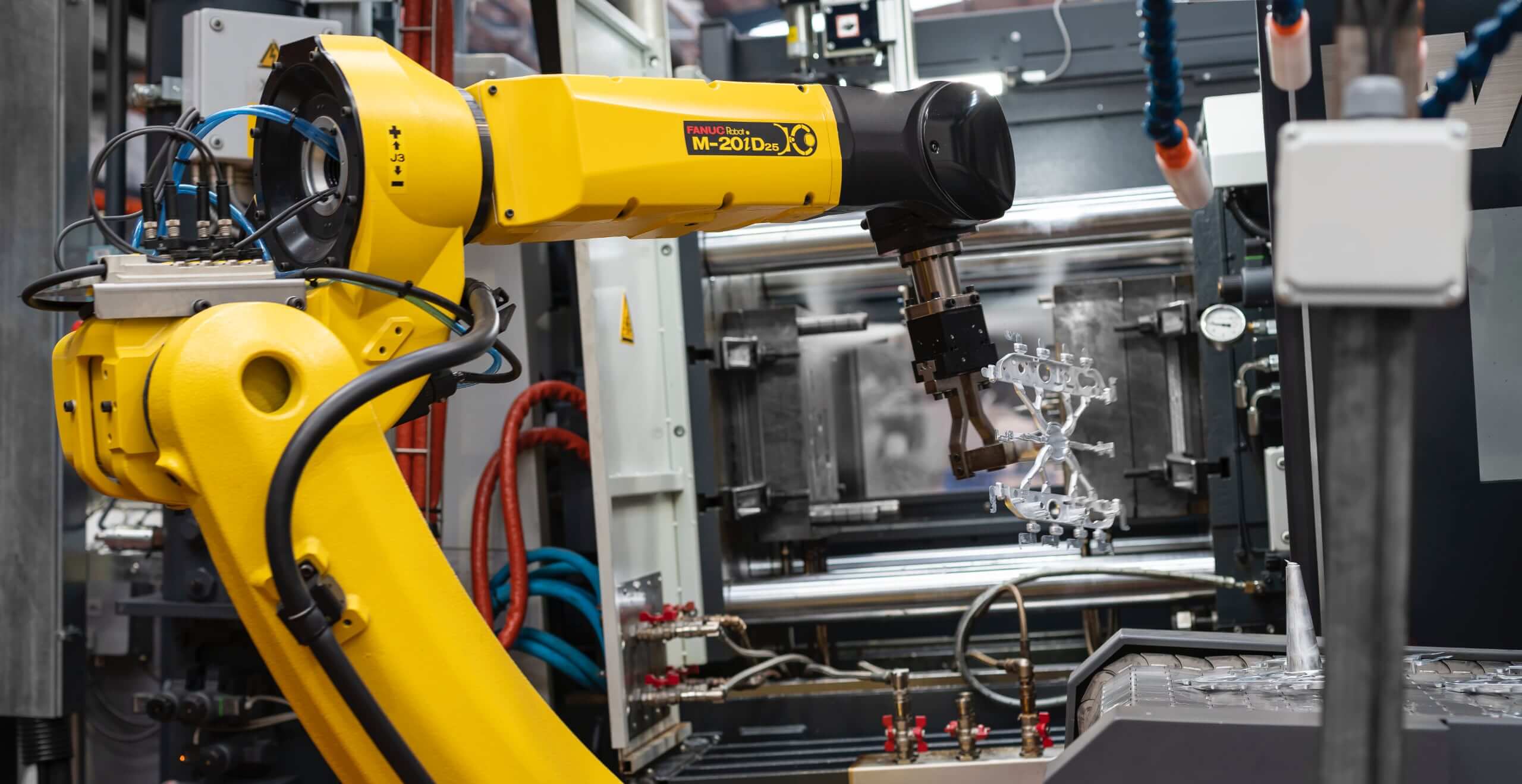
PRIMARY PROCESSES
High-pressure Zamak injection casting
At STAC we are specialists in the manufacture of injection-cast Zamak parts, accompanying our customers throughout the manufacturing process from design conception to the series manufacture of Zamak parts.
What is Zamak injection?
Zamak is an alloy of zinc, aluminium, magnesium and copper.
