PROCESSUS PRIMAIRES
Zamak moulé sous haute pression
Chez STAC, nous sommes spécialisés dans la fabrication de pièces moulées par injection de zamak. Nous accompagnons nos clients tout au long du processus de fabrication, depuis la conception du design jusqu’à la production en série des pièces en zamak.
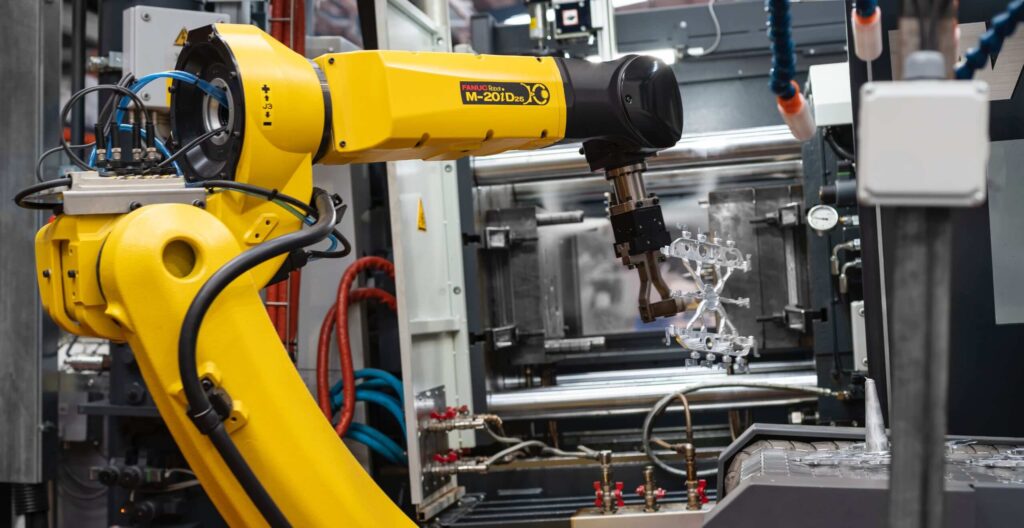
PROCESSUS PRIMAIRES
Zamak moulé sous haute pression
Chez STAC, nous sommes spécialisés dans la fabrication de pièces moulées par injection de zamak. Nous accompagnons nos clients tout au long du processus de fabrication, depuis la conception du design jusqu’à la production en série des pièces en zamak.
Qu’est-ce que l’injection de zamak ?
Le zamak est un alliage de zinc, d’aluminium, de magnésium et de cuivre. Son nom provient des premières lettres des métaux qui le composent : Zn (zinc), Al (aluminium), MA (magnésium) et K (cuivre en allemand, « Kupfer »). Il est principalement utilisé dans la fabrication de pièces métalliques par moulage sous pression. Les pièces fabriquées par moulage sous pression du zamak présentent les caractéristiques suivantes :
- Durabilité : le zamak est résistant et durable, ce qui en fait un matériau approprié pour les applications nécessitant une résistance élevée à l’usure.
- Malléabilité : il est facile à mouler et à façonner, ce qui permet la production de pièces aux conceptions complexes et aux détails précis.
- Finition de surface : le zamak offre des finitions de surface de haute qualité telles que le laquage, le chromage, le nickelage, le PVD, etc.
- Basse température de fusion : contrairement à d’autres métaux, le zamak a une faible température de fusion, ce qui le rend facile à traiter et à couler.
Vous voulez savoir comment ?
