Technical plastics
Technical plastics are characterized by a wide range of properties ranging from mechanical strength, dimensional stability, temperature resistance, electrical and thermal properties, as well as their ability to resist wear, corrosion and various chemicals.
At STAC we evaluate the most suitable material depending on the production process and the final use of the products for each project. Ask us!
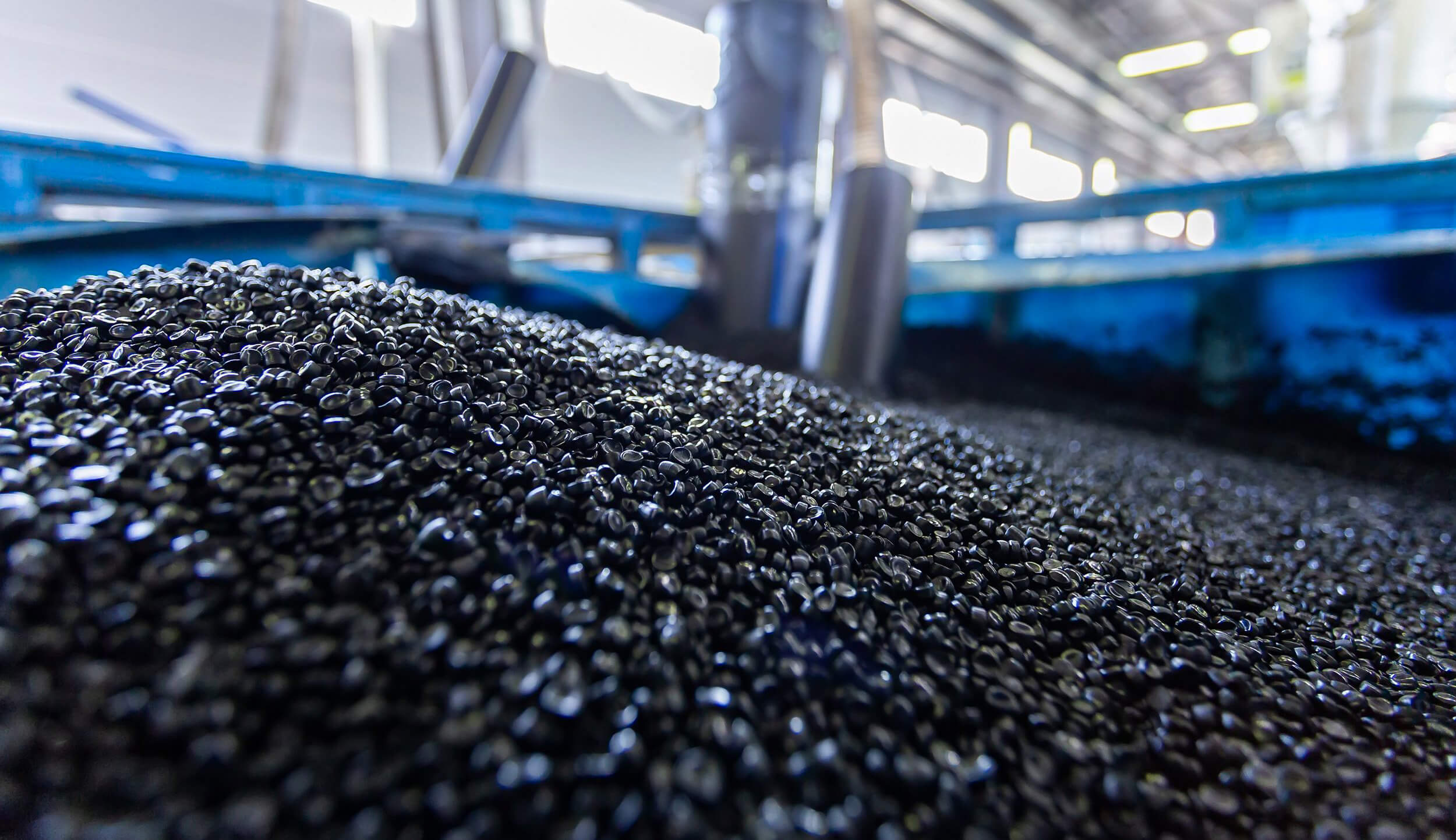
Technical plastics
Technical plastics are characterized by a wide range of properties ranging from mechanical strength, dimensional stability, temperature resistance, electrical and thermal properties, as well as their ability to resist wear, corrosion and various chemicals.
At STAC we evaluate the most suitable material depending on the production process and the final use of the products for each project. Ask us!Plastiques techniques
ABS | Acrylonitrile butadiene styrene
ABS is an amorphous rigid thermoplastic. It is a material with a low thermal conductivity coefficient, which makes it a very interesting alternative for thermal bridge breakage components or profiles. Most grades of ABS are limited for use at temperatures above 87ºC, where it begins to lose mechanical strength. That is why it cannot be lacquered.
