
Otros procesos de fabricación
En STAC tenemos la capacidad de ofrecer otros procesos de fabricación esenciales para que una pieza cumpla sus requisitos técnicos con el acabado y la calidad necesaria. Nuestro equipo de expertos podrá ofrecerte soluciones adaptadas a los requerimientos de tu proyecto.
Fabricación aditiva
Al contrario que la fabricación tradicional (sustractiva) que parte de un tocho de material y elimina parte para obtener la forma final, la fabricación aditiva debe su reciente popularidad a su capacidad de obtener una forma final añadiendo material por capas, en la cantidad justa y necesaria, y de forma totalmente automática desde un diseño digital. Este proceso no necesita utillajes, herramientas ni máquinas auxiliares, lo que lo hace muy sencillo y accesible, tanto para cliente como para fabricante.
La forma de fabricación aditiva más popular y extendida es la también llamada impresión 3D de plásticos, dónde se puede partir de formatos en bobina de hilo, granulado, resinas líquidas, etc. También se aplica la fabricación aditiva a metales, pero esta resulta menos conocida ya que en la actualidad se reserva a entornos industriales. Existen muchas tecnologías para cada material, cada una con sus puntos a favor y en contra; y, en la experiencia, diseño y funcionalidad de la pieza residen las claves para escoger correctamente. Se pueden fabricar desde series pequeñas hasta medianas o grandes por este método, todo dependiendo de la capacidad de la máquina y de la automatización de esta y del proceso productivo.
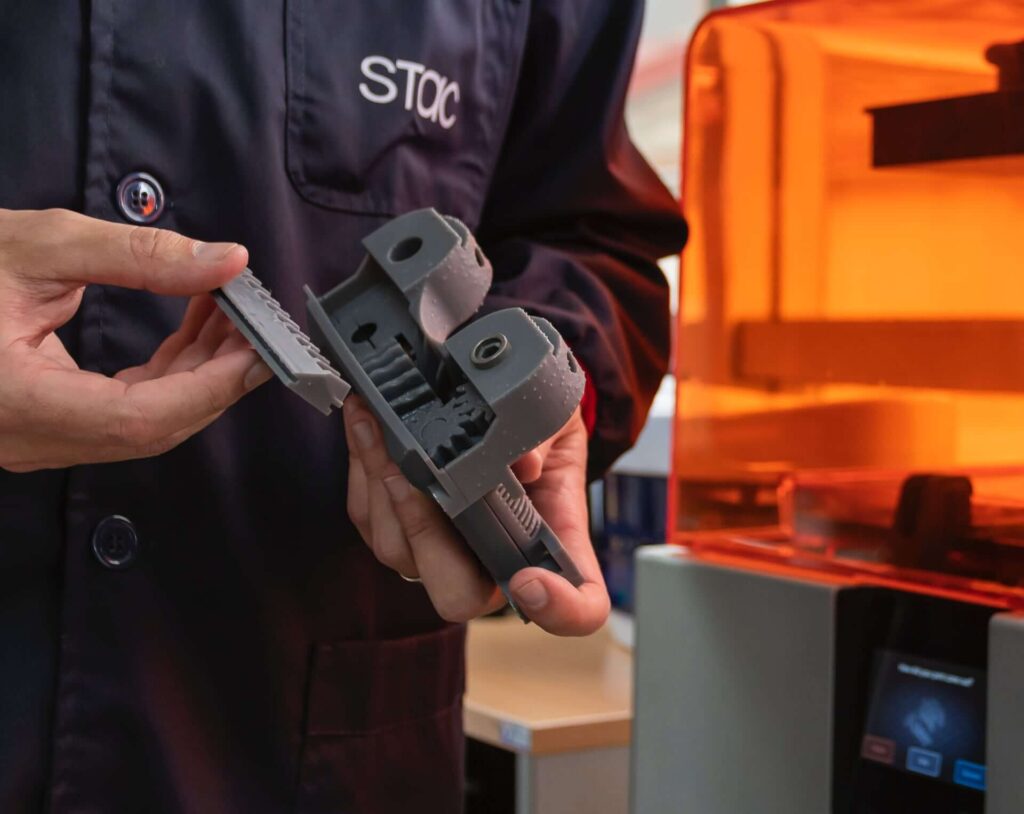
Corte láser
El corte láser es un proceso de fabricación sustractiva (se elimina material), con el que se puede grabar o cortar acero, aluminio, plástico, madera, cartón, etc. El láser es un foco de luz muy potente, y concentrado de forma precisa en un área muy pequeña; esto hace que en esa área se genere de forma inmediata una elevada temperatura, como cuando usamos una lupa para concentrar los rayos del sol sobre un único punto. Este punto de calor crea un calentamiento, fusión y vaporización parcial o total del material de trabajo. Al estar concentrado, la zona afectada es pequeña, y las zonas cercanas apenas sufren modificaciones, lo que genera cortes más limpios en comparación con otros procesos de fabricación existentes. Las trayectorias del láser son programadas y gestionadas digitalmente, lo que asegura su precisión y repetibilidad.
