Versions intermédiaires : évolution de la conception pour réduire l’investissement
Dans cet article, nous explorerons comment, après une analyse approfondie des défis posés par notre client, nous avons mis en œuvre des solutions spécifiques pour optimiser la conception et l’industrialisation de la rotule en zamak.
Grâce à un processus de collaboration étroite, nous avons pu apporter des ajustements qui ont non seulement amélioré la fonctionnalité et la finition esthétique, mais ont également permis une plus grande efficacité de production et une réduction des coûts associés.
Une fois que l’échange d’informations avec le client a avancé, en transmettant les points évoqués dans l’article précédent (Simplifier les pièces à mouler ou comment nous pouvons vous aider à réduire l’investissement nécessaire), les conceptions ont évolué tant pour améliorer le processus que pour améliorer la fonctionnalité de l’ensemble final.
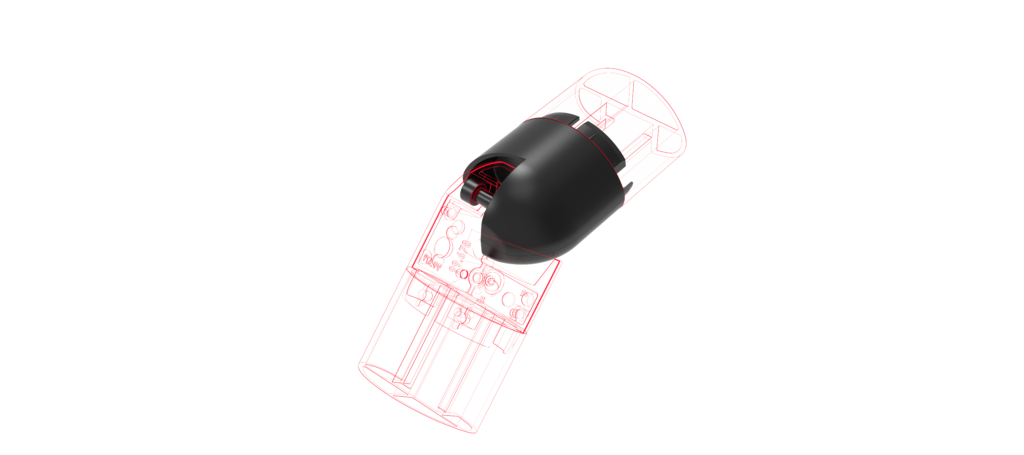
Évolution du design dans cette phase intermédiaire :
- Vidage de la pièce (aussi bien par le bas que par le haut) afin d’éviter les problèmes d’accumulation de masse (auparavant, elles étaient totalement massives).
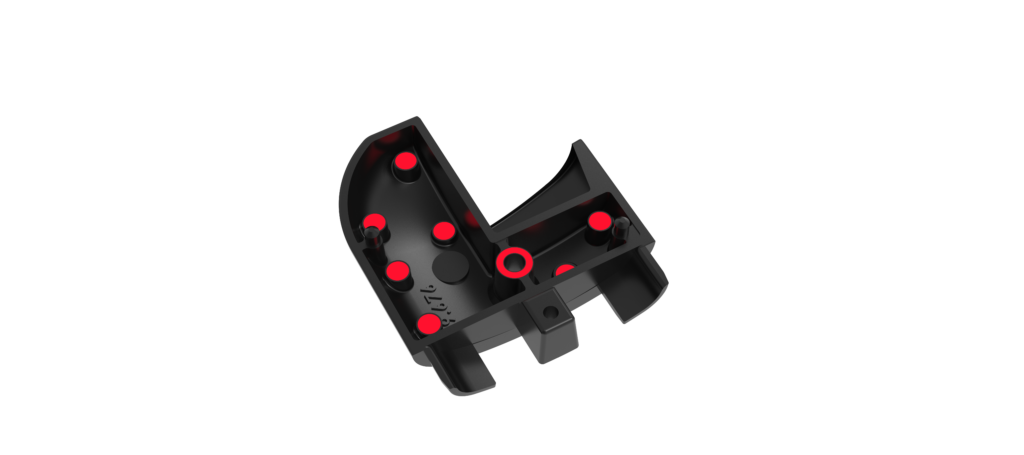
Suppression des géométries impossibles à mouler : les zones des pièces qui restaient « dans l’ombre » pour la direction du moulage et qui n’étaient pas moulables, même à l’aide de coulissantes, ont été corrigées.
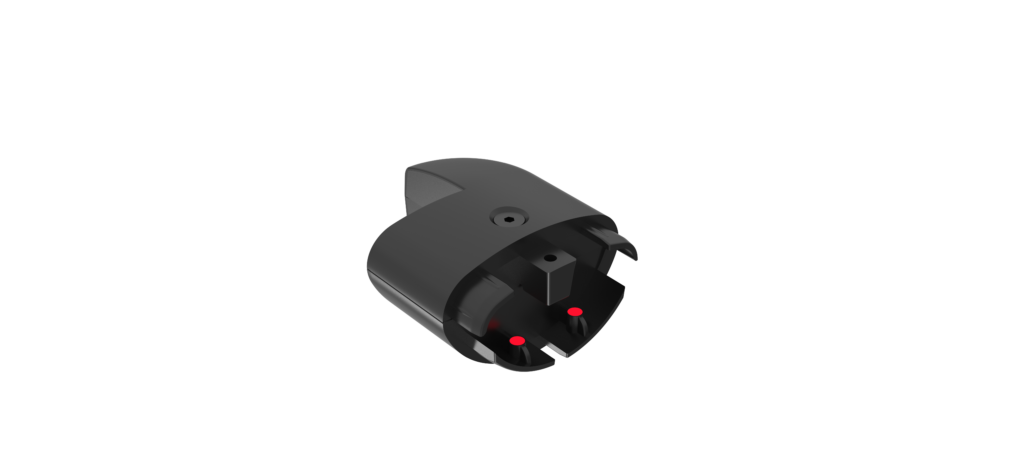
Découpe de la pointe (cachée lors du montage) pour améliorer le moulage et éviter toute interférence dans le mouvement de l’articulation.