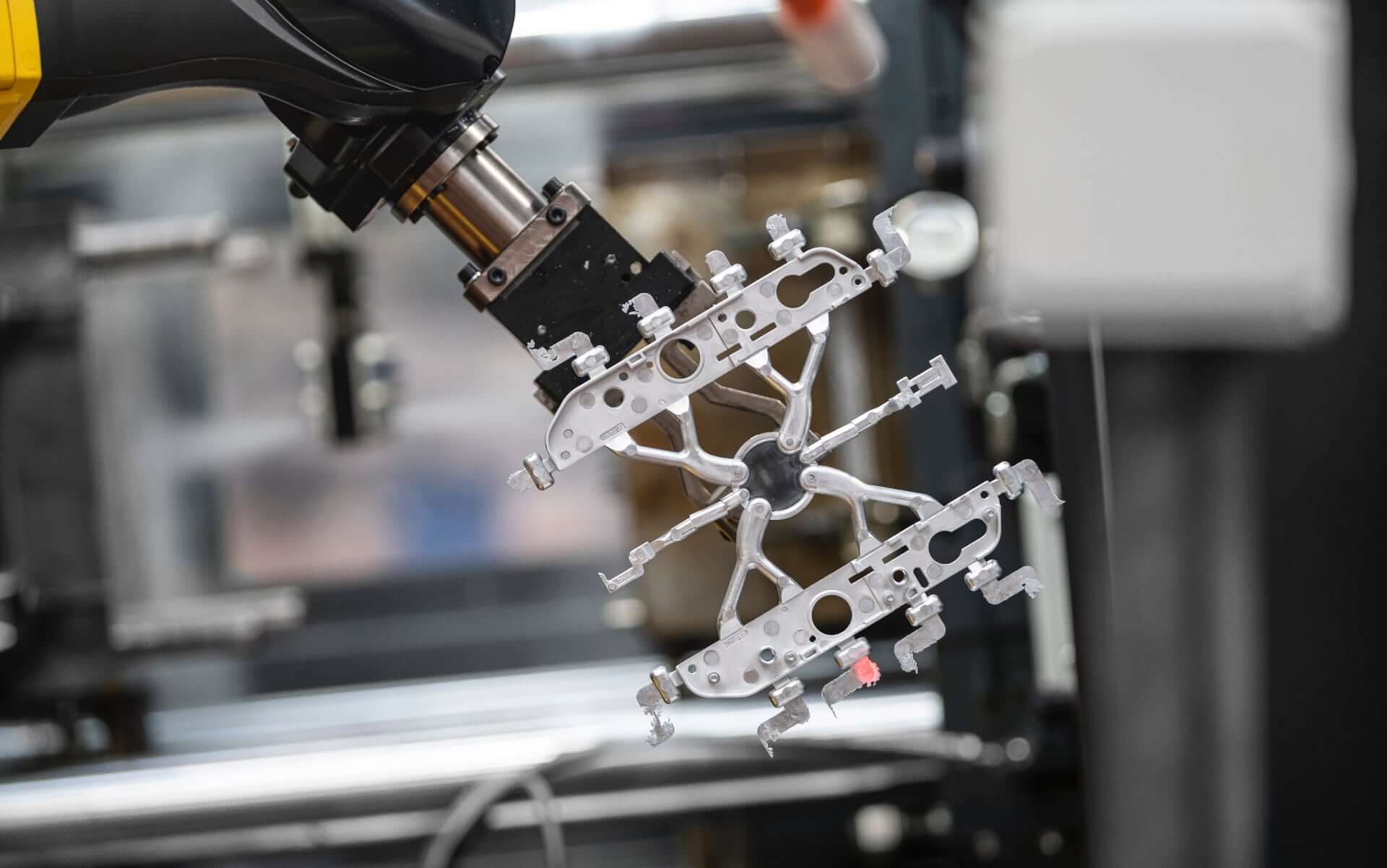
Les étapes de l’injection de zamak
Ce processus de fabrication comporte de nombreuses étapes communes à tous les processus d’injection de plastique ou d’aluminium. Voici les principales étapes :
- Conception de la pièce : à ce stade, on parle de la conception de la pièce, mais orientée vers le processus d’injection. Il y a de nombreux facteurs à prendre en compte qui sont très différents des autres processus. Nous vous conseillerons.
- Conception et fabrication du moule : matériaux, zone d’injection de la pièce, refroidissement dans le moule, moulage des zones de contre-courant, etc. Un bon moule est synonyme de qualité et de répétabilité de la production.
- Préparation de la machine d’injection : le moule est placé dans une machine d’injection de zamak. La machine dispose d’une chambre de coulée où le matériau zamak sera placé.
- Chauffage et fusion du zamak : le zamak se présente sous la forme de lingots. Il est ensuite chauffé à une température adéquate jusqu’à ce qu’il fonde et devienne liquide.
- Injection du zamak : une fois le zamak en fusion, il est injecté dans le moule à l’aide d’un piston et d’une buse. Le matériau doit rapidement remplir toutes les cavités. Dans ce cas, il est essentiel de disposer de machines automatiques avec contrôle du processus.
- Refroidissement et solidification : après l’injection, le zamak est refroidi à l’intérieur du moule. La vitesse de refroidissement peut être contrôlée pour s’assurer que le matériau se solidifie correctement et prend la forme du moule.