Its name comes from the first letters of the metals that compose it: Zn (zinc), Al (aluminium), MA (magnesium) and K (copper in German, “Kupfer”).
It is mainly used in the manufacture of metal parts by high-pressure die casting.
Some of the outstanding characteristics of the parts manufactured by the high pressure Zamak injection casting are:
- Durability: Zamak is resistant and durable, making it a suitable material for applications requiring high wear resistance.
- Malleability: It is easy to mould and shape, allowing the production of parts with complex designs and precise details.
- Surface finish: Zamak offers high quality surface finishes, such as lacquered, chrome plated, nickel plated, PVD, etc.
- Low melting temperature: Unlike many other metals, Zamak has a low melting temperature, making it easy to process and cast.
Do you want to know how?
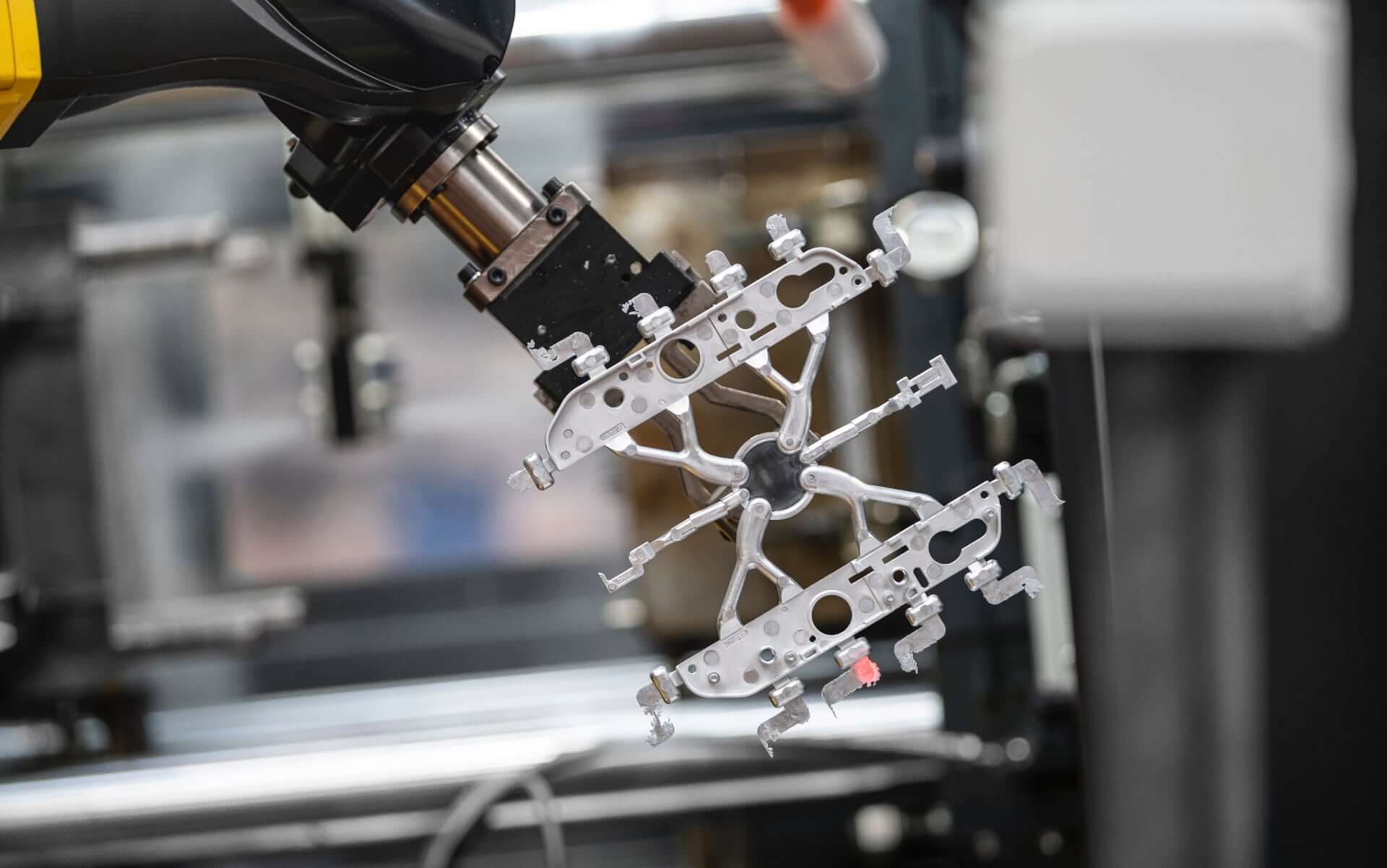
Stages of Zamak injection casting
This manufacturing process has many stages common to all plastic or aluminium injection processes. These are the main stages:
- Design of the part: At this point we talk about the design of the piece, but oriented to the injection process. There are many factors to consider which are very different from other processes. We can advise you.
