
Other manufacturing processes
At STAC we have the ability to offer other essential manufacturing processes for a part to meet its technical requirements with the necessary finish and quality. Our team of experts will be able to offer you solutions adapted to your project’s requirements.
Additive manufacturing
Unlike traditional (subtractive) manufacturing that starts from a piece of material and removes some of it to obtain the final form, additive manufacturing owes its recent popularity to its ability to obtain a final shape by adding material in layers, in the correct and necessary amount, in a fully automated manner based on a digital design. This process does not require tools, tooling or auxiliary machines, which makes it very simple and accessible, both for customer and manufacturer.
The most popular and widespread method of additive manufacturing is also called 3D printing of plastics, which can start with raw materials in the form of spooled filament, granules, liquid resins, etc. Additive manufacturing can also be applied to metals, but this is less well-known as it is currently only used in industrial settings. There are many technologies for each material, each with its own advantages and disadvantages; the keys to choose correctly lie in the experience, design and functionality of the parts to be produced. This method can be used to manufacture anything from small to medium or large series, all depending on the capacity of the machine, its degree of automation and the production process.
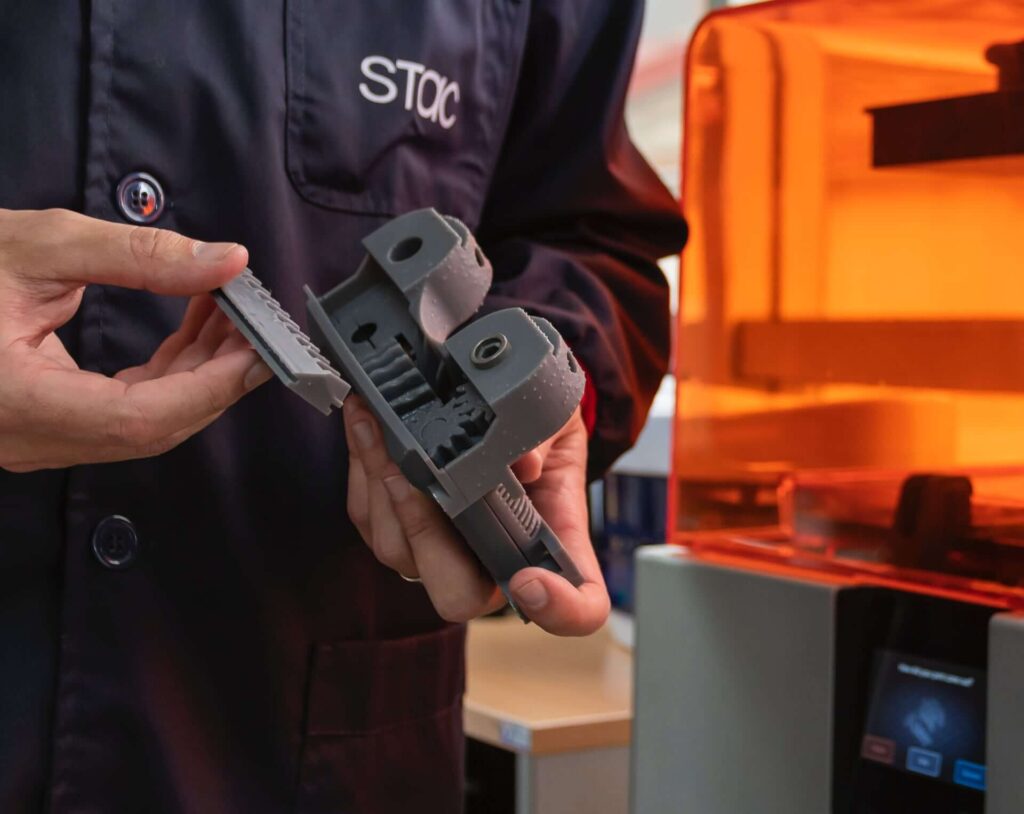
Laser cutting
Laser cutting is a subtractive manufacturing process (material is removed), with which steel, aluminium, plastic, wood, cardboard, etc. etc. can be engraved or cut. The laser is a very powerful focus of light, precisely concentrated in a very small area; this immediately generates a high temperature at that point, similar to when we use a magnifying glass to concentrate the sun’s rays on a single point. This hot spot heats, melts and vaporises the working material, either partially or completely. Being concentrated, the affected area is small, and nearby areas are hardly modified, resulting in cleaner cuts compared to other existing manufacturing processes. The path of the laser is programmed and controlled digitally, ensuring accuracy and repeatability.