- Ouverture du moule et retrait de la pièce : une fois que le zamak a refroidi et s’est solidifié, le moule est ouvert et la pièce finale est retirée. À ce stade, la pièce peut nécessiter certains processus supplémentaires, tels que l’ébavurage, l’usinage ou la finition de surface.
- Recyclage du zamak : les déchets et l’excédent de zamak sont collectés et réutilisés.
- Le processus d’injection du zamak offre des avantages tels qu’une grande précision dans les détails, une production rapide et efficace, ainsi que la possibilité de créer des pièces complexes avec une excellente qualité de surface.
Chez STAC, nous sommes experts dans ce processus. Et nous vous accompagnons dès le début pour faire de votre projet une réussite.
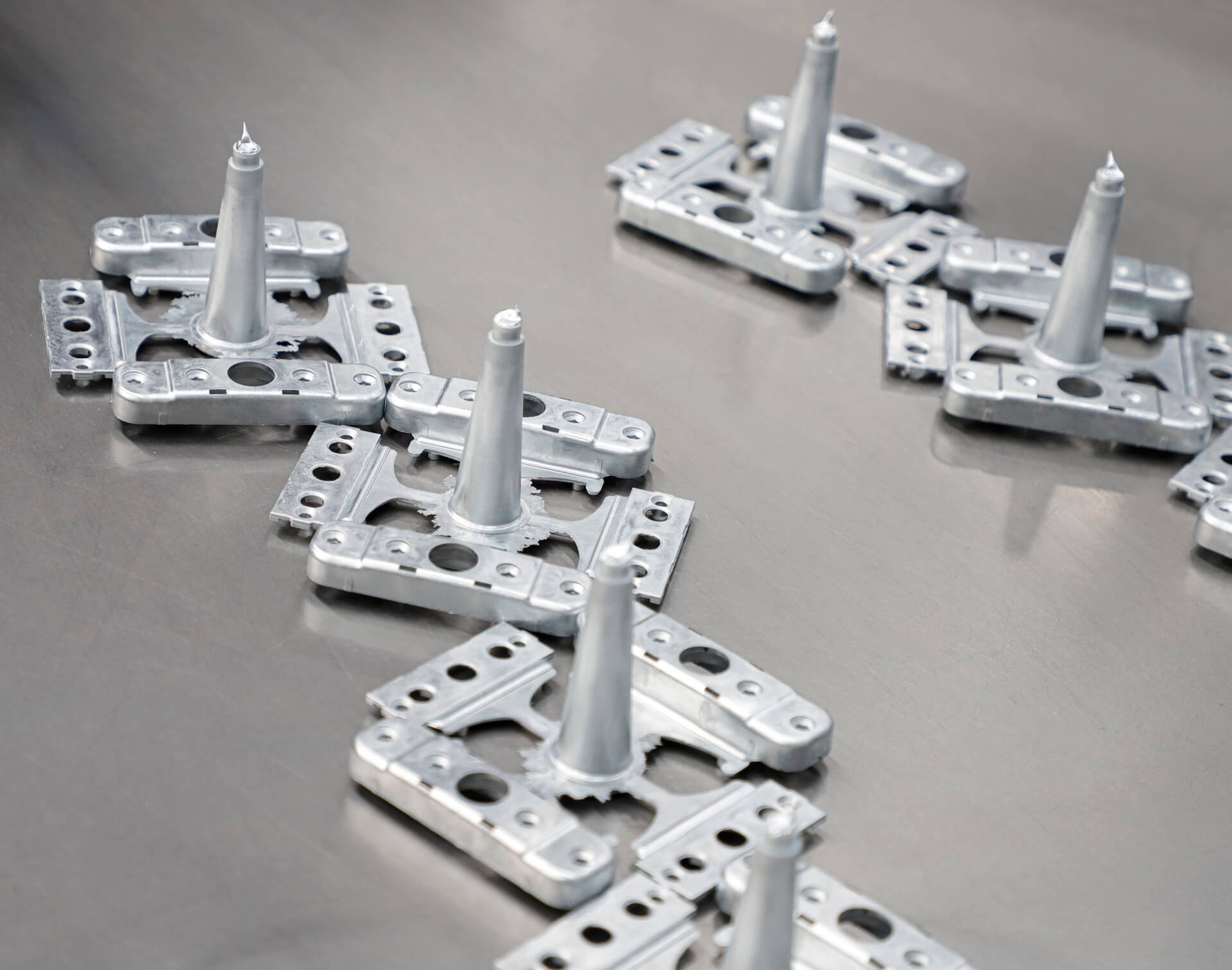
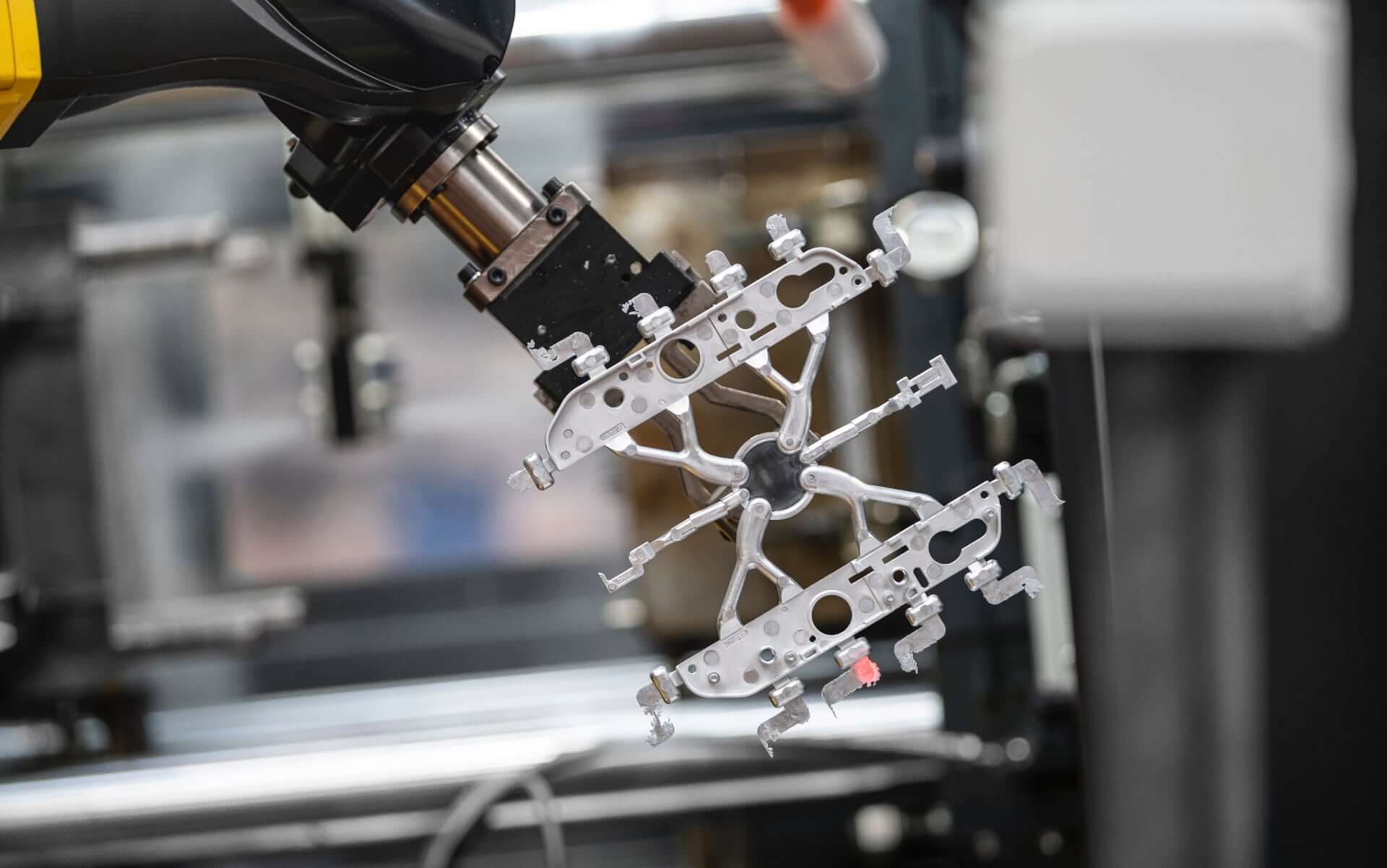
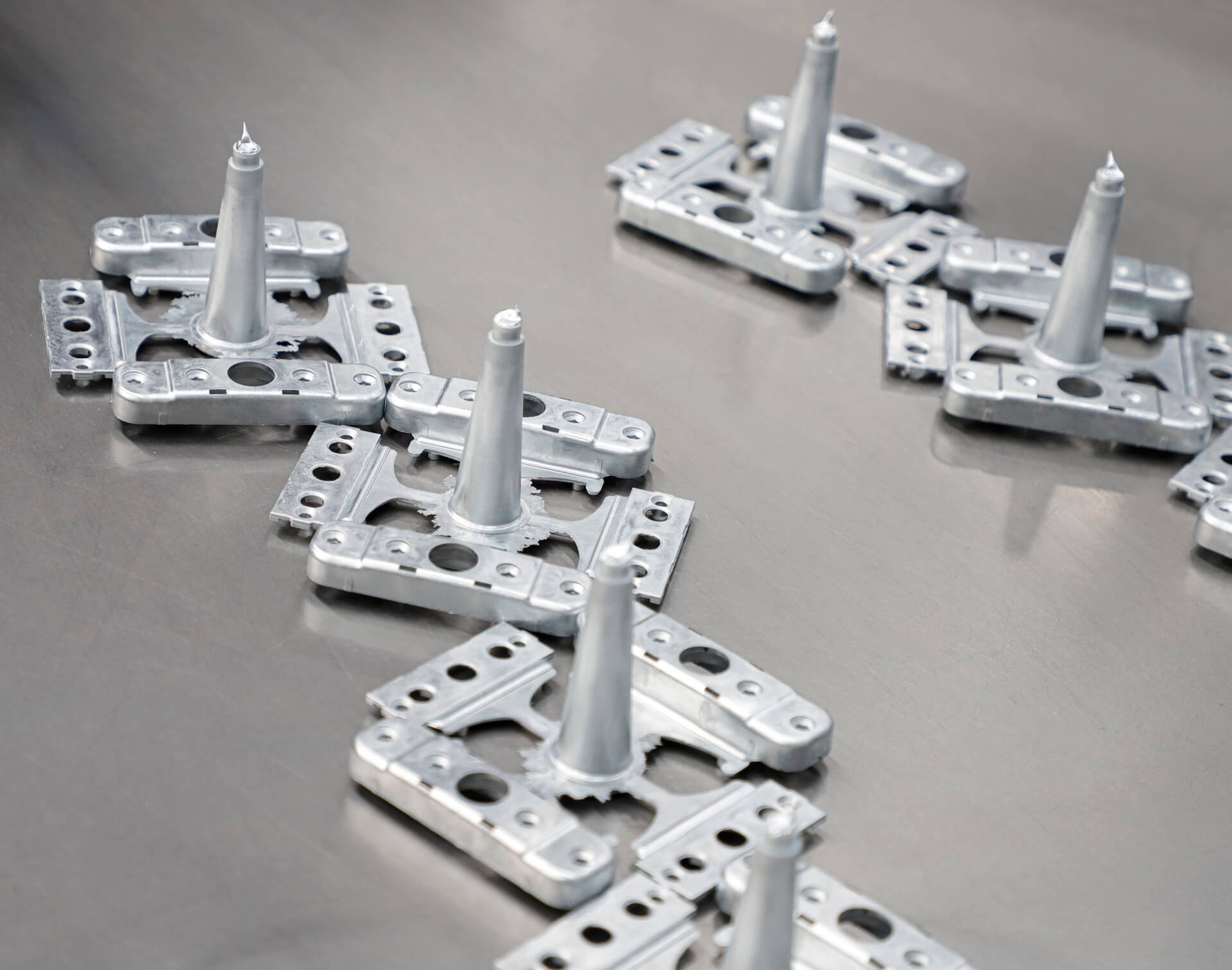
Questions fréquemment posées sur l’injection de zamak
Le zamak 5 est sans doute le plus utilisé dans l’industrie.
Il existe d’autres alliages qui améliorent le zamak 5 dans des caractéristiques très spécifiques, comme la fluidité.
Par exemple : le zamak 5 et le zamak 12. Zamak 5
- Bonne résistance à la corrosion.
- Résistance mécanique plus élevée.
- Applications industrielles et composants structurels : il est couramment utilisé dans les applications industrielles, telles que les composants de machines et les pièces structurelles qui nécessitent une plus grande résistance et une plus grande durabilité.
Zamak 12
- Amélioration de la fluidité et du remplissage : le Zamak 12 a une excellente fluidité en raison de sa teneur plus élevée en magnésium. Cela facilite le remplissage des cavités du moule et la reproduction des détails complexes de la pièce.