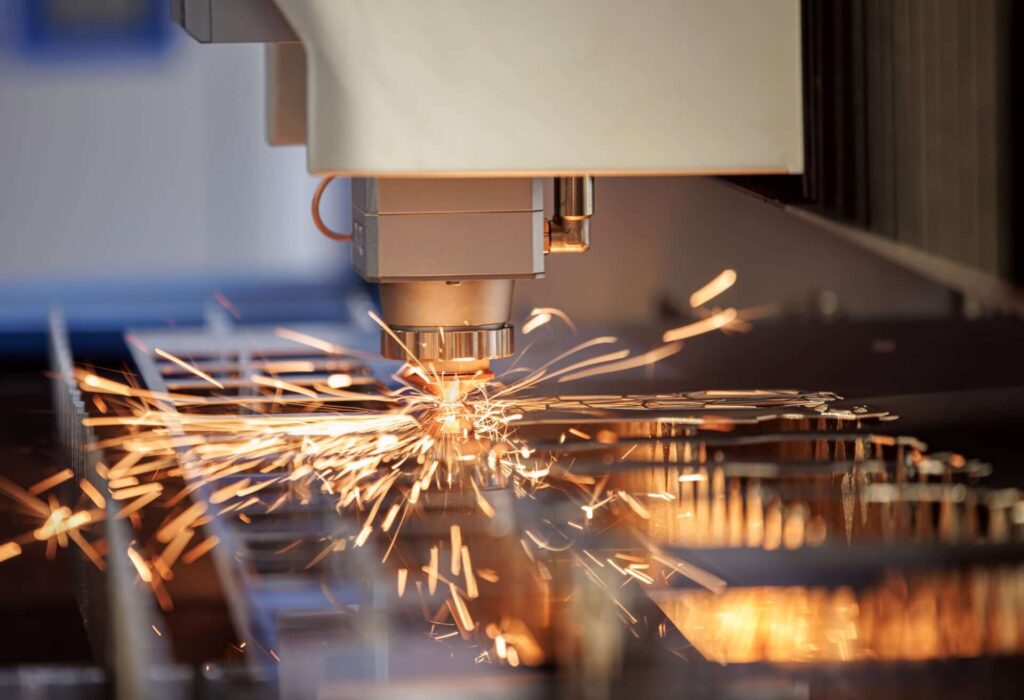
Forja de latón
La forja del latón es un proceso de estampación en caliente que consiste en deformar un trozo de barra de latón (a alta temperatura) mediante matrices que la dotan de una forma determinada mediante la presión ejercida por una prensa. Es uno de los procesos más antiguos de trabajo con metales, y por tanto cobran mucha importancia la temperatura a la que ponemos el material previamente a su conformado, y la composición de este.
Una mayor temperatura facilita el conformado (requiere menos presión), pero esta debe estar dentro de unos límites, asegurando uniformidad y sin llegar a la fusión. La composición modifica las propiedades del material, afectando tanto para su conformado como a la funcionalidad de la pieza final, y se debe escoger para cada caso la aleación más adecuada. También es fundamental el correcto estado de la prensa y de las matrices, para asegurar la calidad del proceso.