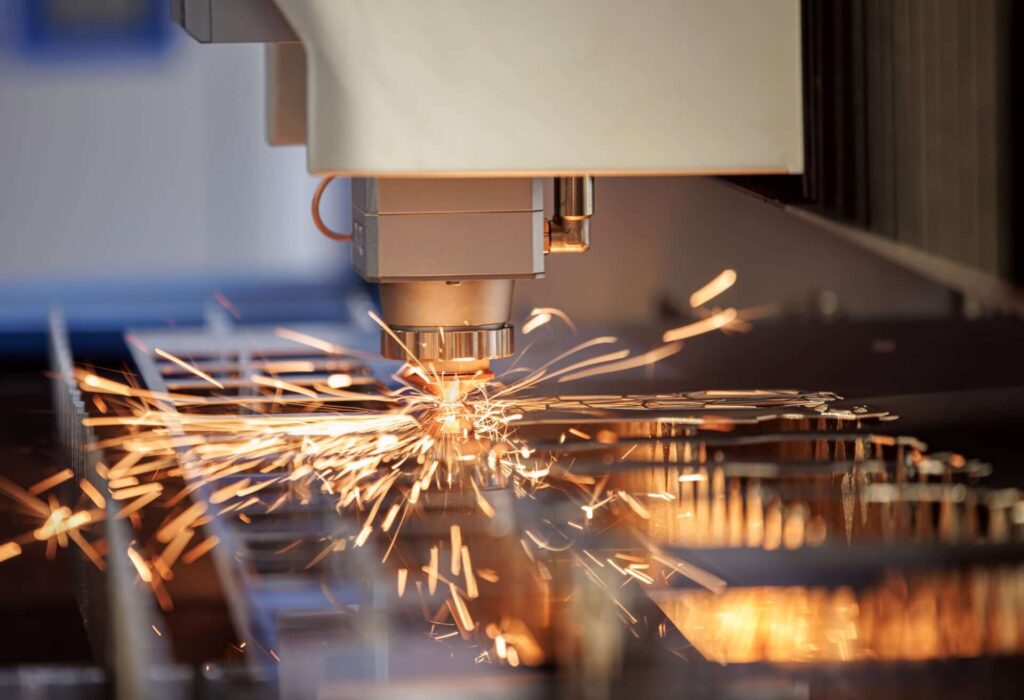
Brass forging
Brass forging is a hot stamping process that consists of shaping a piece of brass bar (at high temperature) by means of dies and the pressure exerted by a press to give it a specific shape. It is one of the oldest processes of working with metals, and therefore the temperature to which the material is heated before forming, and the composition of it, become very important.
A higher temperature makes forming easier (requires less pressure), but this must be within limits, ensuring uniformity and avoiding complete melting. The composition modifies the properties of the material, affecting both its ability to be formed and the functionality of the final piece, and the most appropriate alloy must be chosen for each case. It is also essential that the press and the dies are in good order to ensure the quality of the process.