- Haute précision et pièces minces : grâce à sa capacité à s’écouler facilement dans le moule, le zamak 12 est idéal pour la fabrication de pièces aux parois minces ou aux détails complexes. Si votre pièce nécessite des tolérances serrées ou des caractéristiques de conception délicates, le zamak 12 peut offrir une plus grande précision et un meilleur état de surface.
- Applications électriques et électroniques : utilisé dans la fabrication de composants électriques et électroniques, tels que les connecteurs, les fiches et les pièces d’appareils électroniques, en raison de sa fluidité et de sa capacité à reproduire des détails fins.
Si vous souhaitez en savoir plus sur les matériaux, n’hésitez pas à nous contacter.
Le zamak est injecté à l’état liquide à une température de 420 ºC. Les moules doivent donc être fabriqués avec des aciers spéciaux pour le travail à chaud. Chez STAC, nous disposons d’un département de fabrication d’outillage qui est responsable de la conception, de la fabrication du moule et de son entretien tout au long de sa vie utile. Les caractéristiques les plus importantes à prendre en compte sont les suivantes :
- Matériaux pour les différentes parties du moule : ces matériaux doivent être suffisamment solides et durables pour résister aux pressions et températures élevées du processus d’injection.
- Plaques de moule : le moule se compose d’une cavité et d’un noyau qui définissent la forme de la pièce à injecter. Ces pièces doivent être précises et avoir une finition de surface de haute qualité pour assurer la reproductibilité et la qualité des pièces.
- Système de refroidissement : Le moule d’injection en zamak doit avoir un système de refroidissement efficace pour contrôler la température du moule pendant le processus. Cela permet d’assurer une solidification adéquate du zamak et un cycle de production efficace.
- Canaux d’alimentation et débordements : le moule doit comporter des canaux d’alimentation pour permettre au zamak en fusion d’entrer dans la cavité du moule. En outre, des zones de débordement sont nécessaires autour du périmètre de la pièce pour faciliter l’évacuation de l’air et des impuretés pendant le processus d’injection.
- Résistance à l’usure : comme le zamak fondu peut exercer des contraintes et des forces importantes sur le moule, il est essentiel que le moule ait une résistance à l’usure adéquate et prévoie des cales interchangeables sur les parties les plus faibles de l’outillage. Cela garantit une longue durée de vie du moule et une qualité constante des pièces.
Les moules en acier sont peut-être les outils les plus techniques que nous fabriquons et les plus difficiles à entretenir. STAC garantit à ses clients le moule pendant toute la durée de vie de l’outillage. Si vous souhaitez en savoir plus, nous pouvons vous aider. Contactez nous.
Pour fabriquer des pièces d’injection de zamak de la plus haute qualité, nos machines possèdent les caractéristiques suivantes :
- Haute pression et force de serrage : la machine doit être en mesure de générer et de maintenir une pression d’injection élevée pour assurer un remplissage et un compactage adéquats du zamak dans le moule. De plus, elle doit avoir une force de serrage suffisante pour maintenir le moule en toute sécurité pendant le processus.
- Contrôle précis de la température : la machine doit avoir un système de contrôle précis de la température pour s’assurer que le zamak en fusion conserve la bonne température tout au long du processus d’injection, de la coulée à l’injection. Cela permet d’éviter des problèmes tels qu’un refroidissement prématuré ou des déséquilibres thermiques qui peuvent affecter la qualité des pièces.
- Système d’injection et de dosage de haute précision : elle doit être dotée d’un système d’injection et de dosage qui permet un contrôle précis du volume et de la vitesse d’injection du zamak fondu dans le moule. Cela garantit une distribution uniforme du matériau et évite les problèmes tels que la porosité ou les défauts de remplissage.
- Contrôle de la pression et de la vitesse d’injection : la machine doit être dotée de commandes sophistiquées qui permettent d’ajuster et de contrôler avec précision la pression et la vitesse d’injection. Ceci est essentiel pour s’adapter aux caractéristiques spécifiques du zamak et à la conception de la pièce, assurant ainsi une injection optimale et minimisant les défauts.
- Capacité de surveillance et d’enregistrement : il est important que la machine ait des capacités de surveillance et d’enregistrement des données pour permettre un suivi détaillé des paramètres du processus tels que la température, la pression, la vitesse, la synchronisation, entre autres. Cela facilite l’identification des problèmes potentiels et contribue à l’amélioration continue du processus de fabrication.
- Système d’extraction des gaz d’échappement : l’injection de zamak pouvant générer des gaz et des bulles lors du remplissage du moule, la machine et le moule doivent être dotés d’un système d’extraction des fumées efficace. Cela permet de minimiser la porosité et d’améliorer la qualité des pièces.