ABS plastic has excellent impact resistance, low temperature resistance, chemical resistance and good dimensional stability. Despite this, it is very sensitive to sunlight, so the use of light coloured pieces for exteriors is not recommended.
- Low thermal conductivity coefficient.
- Good impact resistance.
- Dimensional stability due to its low water absorption.
- Stiffness, hardness and toughness even at low temperatures.
- Material that can be manufactured co-extruded with flexible TPE.
- Low resistance to UV radiation.
- All types of pieces. Almost any geometry can be produced, although it is not recommended for high-temperature applications or for prolonged exposure to sunlight.
- Thermal break profiles that are not to be lacquered.
- Extruded profiles for crossing leaves in sliding doors.
- Extruded profiles for facades.
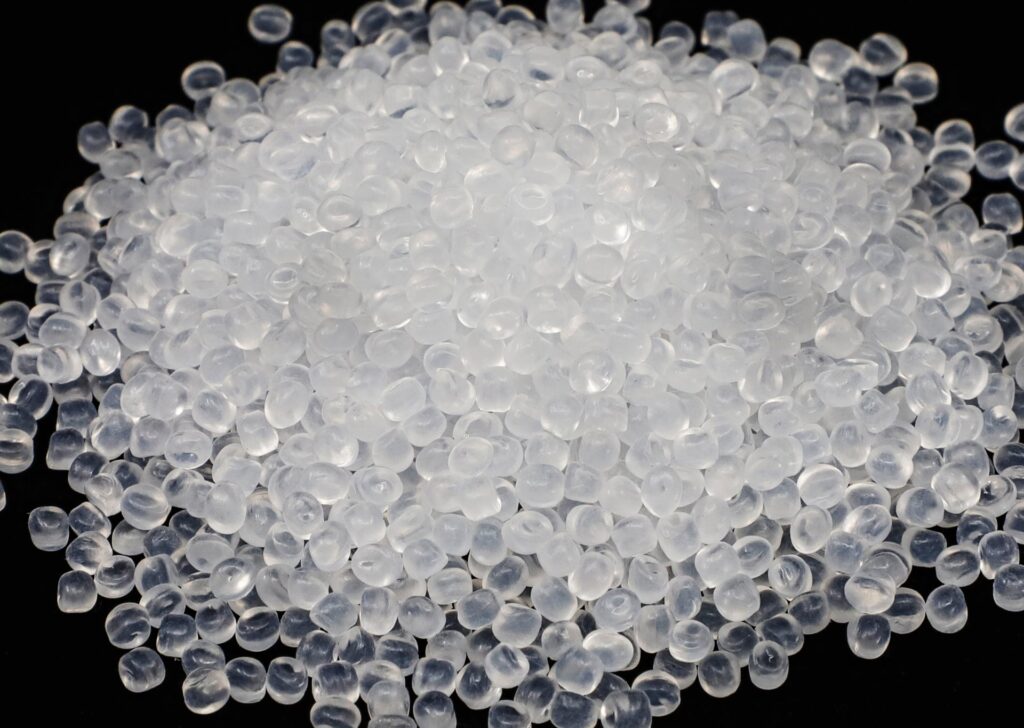
PA6 | Polyamide 6
Polyamide 6 is a semi-crystalline rigid thermoplastic. It has a melting temperature of around 218ºC, which gives it good temperature resistance. It has a low thermal conductivity coefficient, which makes it suitable for thermal insulation applications. It is a hygroscopic material, so it absorbs moisture from the environment. Polyamide 6 is one of the most economical engineering plastics and has good mechanical and UV resistance, making it a good choice for a wide field of outdoor applications.
- Low thermal conductivity coefficient.
- Thermal expansion coefficient close to that of aluminium.
- Good resistance to impact and friction.
- Resistant to UV radiation and outdoors.
- Resistant to corrosion and most chemicals.
- By absorbing moisture, its dimensions vary and its tensile strength is lowered.
- All kinds of parts can be produced using the injection process since almost any geometry can be manufactured. It is the material with which we have the most experience at STAC, in our facilities we manufacture products in PA6 for various sectors and customers.
