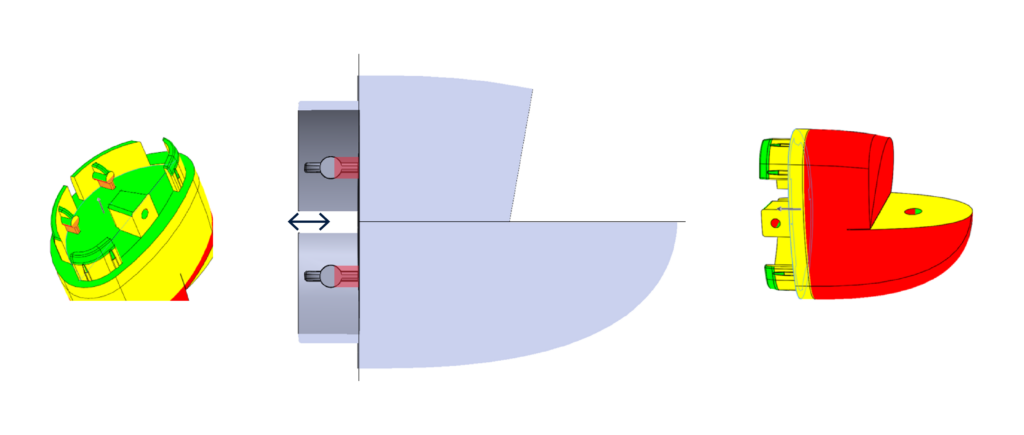
- Zones, bien que moulables, présentant un risque très élevé pour la durée de vie du moule. Cela se produit lorsque des zones présentant des géométries fragiles dans l’acier sont générées ; dans ce cas, les coulissantes généreraient une épaisseur d’acier très faible par rapport à la pièce. Il existait également d’autres zones critiques, mais celles-ci étaient dues à des imperfections dans la conception des surfaces.
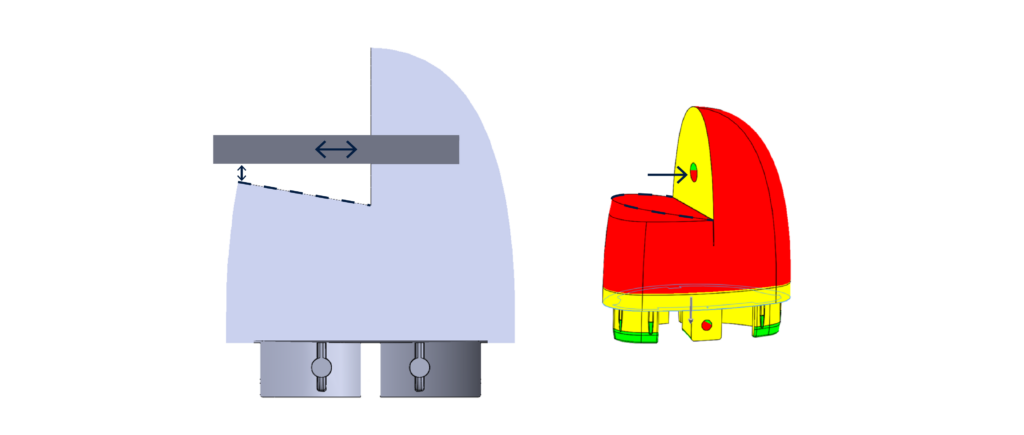
- Moule complexe en raison de la nécessité de placer plusieurs coulissantes. Les pièces présentaient plusieurs zones et alésages qui ne pouvaient pas être moulés dans le sens principal du moulage. Ces coulissantes génèrent à leur tour des marques sur la pièce dans les zones de « fermeture », dont beaucoup resteraient visibles/esthétiques.

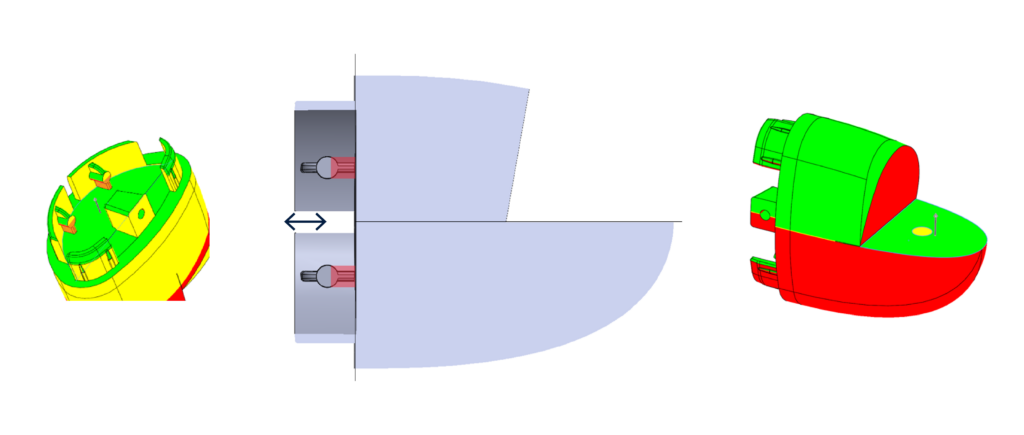
- Difficulté à extraire la pièce du moule sans endommager ses faces extérieures (pièces esthétiques) et à éviter les lignes de fermeture sur celles-ci, quelle que soit l’option de moulage choisie.