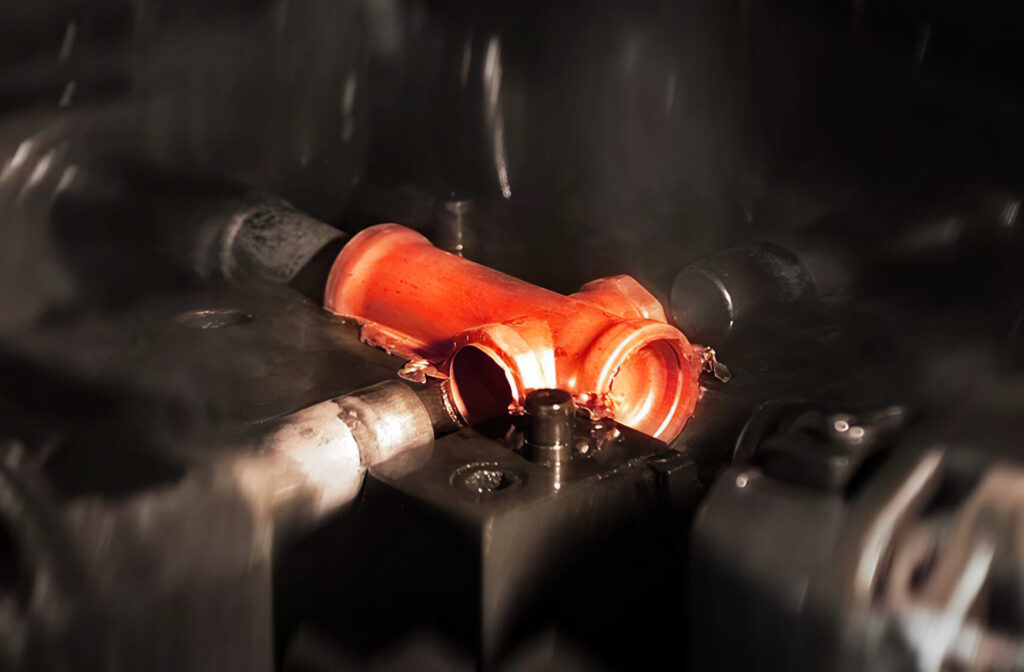
Forja de aluminio
La forja de aluminio es un proceso de estampación en caliente en el que se da forma a una plancha de aluminio (a alta temperatura) en el interior de una prensa, mediante esfuerzos transmitidos al material por matrices que calcan la forma final deseada. Tienen mucha importancia la temperatura a la que introducimos el material, y la composición de este; pero también todos los parámetros de la máquina y las matrices, que van a marcar el acabado final de la pieza y su homogeneidad interior. Además las características mecánicas de la pieza final son muy buenas.
En STAC llevamos años desarrollando piezas asociadas a este proceso, asegurando la calidad de las piezas y el correcto funcionamiento de las prensas y utillajes de forja de aluminio.
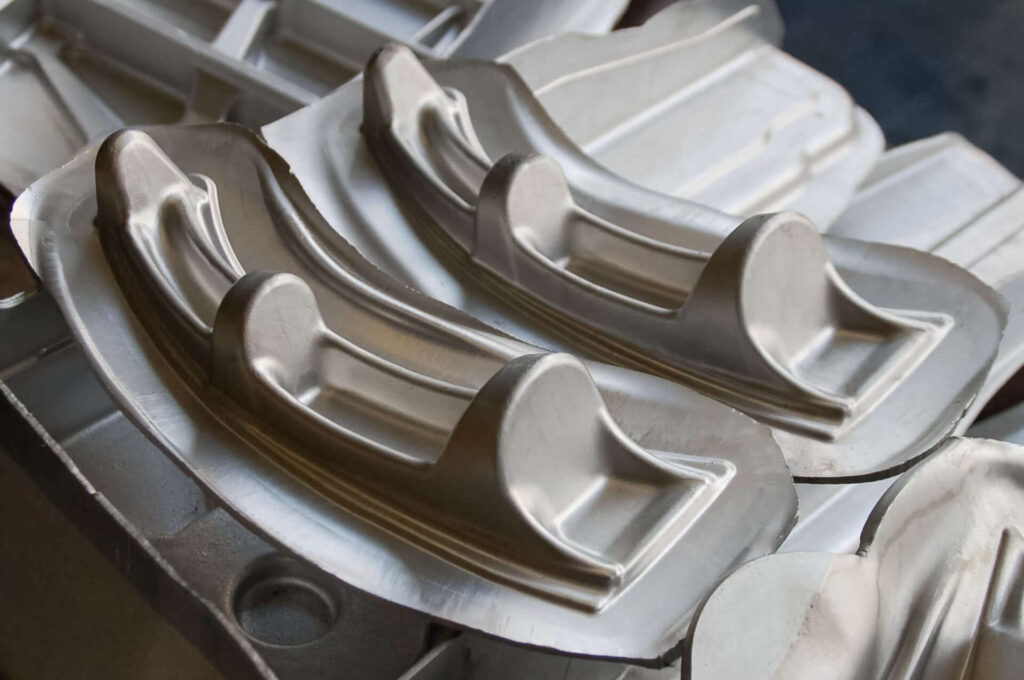
Inyección MIM
El proceso de inyección de metal MIM (Metal Injection Molding) es un proceso industrial novedoso que permite alta productividad y mucha versatilidad dimensional al poder moldear piezas como un termoplástico ofreciendo unas prestaciones mecánicas excelentes al tratarse finalmente de piezas macizas metálicas.