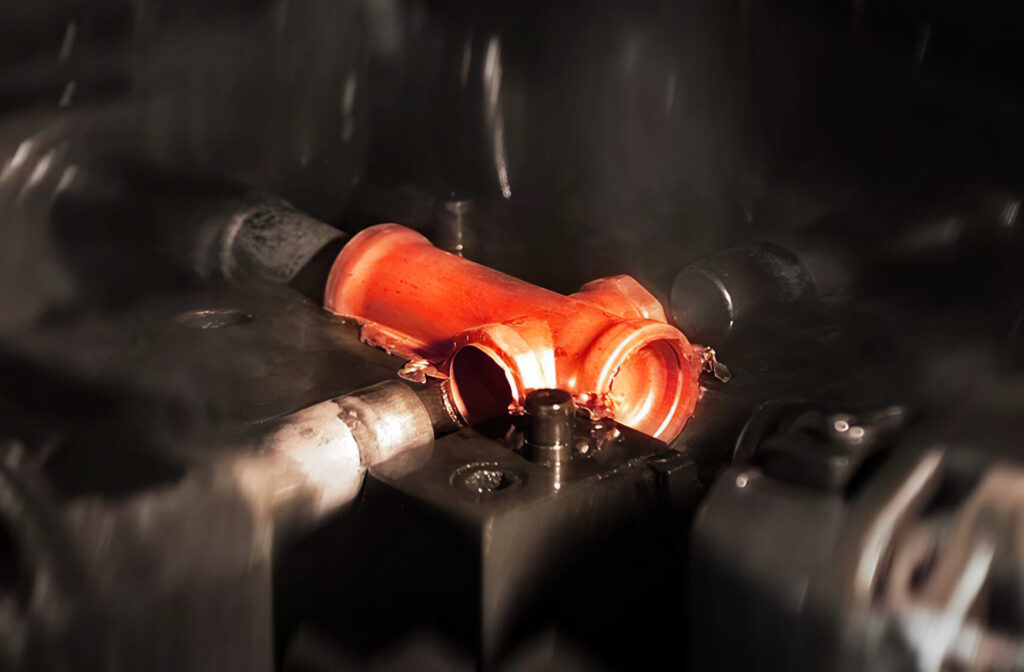
Aluminium forging
Aluminium forging is a hot stamping process in which an aluminium sheet (at high temperature) is formed inside a press, through the force transmitted to the material using dies to reproduce the desired final shape. The temperature at which we introduce the material, and the composition of it, are very important; as are all the parameters of the machine and the dies, which will be responsible for the final finish of the piece and its interior homogeneity. In addition, the mechanical characteristics of the final piece are very good.
At STAC we have been developing parts using this process for years, ensuring the quality of the parts and the correct operation of the aluminium presses and forging tools.
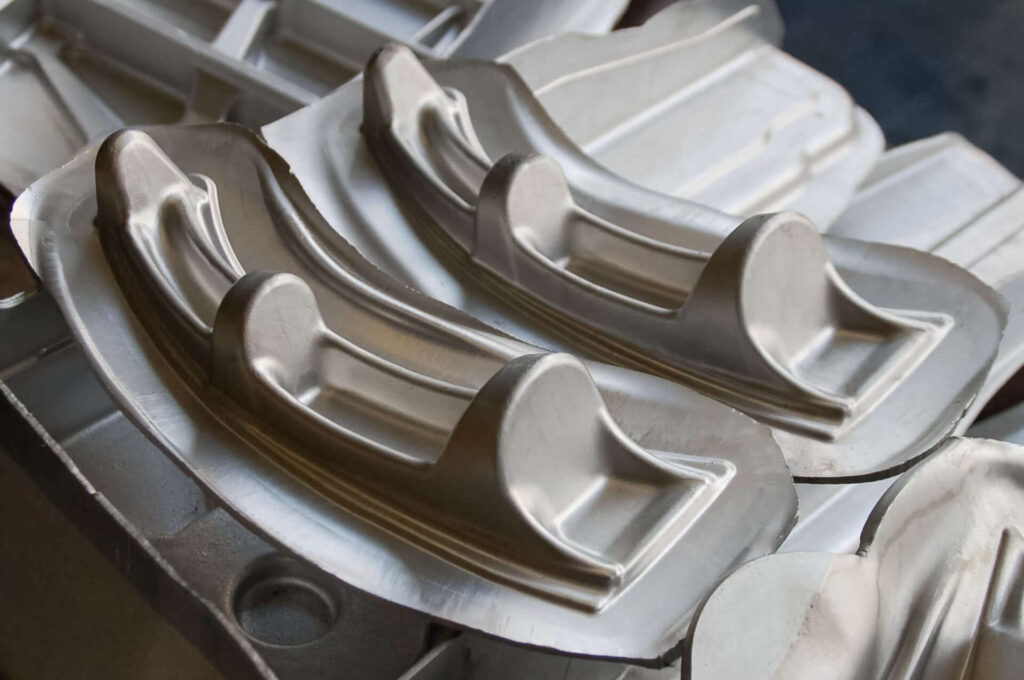
MIM Injection
The metal injection process (MIM) is a novel industrial process that allows high productivity and a lot of dimensional versatility by being able to mould parts in a similar way to thermoplastics, providing excellent mechanical performance as they are solid metal parts at the end of the process.