- Design and manufacture of the mould: Materials, injection zone to the part, refrigeration in the mould, moulding of undercut zones, etc. A good mould means quality and repeatability in production.
- Preparation of injection machine: The mould or die is placed in a Zamak injection machine. The machine has a casting chamber where the Zamak material will be placed.
- Smelting of Zamak: Zamak starts in the form of ingots. It is then heated to a suitable temperature until it melts and becomes a liquid.
- Zamak injection: Once the Zamak is melted, it is injected into the mould using a plunger and a nozzle. The material must quickly fill all the cavities. Here having automatic machines with process control is crucial.
- Cooling and solidification: After injection, the Zamak is cooled inside the mould. The cooling speed can be controlled to ensure that the material solidifies properly and takes the shape of the mould.
- Opening the mould and removing the part: Once the Zamak has cooled and solidified, the mould is opened and the final part is ejected. At this point, the part may require some additional processes, such as deburring, machining or surface finishing.
- Zamak recycling: Waste and excess Zamak are collected and reused.
- The Zamak injection process offers advantages such as high precision in detail, fast and efficient production, as well as the possibility of creating complex parts with excellent surface quality.
At STAC we are experts in this process. And we will accompany you from the first moment to make your project a success.
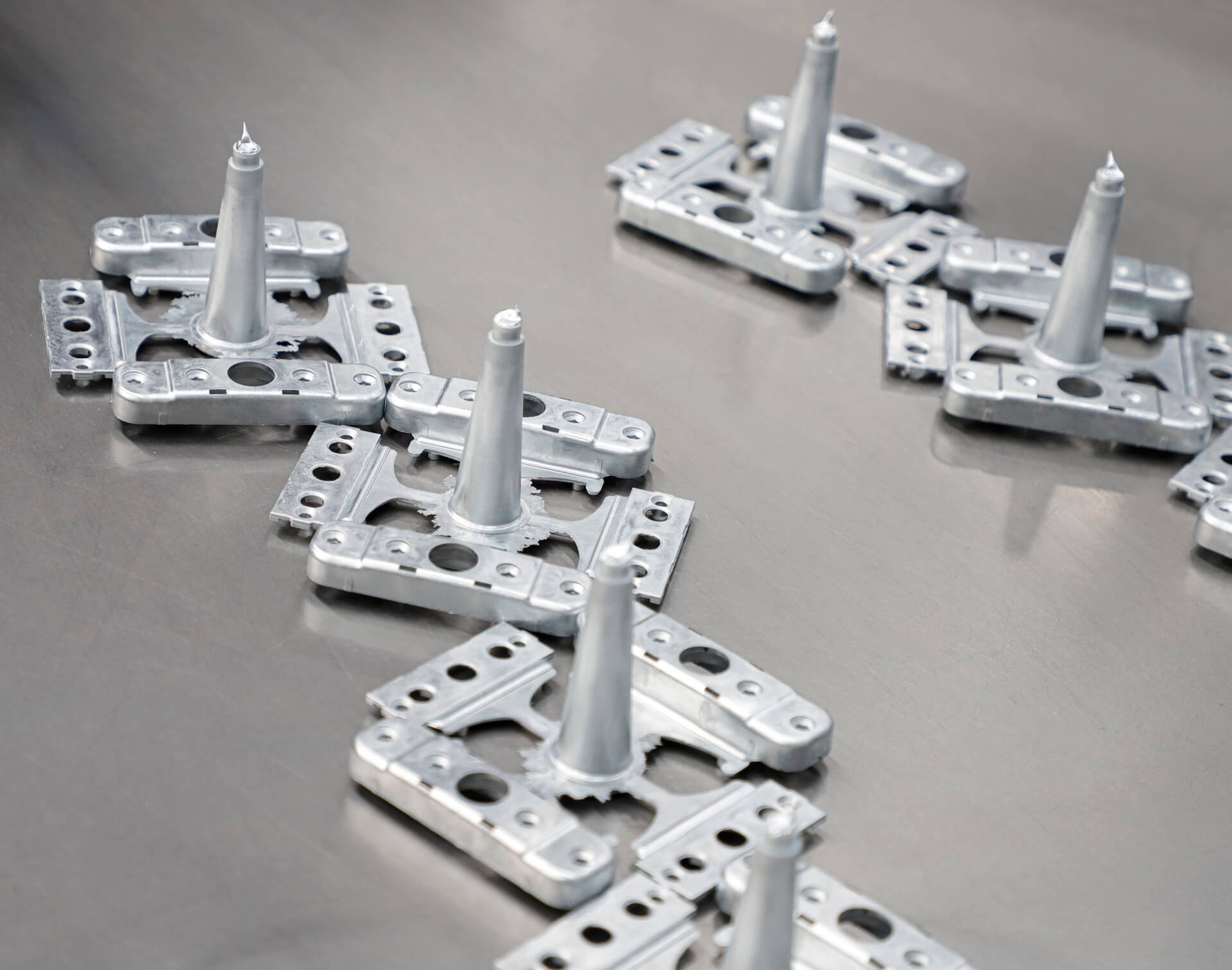
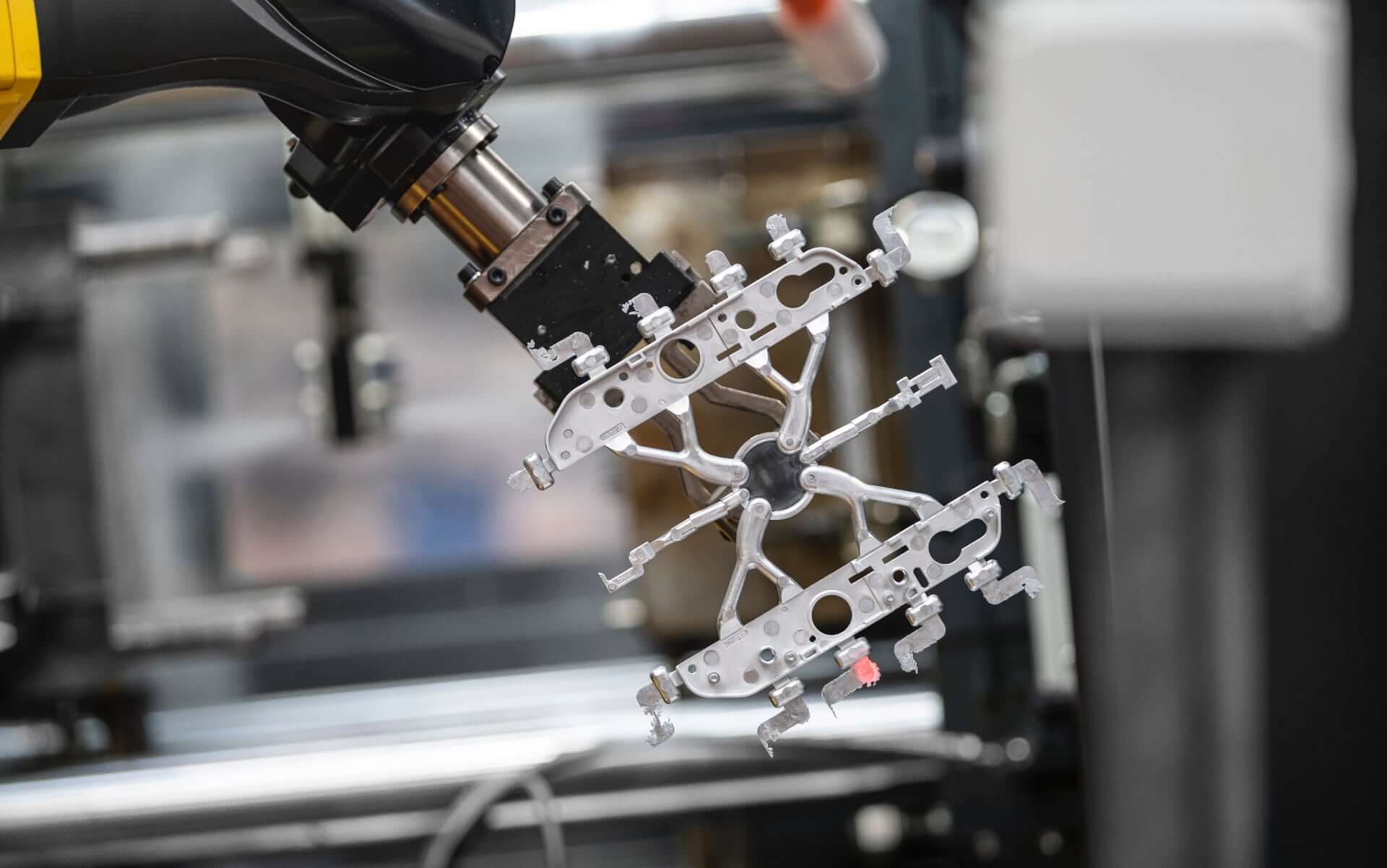
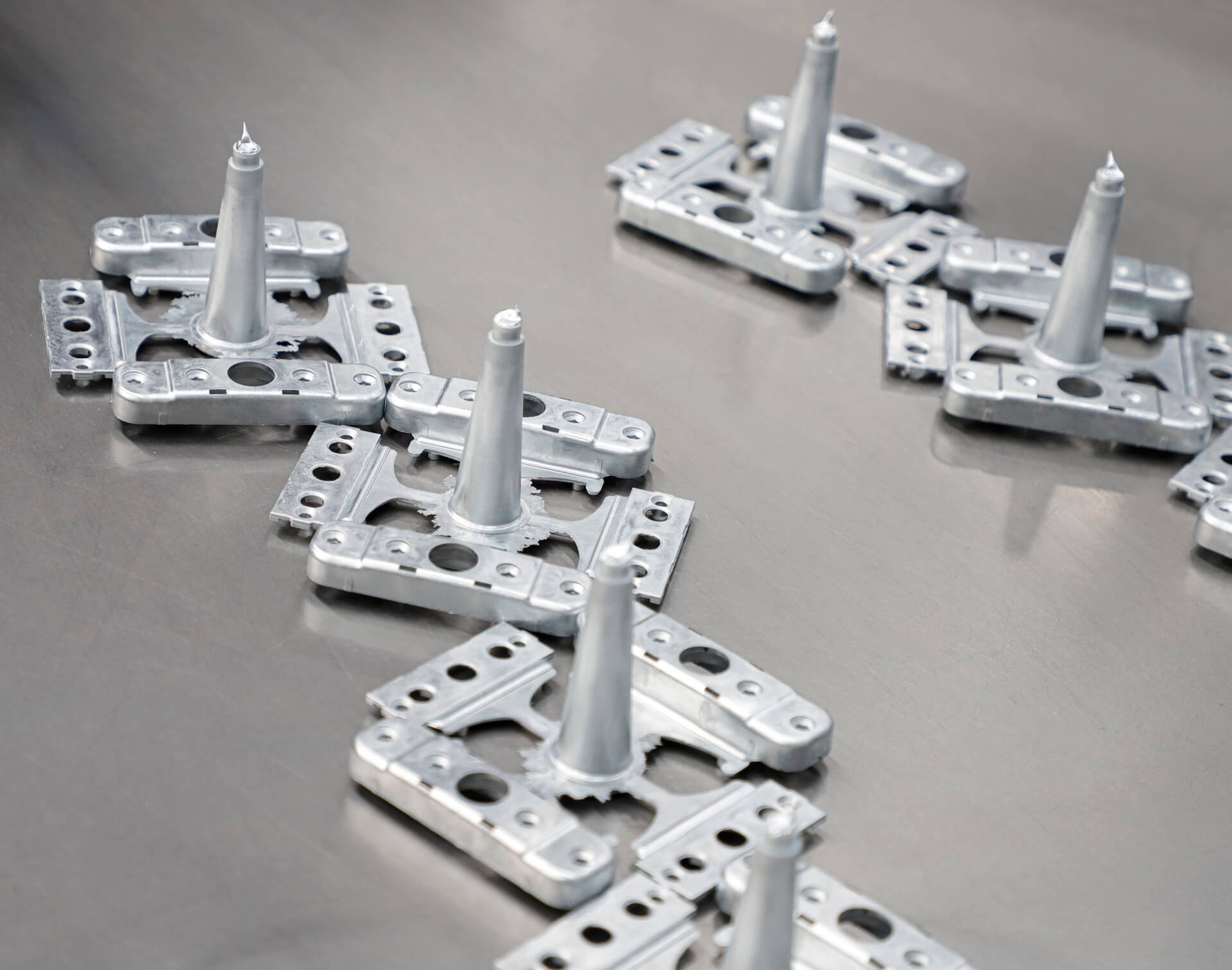
Frequently asked questions about Zamak injection
Zamak 5 is without a doubt the most widely used in the industry.