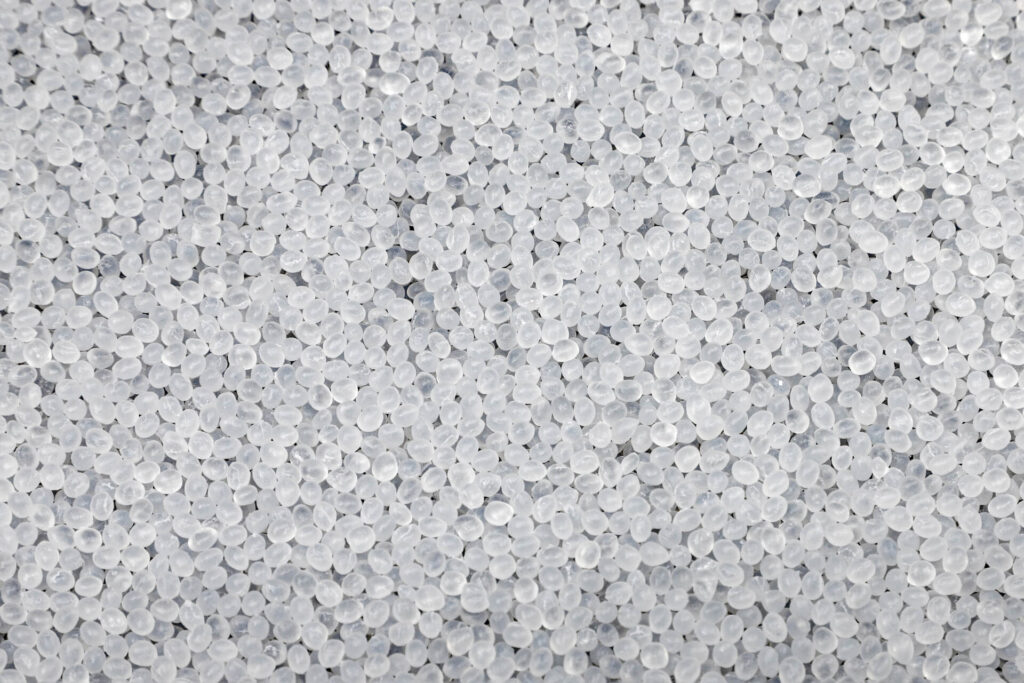
PA 66 | Polyamide 66
Polyamide 66 is a semi-crystalline rigid thermoplastic. It is one of the most used engineering plastics due to its balance between mechanical properties and price. It has greater temperature resistance than polyamide 6, since it melts around 265ºC. It also absorbs less humidity from the environment, which improves its dimensional stability.
For our extrusion process, we add 25% fibreglass. Thus we improve its mechanical properties, without increasing the thermal conductivity coefficient too much.
In addition, if we want to further improve the insulating capacity of polyamide, our range of HITEP profiles goes from a conductivity value of 0.3 W/mk for PA 66 with 25%GF to 0.19 W/mk. A reduction of more than 36% without changing the geometry of the profiles.
Read more- Low thermal conductivity coefficient.
- Thermal expansion coefficient close to that of aluminium.
- Melting point higher than the temperatures of the lacquering oven.
- Resistant to impact and aging.
- Resistant to UV radiation.
- Resistant to corrosion and most chemicals.
- Hygroscopic material.
- Almost any geometry can be manufactured. Together with PA6, it is one of the injection materials with which we work the most.
- Extrusion profiles for thermal bridge break for windows.
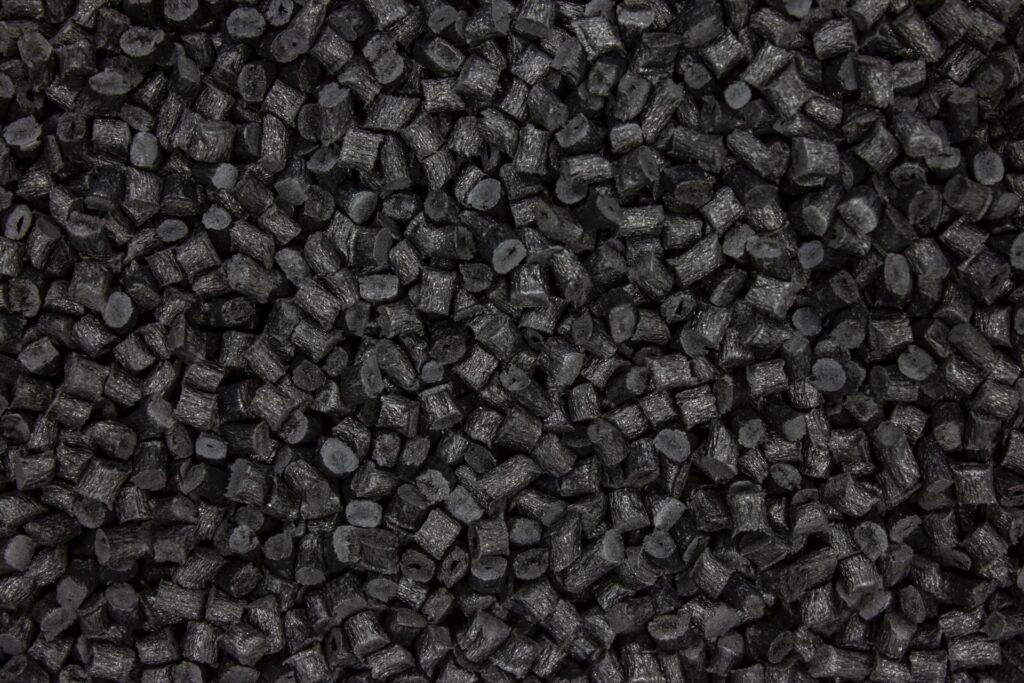
Rigid PVC | rigid polyvinyl chloride
Rigid PVC is an amorphous rigid thermoplastic that stands out for its high resistance to chemical agents and its excellent mechanical properties. It is an easily modifiable material, so you can produce grades with special properties: Greater impact resistance, custom colour, specific regulations… Because it can be manufactured in a wide range of colours and finishes, rigid PVC is an ideal material for mounting parts and / or profiles as aesthetic elements.