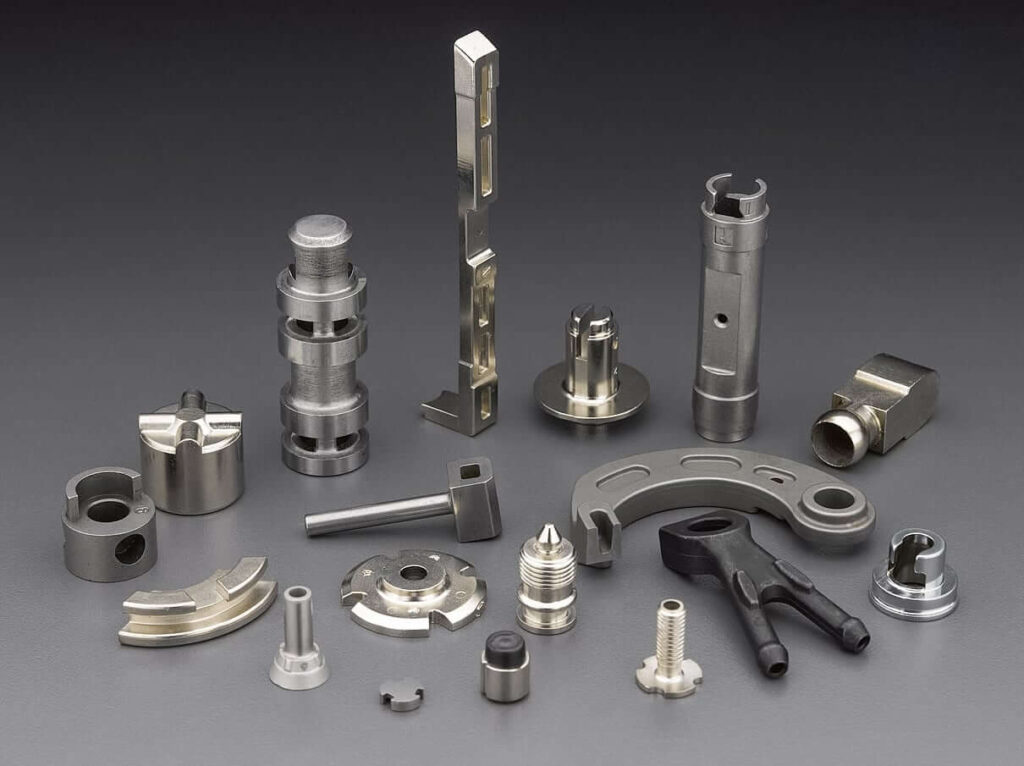
High Pressure Brass Injection (HPDC)
High pressure brass injection (High Pressure Die Casting), is a manufacturing process consisting of the introduction of molten brass, usually by the movement of a piston, into a cavity or steel mould (the die), in order for it to copy the forms and retain them once solidified. The process is very similar to aluminium injection and this allows us to apply our know-how directly to the brass injection process, although we must always make certain considerations, especially those that relate to the higher temperature required in the process (brass melts at 940ºC).