There are other alloys that improve on Zamak 5 in very specific characteristics, such as fluidity.
For example: Zamak 5 and Zamak 12.
Zamak 5
- Good corrosion resistance.
- Greater mechanical resistance.
- Industrial applications and structural components: Commonly used in industrial applications, such as machinery components and structural parts that require greater strength and durability.
Zamak 12
- Increased fluidity and filling capacity: Zamak 12 has excellent fluidity due to its higher magnesium content. This makes it easier to fill the mould cavities and reproduce complex details on the part.
- High precision and thin parts: Due to its ability to flow easily into the mould, Zamak 12 is ideal for manufacturing parts with thin walls or intricate details. If your part requires tight tolerances or delicate design features, Zamak 12 can provide greater precision and surface finish.
- Electrical and electronic applications: Used in the manufacture of electrical and electronic components, such as connectors, plugs and parts of electronic devices, due to its fluidity and ability to reproduce fine details.
If you want to know more about materials, contact us.
Molten Zamak enters the injection mould at a temperature of 420ºC. Therefore, the moulds have to be manufactured with steels for high-temperature work.
At STAC we have a tooling manufacturing department that is responsible for the design and manufacture of the moulds and their maintenance throughout their service life.
Some of the most important features to consider are:
- Materials for the different parts of the mould: These materials must be sufficiently strong and durable to withstand the high pressures and temperatures of the injection process.
- Moulding plates: The mould consists of a cavity and a core that define the shape of the part to be injected. These parts must be precise and have a high quality surface finish to ensure reproducibility and quality of the parts.
- Cooling system: The Zamak injection mould must have an efficient cooling system to control the mould temperature during the process. This helps ensure proper solidification of the Zamak and an efficient production cycle.
- Feed channels and overflows: The mould must have feed channels to allow the entry of the melted Zamak into the mould cavity. In addition, overflow areas are required at the perimeter of the mould to assist in the evacuation of air and impurities during the injection process.
- Wear resistance: Given that molten Zamak can exert significant pressures and forces on the mould, it is essential that the mould has adequate wear resistance and that interchangeable inserts are considered for the weaker parts of the tooling. This ensures long mould life and consistent part quality.
Stainless steel moulds are perhaps the most technical tooling that we manufacture and the ones with the most critical maintenance.
STAC guarantees its customers the mould during the life of the tooling.
If you want to know more about this point, we can help you. Contact us.
To manufacture injected Zamak parts with the highest quality, our machines have the following characteristics:
- High pressure and closing force: the machine must be able to generate and maintain high injection pressure to ensure proper filling and compacting of Zamak in the mould. In addition, it must have enough closing force to keep the mould safely sealed during the process.
- Precise temperature control: the machine must have a precise temperature control system to ensure that the cast Zamak maintains the right temperature throughout the injection process, from smelting to injection time. This helps to avoid problems such as premature cooling or thermal imbalances that may affect the quality of the part.
- High precision injection and dosing system: the injection and dosing system must allows precise control of the volume and injection rate of the melted Zamak into the mould. This ensures a uniform distribution of the material and avoids problems such as porosity or filling defects.