Thanks to its low friction coefficient, rigid PVC is ideal for extrusion joints where mounting is carried out by sliding into the channel. It is also widely used in co-extrusion with a flexible PVC in many wooden systems since it does not stain this type of surfaces.
Read more- High strength, rigidity and hardness.
- Minimal water absorption.
- Customized colours or according to RAL chart. Transparent and translucent grades available.
- Low coefficient of friction. Smooth and sliding finish.
- It has an elevated flame resistance, which can be enhanced by formulation.
- Resistant to UV rays and a large number of chemical agents.
- Material that can be manufactured co-extruded with flexible PVC.
- Temperature sensitive material, which can cause contractions and dilation if exposed to heat sources or, especially in dark colours, to direct sunlight.
- Parts that require a low friction surface finish, or that need to be welded together.
- Self-locking blind guide joints.
- Thermal bridge break profiles.
- Lid or placket seals.
- Thermo weldable seals for mosquito nets.
- Cover-channel profiles.
- Guide profiles in industrial doors.
- Profiles for facades.
- Seals that are inserted in to channel.
- Seals intended for wood systems.
- Seals intended for PVC systems.
- Seals that require high resistance to friction.
- U-seals to glaze bath screens or jacuzzi.
- Seals for interior furnishings such as kitchens, bathrooms, etc.
- Transparent or translucent seals.
- Seals for end of shutters.
- Beading for glazing hidden sheet systems.
- Profiles for sealing bathroom screens.
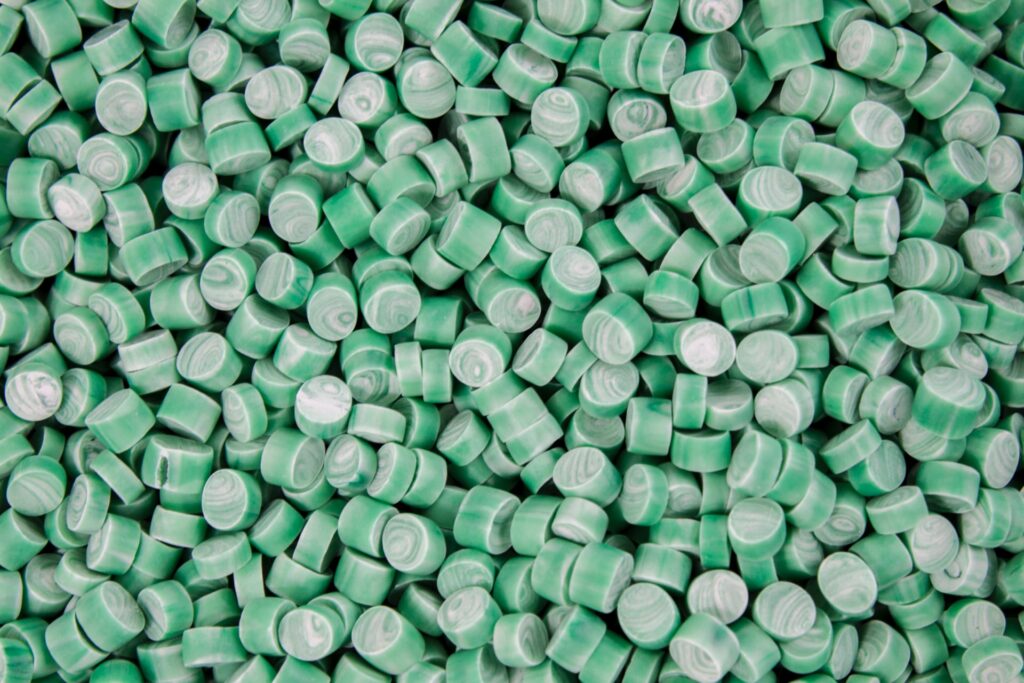
LDPE | Low density polyethylene
Low-density polyethylene is a semi-crystalline and semi-rigid thermoplastic, allowing it to be easily bent. Its has low density, so it is a light material. It is a particularly slippery material, with a very soft touch and a very low friction coefficient. This makes it ideal for use in products that require sliding in assembly or during use, such as in sliding doors and windows. It is also used to improve the clipping of some injection or extrusion rubbers that are inserted under pressure.