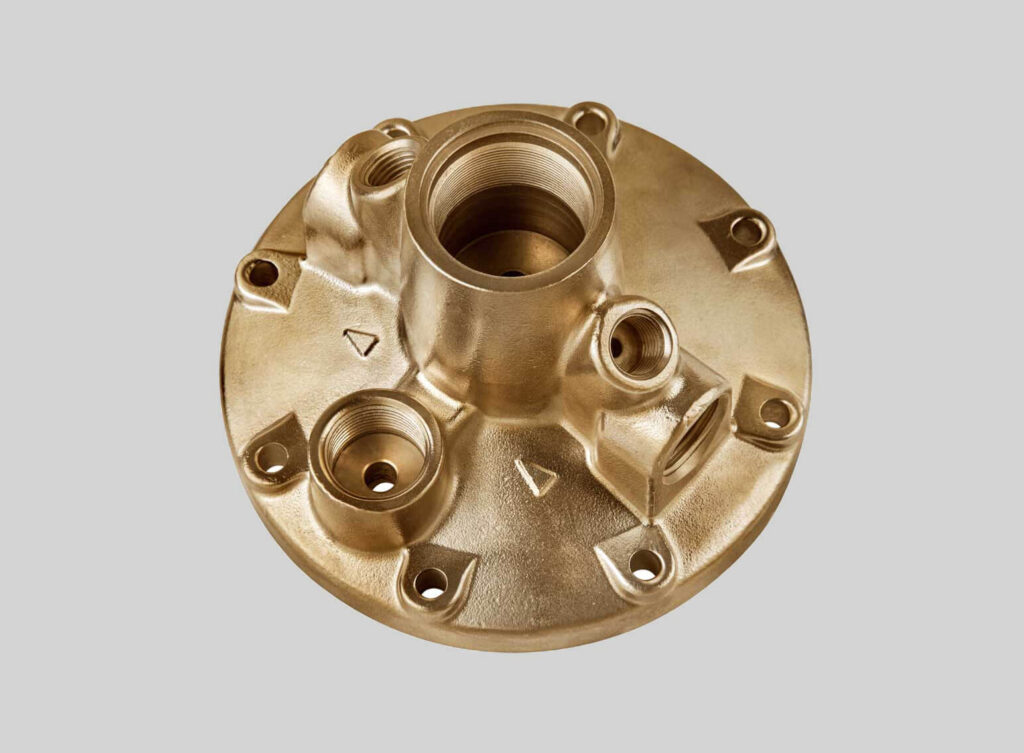
Lost wax moulding
It is one of the oldest manufacturing processes. Starting with a wax model with the final shape that is sought, it is surrounded by a thick layer of refractory material that solidifies, and once hardened, it is put in a furnace to melt the wax figure; the wax exits the cavity via drain holes. Molten metal is injected into the cavity made by the wax, adopting the exact shape of the part’s blank. Finally, to extract the final part, it is necessary to remove the mould, which means that it is destructed.
The lost wax process allows the manufacture of steel parts larger than the MIM injection process. However, the dimensional tolerances and surface finish are not as good. This usually means that the parts require secondary processes such as sanding and machining to obtain the finished part. In addition, production rates are lower unless industrial carousel-like facilities are developed that would allow increased output.
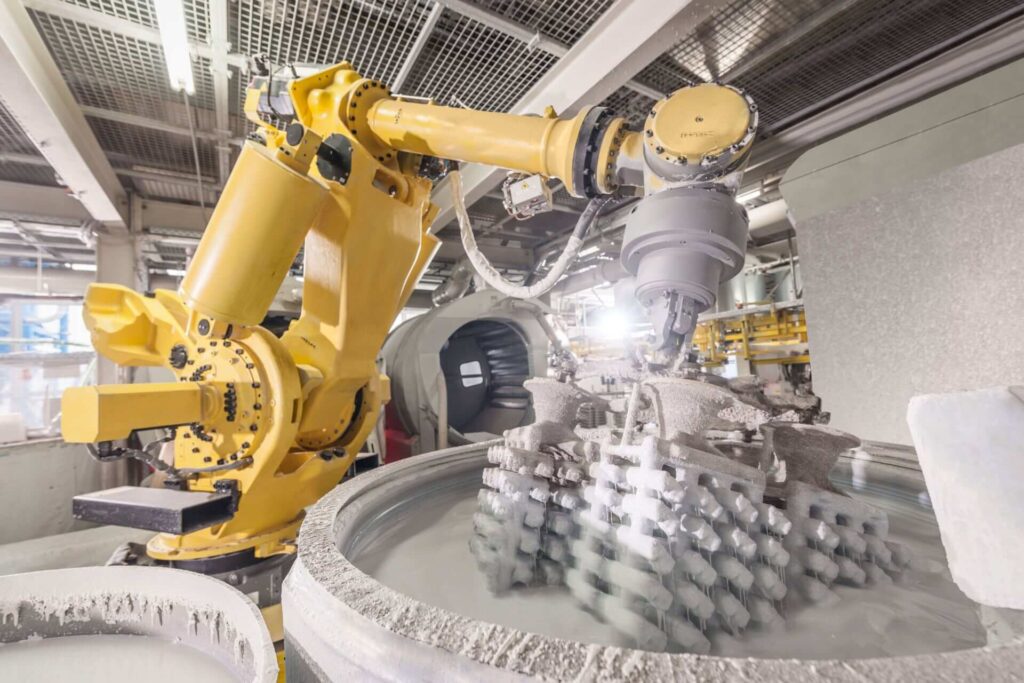