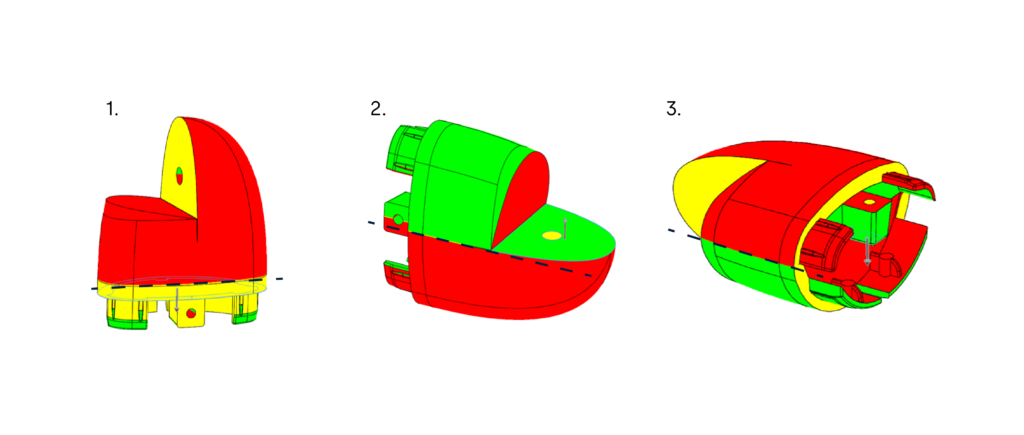
- Défauts de conception dus à un manque de raffinement. Ce point n’a généralement pas d’importance, mais il est toujours nécessaire de le mettre en évidence dès que possible afin d’éviter des problèmes ultérieurs.
Dans ce cas, certaines surfaces se rejoignaient, créant des « rainures » non moulables.
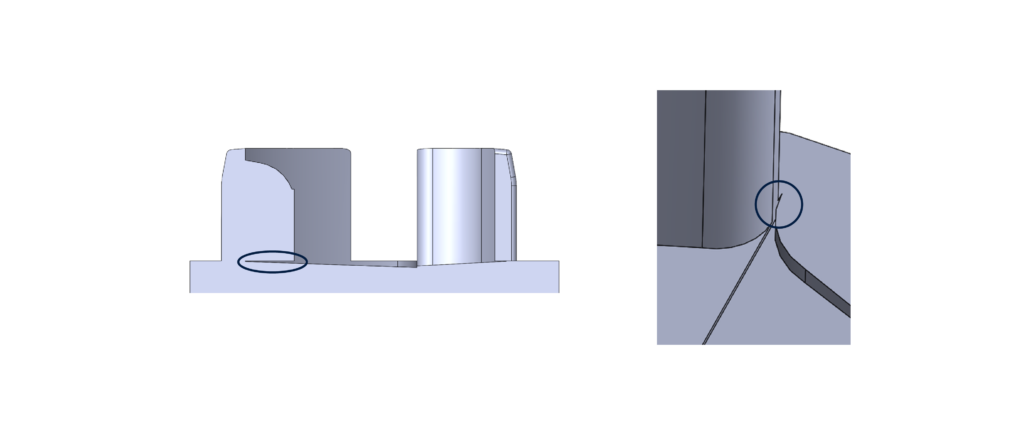
Face à ces problèmes majeurs, un dialogue étroit a été engagé avec le client afin d’étudier différentes options et propositions. Cet échange a permis de mieux comprendre le fonctionnement et l’environnement des conceptions.
Ce dialogue est essentiel pour pouvoir proposer des solutions qui préservent les caractéristiques du produit final tout en améliorant ses performances et son optimisation.
Si vous souhaitez savoir comment ce processus s’est déroulé et comment nous avons relevé chaque défi pour parvenir à une solution parfaite, nous vous invitons à vous inscrire à notre blog. Accédez à des contenus exclusifs, des interviews et des études de cas qui détaillent comment nous avons transformé chaque défi en opportunité.
Contactez-nous
Nous vous assisterons dans vos projets et répondrons à vos questions dans les meilleurs délais