- High flexibility.
- High resilience.
- Minimal water absorption.
- High chemical resistance.
- Low friction coefficient.
- Colour according to RAL chart.
- Low resistance to UV rays.
- Reduced tensile strength.
- Parts that require flexibility and a surface finish of low friction or soft touch.
- Flexible waterproof parts that will be in contact with all kinds of fluids.
- Packaging seals for chemicals (excluding halogenated hydrocarbons).
- Cords for awnings.
- Joints between strips of shutters.
- Window seals that are inserted by machine.
- Frame seals for sliding door and window systems.
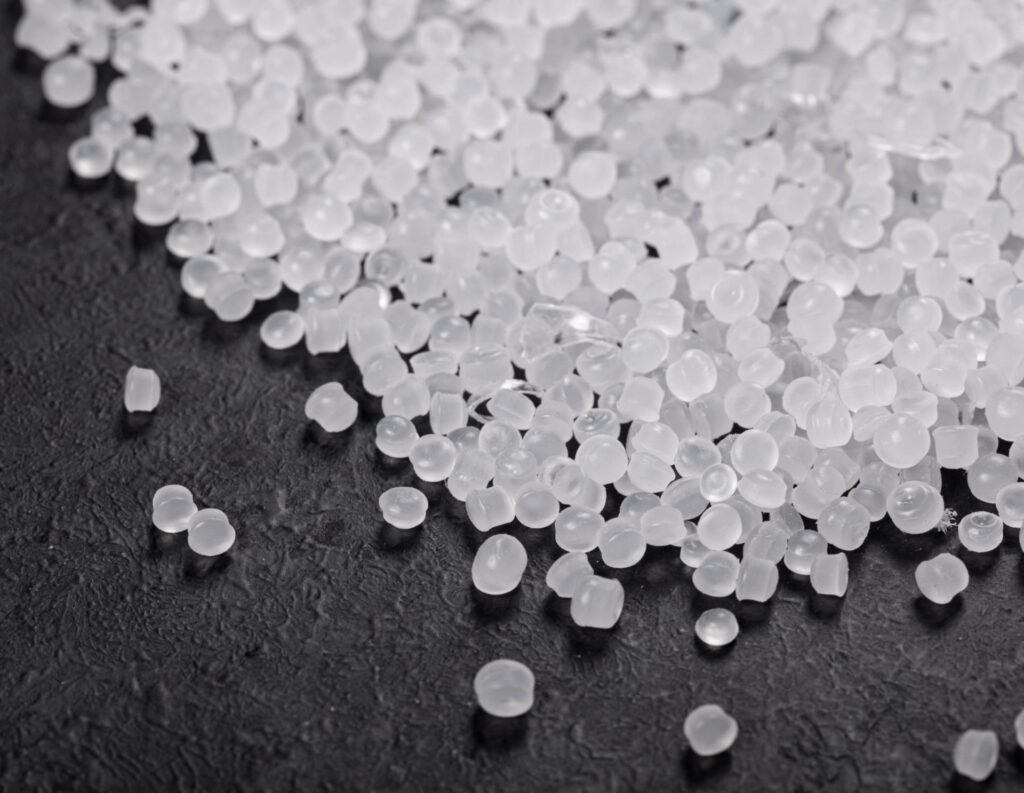
PP | Polypropylene
Polypropylene is a semi-rigid, semi-crystalline thermoplastic. It has low density and higher temperature and UV resistance than polyethylene. It is one of the most versatile plastics available and is used in a wide variety of industrial applications. In injection moulding, it is an economical material, although it has slightly inferior properties to other plastics. In extrusion, polypropylene is ideal for the manufacture of the bases of many rubbers that are inserted into a rigid base channel, as it is a material that produces very little friction and allows the product to be wound onto spools.
- High temperature resistance.
- Low friction coefficient.
- High chemical resistance.
- Colour according to RAL chart.
- Mechanical resistance lower than that of other plastics.
- All kinds of parts that require a compromise between cost and general properties.
- U-seams to cover panel edges.