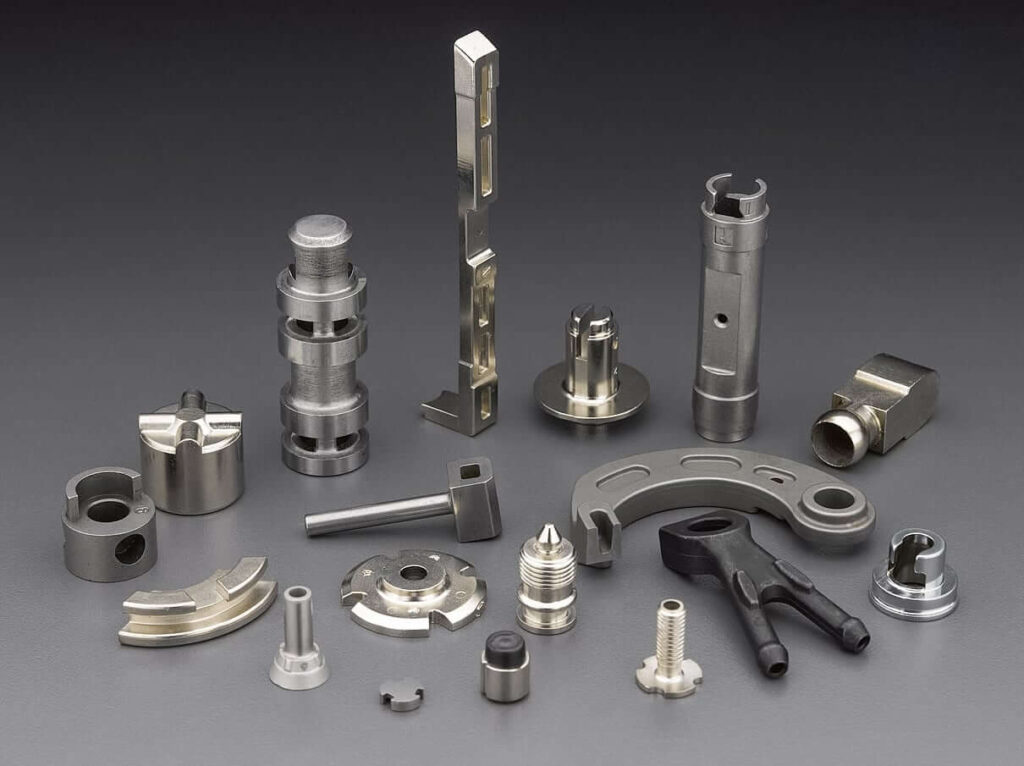
Inyección a alta presión de latón (HPDC)
La inyección a alta presión de latón (HPDC), es un proceso de fabricación que consiste en la introducción de latón fundido, mediante el movimiento de un pistón generalmente, en el interior de una cavidad o molde de acero, con el fin de que este copie sus formas y las adquiera una vez solidificado. Es un proceso muy similar a la inyección de aluminio esto nos permite utilizar nuestros conocimientos de manera directa a la inyección de latón, aunque siempre debemos de tener ciertas consideraciones especialmente derivadas de la mayor temperatura requerida en el proceso ya que el latón funde a 940ºC.