- Sécurité : nos machines sont entièrement automatisées, de sorte qu’aucun travailleur n’entre en contact avec les pièces en mouvement lorsqu’elles sont en production. Nous utilisons également les EPI nécessaires pour assurer une protection adéquate dans chaque processus.
Si vous souhaitez en savoir plus sur nos capacités en matière d’injection de zamak, n’hésitez pas à nous contacter.
Solution intégrale de fabrication
Notre objectif est de vous offrir des solutions complètes et de haute qualité pour vos besoins de fabrication. Laissez-nous vous expliquer comment nous prenons en charge chaque étape du processus
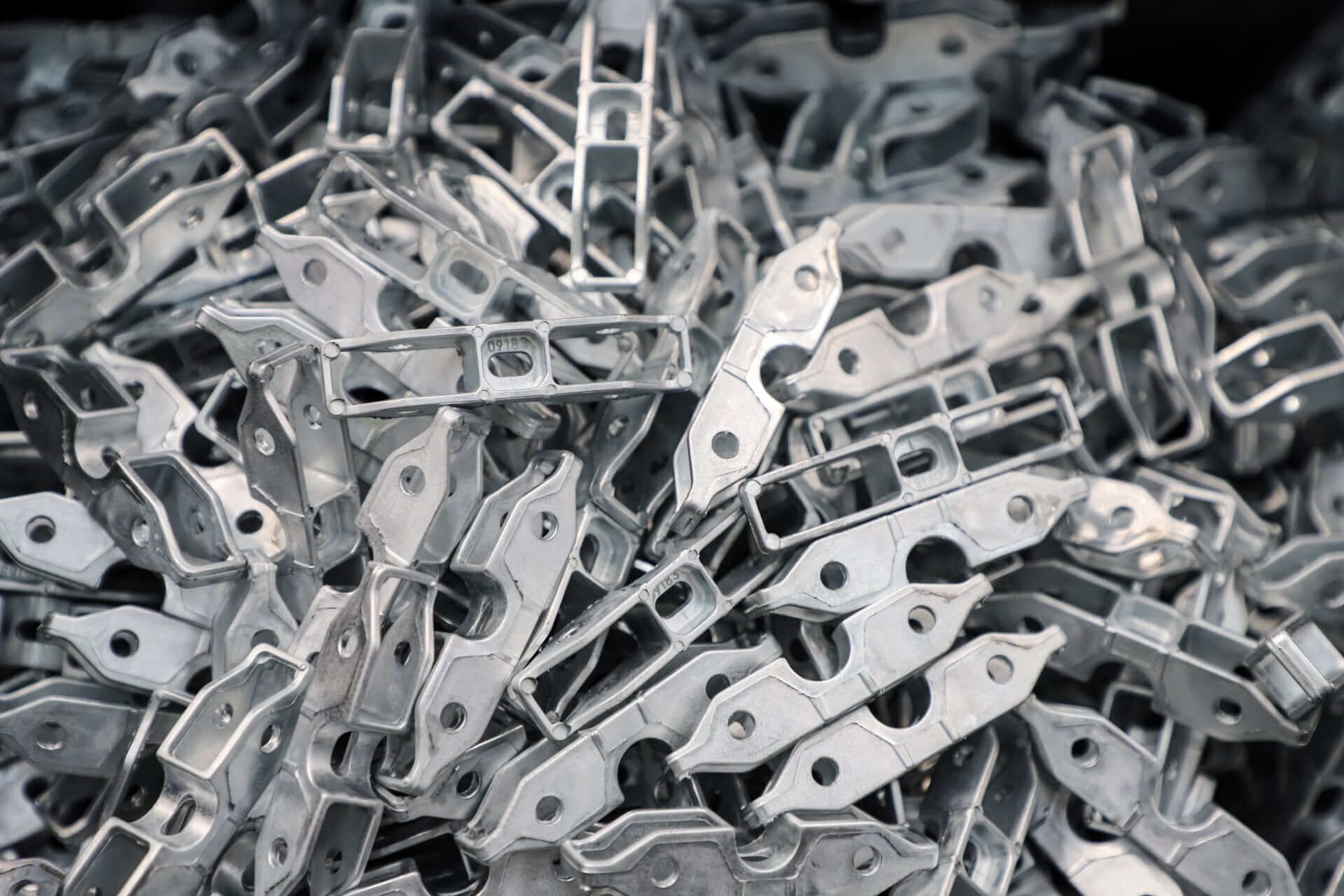
Chez STAC, nous voulons être votre fournisseur unique de pièces d’injection de zamak
Nous voulons vous offrir un service complet et nous prenons en charge l’ensemble du processus, de la conception initiale à la livraison finale du produit fini à l’endroit où vous le demandez.