- Seals that are inserted into the channel.
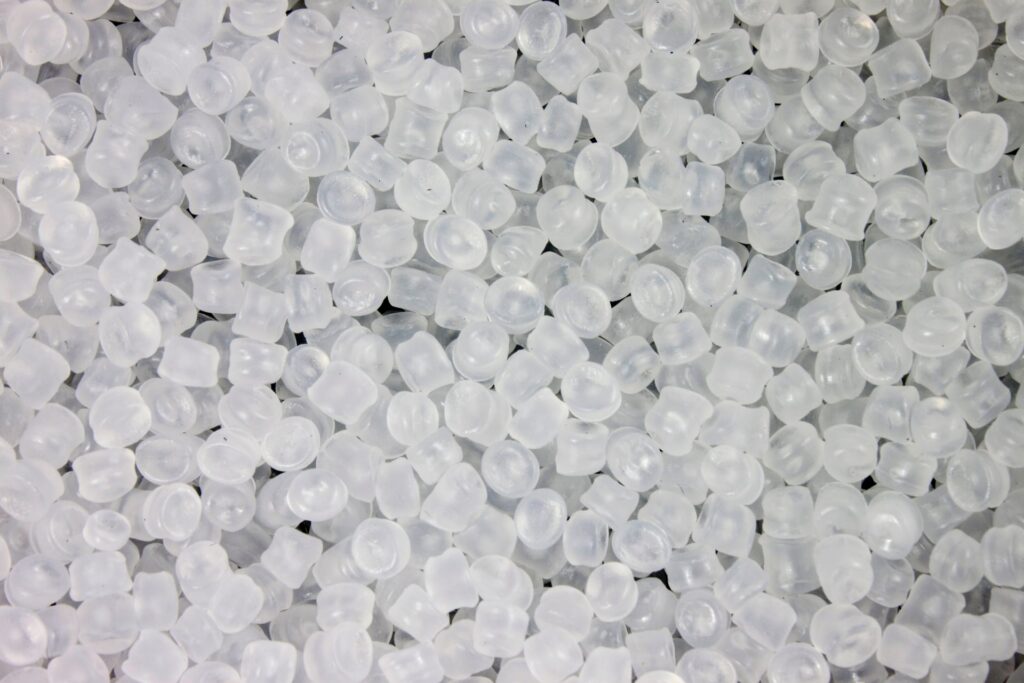
POM | Polyacetal
Polyacetal or polyoxymethylene (POM) is a rigid semi-crystalline thermoplastic, which stands out for its high rigidity, low friction and very good dimensional stability. This is due to its high degree of crystallinity. In addition, it has a high impact resistance and hardness. It has good chemical resistance except to strong acids. POM is used in injection parts that require good mechanical properties, low friction and wear resistance, without being exposed to sunlight. Its applications range from gear wheels, bearings, glasses frames, etc.
- High rigidity and dimensional stability.
- Low coefficient of friction and wear.
- High resistance to impact.
- Good chemical resistance.
- Resistant to fatigue.
- Little influence of temperature changes on its mechanical properties.
- Low resistance to UV rays.
- Parts that require a low friction surface finish or soft touch.
- Technical parts for mechanisms that need good wear resistance in their movements.
- Parts that require preserving their properties on exposure to environments with frequent and accentuated temperature changes.
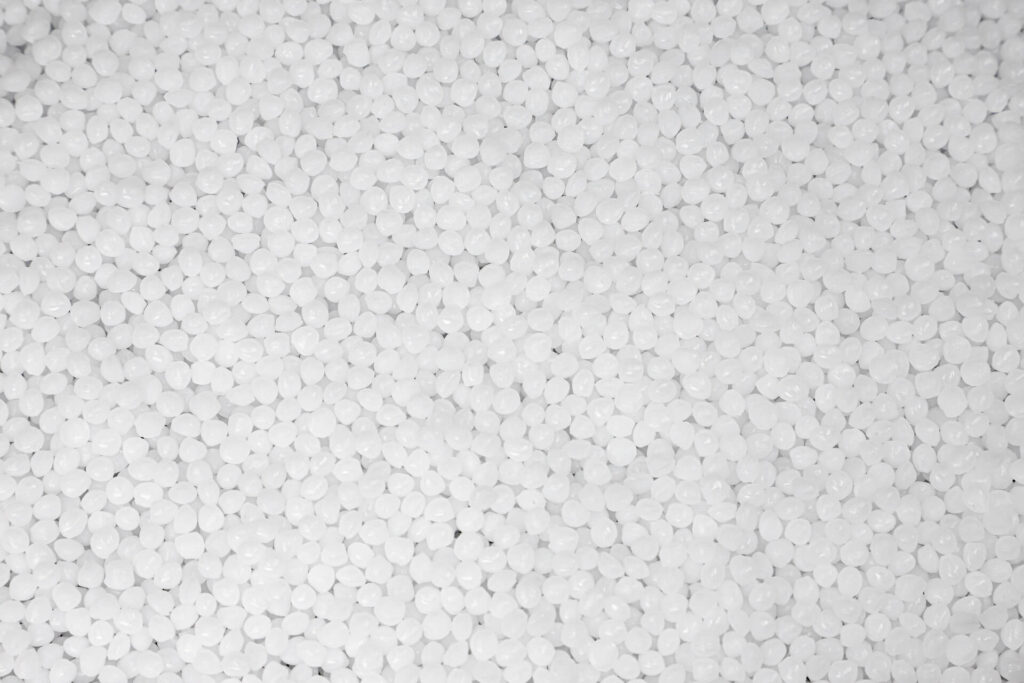
EPDM | Ethylene propylene diene rubber
EPDM is a thermostable elastomer characterized by its high resistance to abrasion, weather, ozone and UV rays. It has good chemical resistance against acids, bases and polar solvents. It is the most used material in the manufacture of joint seals and extruded profiles, due to its mechanical characteristics and its cost. The main application of EPDM is also to create accessory parts for seals and profiles, as well as for any external sealing application. This is due to its