- Injection pressure and speed control: the machine must have sophisticated controls that allow precise adjustment and control of injection pressure and speed. This is essential to adapt to the specific characteristics of Zamak and part design, thus ensuring optimal injection and minimizing defects.
- Monitoring and logging capability: It is important that the machine has monitoring and data logging capabilities to allow detailed tracking of process parameters such as temperature, pressure, speed, times, among others. This facilitates the identification of potential problems and contributes to the continuous improvement of the manufacturing process.
- Gas extraction system: As Zamak injection can generate gases and bubbles during mould filling, the machine must have an efficient gas extraction system. This helps to minimize porosity and improve the quality of parts.
- Robustness and stability: The machine must be robust and stable to withstand the high pressures and temperatures of the Zamak injection process. This includes a solid structure, high-strength components and reliable clamping and closing systems.
Safety: Our machines are fully robotised so that no worker comes into contact with moving parts during production. The correct PPE is also used for each process.
If you want to know more about our Zamak injection capabilities, please contact us.
Comprehensive manufacturing solution
Our goal is to offer you comprehensive and high quality solutions for your manufacturing needs. Let us explain how we handle each stage of the process
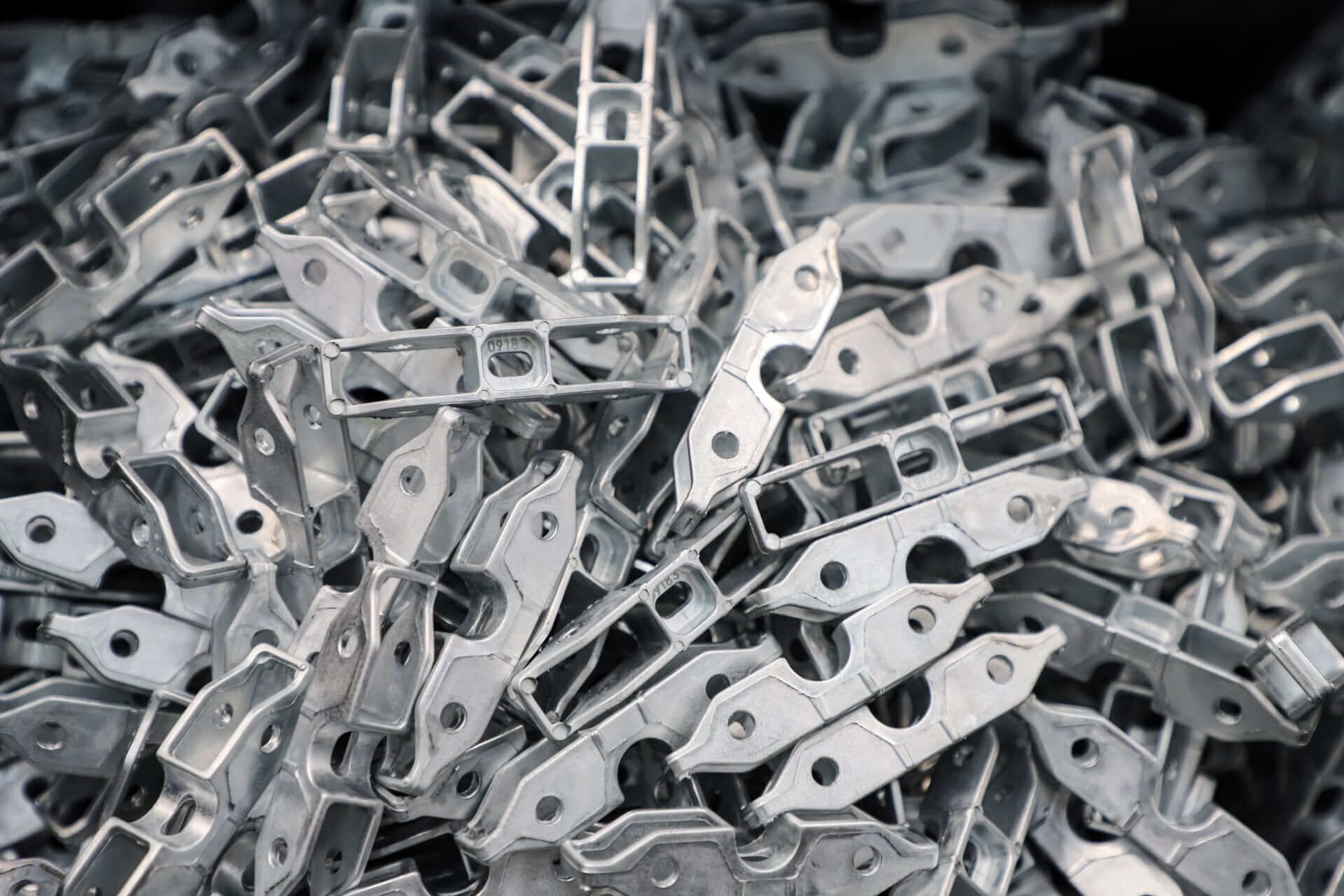
At STAC, we want to be your comprehensive supplier of injected Zamak parts.