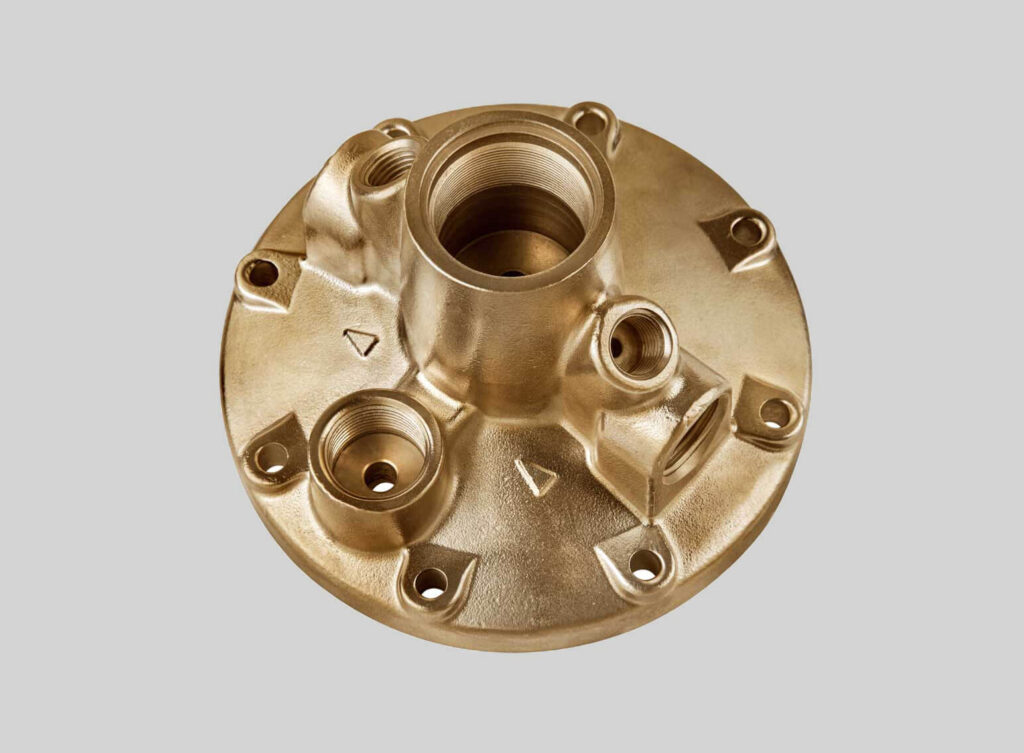
Fabricación por moldeo a cera perdida
Es un proceso de fabricación de los más antiguos. Partiendo de un modelo de cera con la forma final que se busca, se rodea de una gruesa capa de material refractario que se solidifica, y una vez endurecido, se mete en un horno para derretir la figura de cera, que sale de la cavidad por unos orificios. En el lugar de la cera, se inyecta el metal fundido, que adopta la forma exacta del modelo de la pieza. Finalmente, para extraer la pieza final, es necesario retirar el molde, de forma destructiva.
El proceso de cera perdida permite la fabricación de piezas de acero de mayor tamaño que el proceso de inyección MIM pero por el contrario nos proporciona peores tolerancias dimensionales y peor acabado superficial. Esto generalmente nos lleva a que las piezas necesiten de procesos secundarios como el lijado y el mecanizado para conseguir la pieza final. Además, las cadencias de producción son menores a no ser que se desarrollen instalaciones industriales tipo carrusel que permitiría aumentarlas.
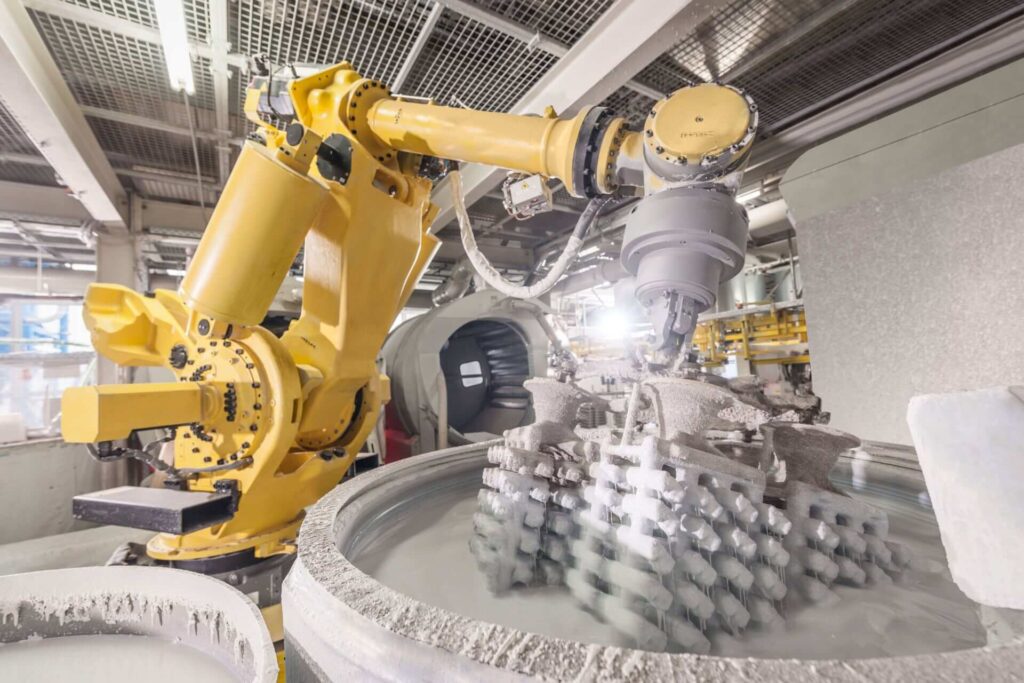