suitability in terms of insulation and impermeability, as well as its flexibility. Being a rubber, it is a material with a high surface adhesion and also has a great elasticity. EPDM can also be manufactured in closed-cell sponge or foam, thus reducing its density, increasing thermal insulation and providing door and window systems with a softer close.
- High resistance to chemicals, ozone and UV radiation.
- High flexibility at low temperatures.
- Excellent return from compression deformation.
- Acoustic damping.
- High friction coefficient, which causes it to adhere to surfaces and can stain parts of the system.
- Difficult to colour.
- It is applied to all types of sealing parts, due to its watertight properties and form recovery capabilities after the application of a force.
- Seals for steel doors.
- All kinds of dynamic seals such as frames, central…
- All kinds of static seals such as glass joints, wedges, U-shaped joints…
- Window seals.
- Industrial seals.
- Anti-trap seals.
- Seals for bodywork.
- Seals for facades.
- Seals for pipes.
- Expansion joints for civil works, bridges…
- railings and handrails joints.
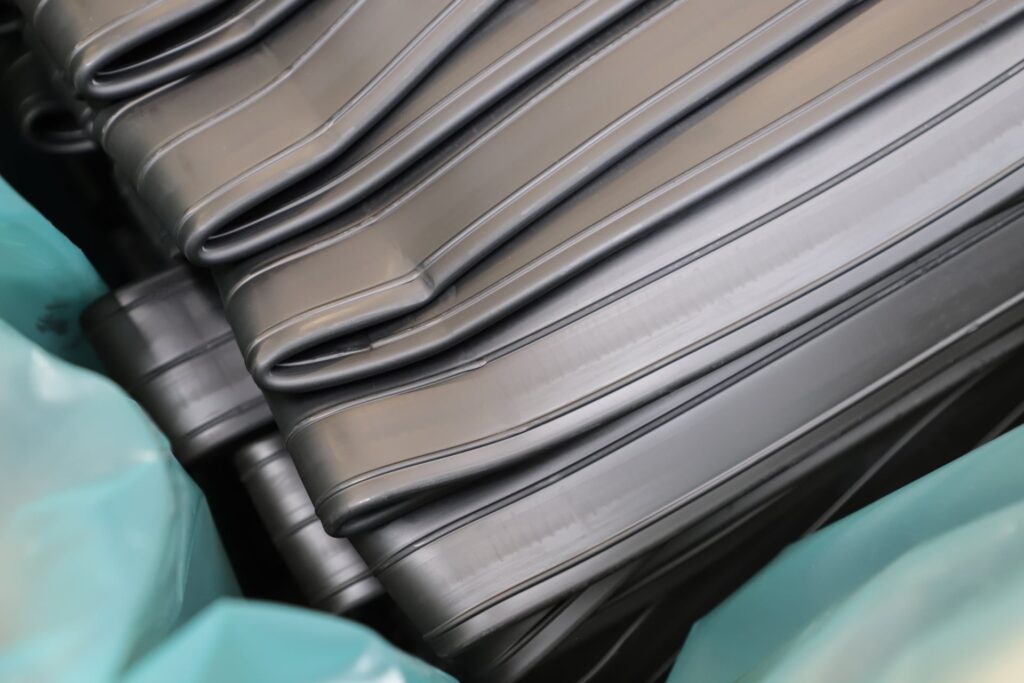
Flexible PVC | Flexible polyvinyl chloride
Flexible PVC is a thermoplastic elastomer For extrusion, combined with acrylic or NBR rubbers, it can offer excellent results as a dynamic seal. It is a material that has a particularly smooth surface with a very low friction coefficient. This makes it ideal for use in applications where the rubber needs to rub or drag. It is also very commonly co-extruded with rigid PVC for wood systems, since it does not stain this type of surfaces. The recommended temperature range of these materials goes from -20ºC to 60ºC continuously.