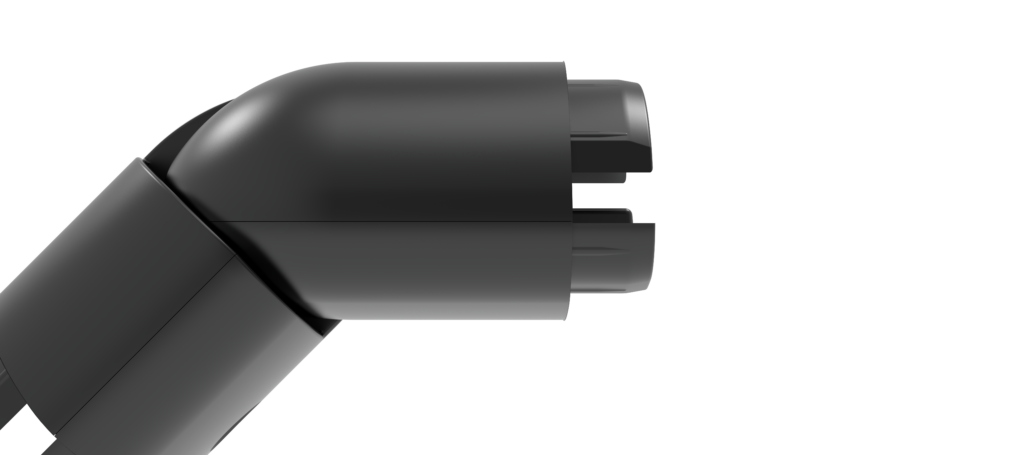
- Correction des imprécisions dans la conception. À ce stade intermédiaire, il n’y a plus de surfaces mal assemblées entre elles, ni de zones d’épaisseurs impossibles.
Avec tous ces changements, les pièces étaient désormais moulables, mais il restait encore quelques points à corriger :
D’une part, les pièces devaient toujours être équipées de multiples coulissantes (qui compliquent et renchérissent le moule, tout en générant des marques sur les pièces).
D’autre part, il restait le problème de la présence de lignes de jonction/fermeture du moule, d’alimentations, etc. sur les faces visibles (les pièces sont esthétiques à 360º) et, à tout cela, il fallait ajouter la génération de zones faibles dans l’acier du moule, en particulier dans la zone des coulissantes.
De plus, en raison de la nécessité de donner des angles de sortie à la pièce selon ce concept de moulage, l’assemblage de celle-ci avec les profilés sur lesquels elle était montée n’était pas entièrement satisfaisant, car il se produisait un changement de direction au niveau du profilé d’assemblage, ainsi qu’un « décalage ».
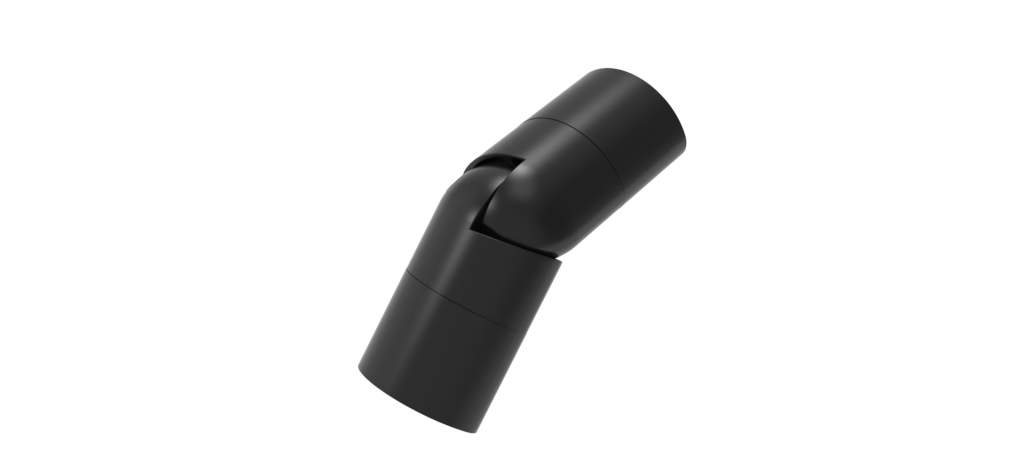
Si vous souhaitez voir le résultat final après avoir relevé tous ces défis, ne manquez pas le dernier volet de cette série, où nous vous montrerons le résultat final et comment chaque ajustement a contribué à améliorer la qualité et la fonctionnalité du produit.
Contactez-nous
Nous vous assisterons dans vos projets et répondrons à vos questions dans les meilleurs délais