Fabricación por moldeo por gravedad
El moldeo por gravedad es un proceso de fabricación industrial, también llamado moldeo en coquilla o moldeo en molde permanente. Consiste en el vertido del metal en el molde (normalmente utilizamos aluminio) a presión atmosférica, no a presión, a diferencia de los procesos de moldeo por inyección. El metal copia la forma del molde y tras la solidificación, se abre el molde y se obtiene la pieza. Apareció para sustituir al moldeo en arena, y es muy utilizado para la fabricación de piezas hechas de metales no ferrosos como pueden ser aleaciones de aluminio, cobre, magnesio o zinc.
El moldeo por gravedad sigue siendo normalmente muy manual en su operación, pero la apertura y cierre de los moldes si está automatizada mediante mecanismos neumáticos o hidráulicos. Pese a todo esto, continúa siendo un proceso recomendado para series pequeñas o medianas, por su elevado coste en comparación a otros sistemas de moldeo a alta presión.
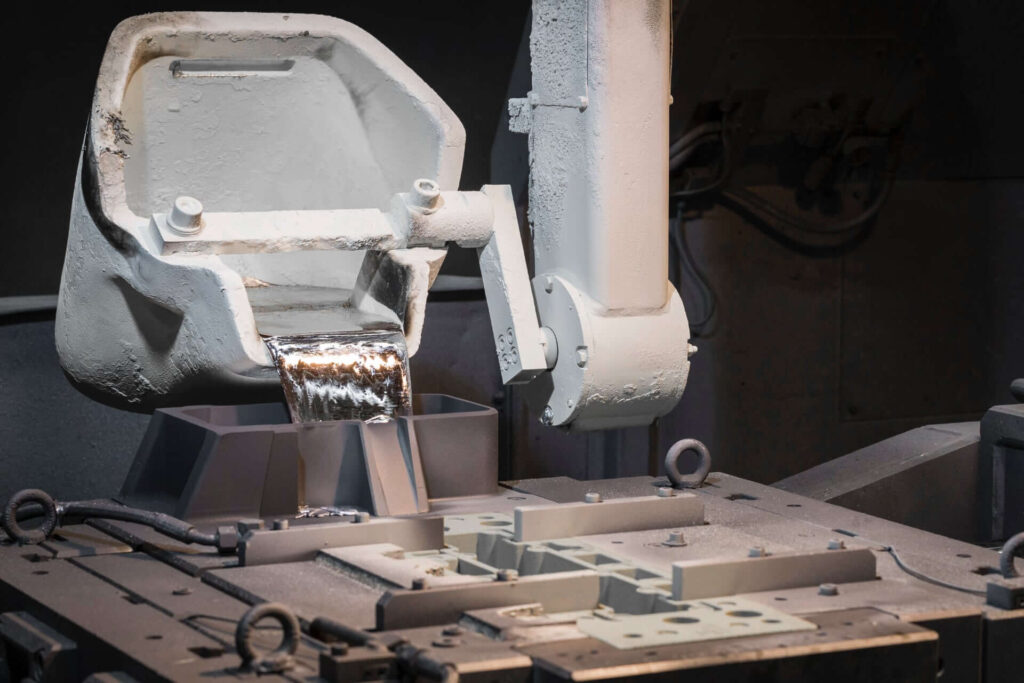
Contacta con nosotros
Te daremos asistencia para tus proyectos y resolveremos tus dudas lo antes posible