Gravity die casting
Gravity casting or moulding is an industrial manufacturing process. It consists of pouring the metal into the mould (normally we use aluminium) at atmospheric pressure, unlike injection moulding processes, which are done under high pressure. The metal copies the shape of the mould and after solidification, the mould is opened and the piece is obtained. It arose to replace sand moulding, and is widely used for the manufacture of parts made of non-ferrous metals such as aluminium, copper, magnesium or zinc alloys.
Gravity moulding is usually still performed manually, but the opening and closing of the moulds can be automated by pneumatic or hydraulic mechanisms. Despite all this, it remains a recommended process for small or medium manufacturing runs, due to its high cost compared to other high pressure moulding systems.
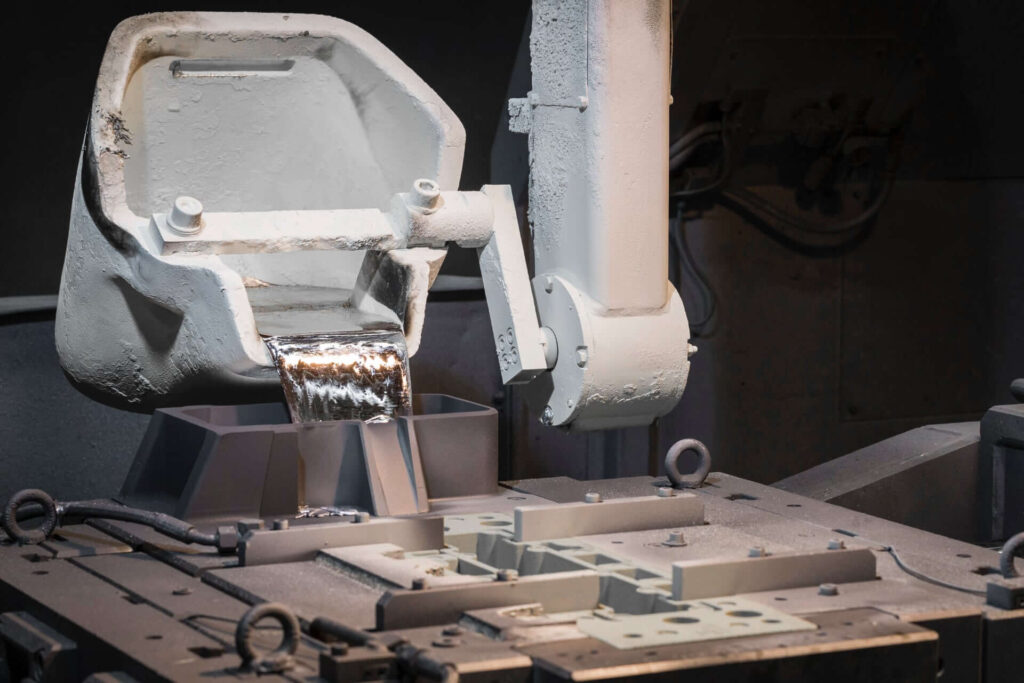
Contact us
We’ll be happy to provide help for your projects and resolve any doubts as soon as possible