We want to provide you with a comprehensive service and we take care of the entire process, from the initial design to the final delivery of the finished product where you request it.
Our priority is to help the customer achieve their goals
At STAC, we are committed to excellence and customer satisfaction.
We are ready to work closely with you and meet your specific requirements.
Don’t hesitate to contact us to discuss your projects and how we can help you achieve your goals.
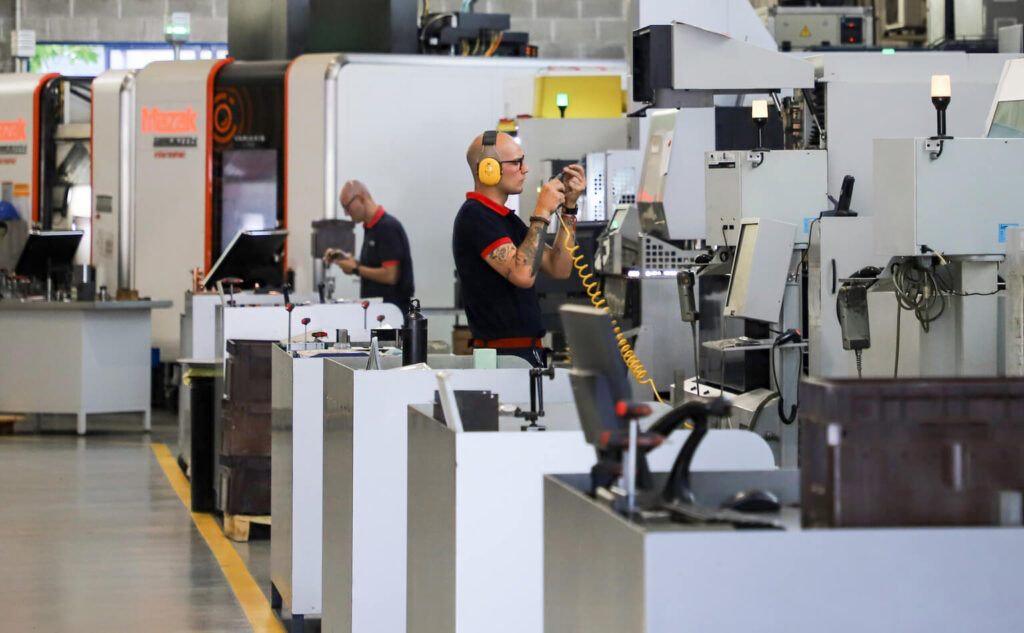
Post- Zamak Injection processes
After the Zamak injection process, it is common to perform a series of subsequent processes to obtain the final parts with the desired characteristics.
The most common post-casting manufacturing processes are the following:
Mechanical surface treatments
Such as shot blasting, which consists of removing burrs, sharp edges or unwanted protrusions of the moulded part, by projecting an abrasive on to the piece at high speed, or vibration polishing which is a system of cleaning and polishing the part with the help of abrasives in wet medium.
Decorative or protective treatments
For example, electrolytic zinc plating which can increase the corrosion resistance of Zamak parts. STAC has various technologies and different finishes. Or powder coating which is a finishing and coating process for the parts that are on view. They can improve both the aesthetics and the corrosion resistance of the pieces.
Contact us
We’ll be happy to provide help for your projects and resolve any doubts as soon as possible