Notre priorité est d’aider nos clients à atteindre leurs objectifs
Chez STAC, nous nous engageons à atteindre l’excellence et à satisfaire nos clients.
Nous sommes prêts à travailler en étroite collaboration avec vous pour répondre à vos besoins spécifiques.
N’hésitez pas à nous contacter pour discuter de vos projets et de la manière dont nous pouvons vous aider à atteindre vos objectifs.
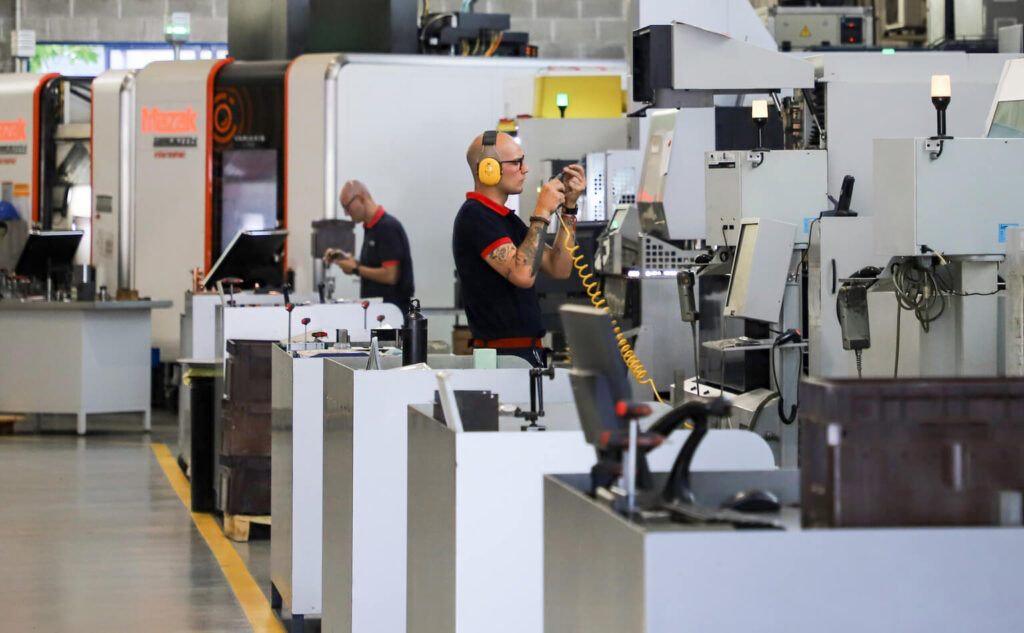
Processus ultérieurs à l’injection de zamak
Après le processus d’injection de zamak, il est courant d’effectuer une série de processus ultérieurs pour obtenir les pièces finales présentant les caractéristiques souhaitées.
Les processus en aval les plus courants dans la fabrication de pièces en zamak sont les suivants
Traitements de surface mécaniques
Comme le grenaillage, qui consiste à éliminer les bavures, les arêtes vives ou les saillies indésirables de la pièce moulée en projetant un abrasif sur la pièce à grande vitesse. Ou le polissage vibratoire, qui est un système de nettoyage et de polissage de la pièce à l’aide d’abrasifs dans un environnement humide.
Traitements décoratifs ou de protection
Comme le zingage électrolytique, qui augmente la résistance à la corrosion des pièces en zamak. Le STAC dispose de différentes technologies et de différentes finitions. Ou la peinture en poudre, qui est un processus de finition et de revêtement pour les pièces visibles. Ce processus améliore à la fois l’esthétique et la résistance à la corrosion des pièces.
Assemblage avec d’autres pièces
Chez STAC, nous disposons de lignes manuelles et automatiques pour l’assemblage de systèmes et d’ensembles, ce qui nous permet d’expédier des produits assemblés, prêts à être montés immédiatement à leur destination. Avec la possibilité de former des kits avec d’autres composants provenant de nous ou de nos clients.
Contactez-nous
Nous vous assisterons dans vos projets et répondrons à vos questions dans les meilleurs délais