In injection, as with rigid PVC, it must be taken into account that its degradation products are corrosive and so stainless steel moulds and specific machines that can work with this material are required. Flexible parts are usually injected that require a low friction coefficient, which allows the parts to have smooth movements despite coming into contact with each other.
- Minimal water absorption.
- Customized colours or according to RAL chart. Transparent and translucent grades available.
- Low coefficient of friction. Smooth and sliding finish.
- It has an elevated flame resistance, which can be enhanced by formulation.
- Resistant to UV rays and a large number of chemical agents.
- Material that can be co-extruded with rigid PVC.
- The grades combined with rubbers have a good recovery from compression deformation, which makes them suitable for dynamic seals.
- Temperature sensitive material, which can cause permanent deformations if exposed to heat sources.
- Parts that require a low friction surface finish, or that need to be welded together. In the case of flexible PVC, the most frequent application is for windbreak systems in doors and windows.
- Flexible waterproof parts for doors and windows and barriers against water or gases.
- Seals for steel doors.
- Dynamic seals such as hinged or central.
- Static seals such as glazing seals, wedges, U-shaped
- Seals for blinds guides.
- Seals for bathroom screens or offices.
- Mosquito nets seals.
- Transparent or translucent seals.
- Seals that are inserted into the channel.
- Seals intended for wood systems.
- Seals intended for PVC systems.
- Seals that require high resistance to friction.
- Seals to glaze bath screens or jacuzzi.
- Seals for interior furnishings such as kitchens, bathrooms, etc.
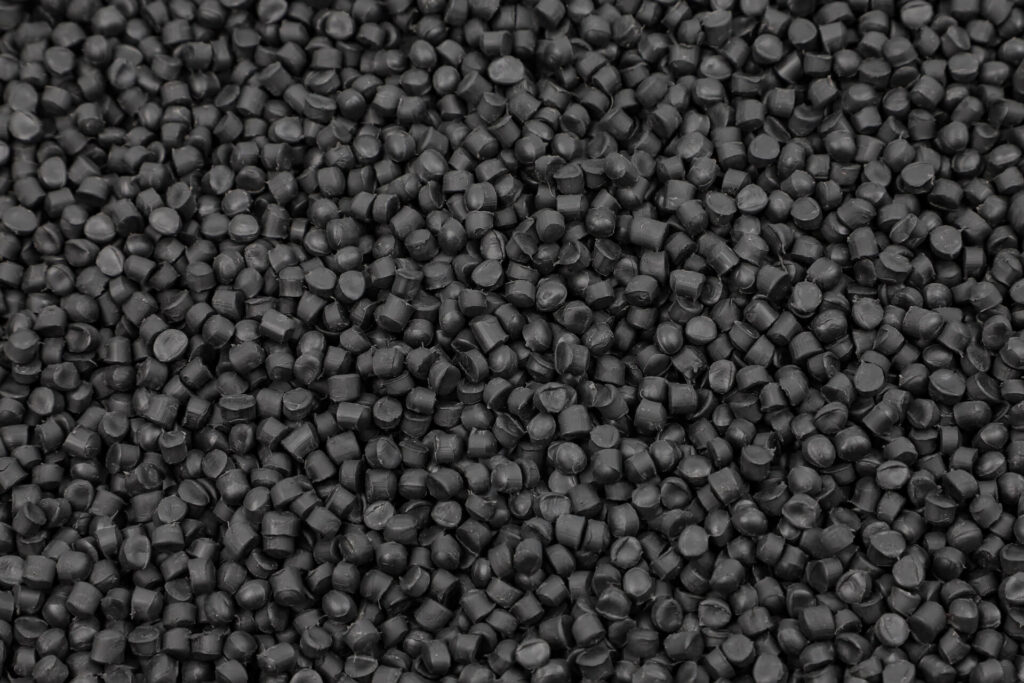
TPE SEBS | Thermoplastic styrene-based elastomer
SEBS (styrene-ethylene-butylene-styrene) is a thermoplastic elastomer with a behaviour very similar to rubbers. It is a material with very good properties for extruded seals that must behave dynamically. It provides excellent resistance to polar solvents, ozone and UV rays. In co-extrusion it is usually combined with polypropylene and polyethylene.
- High chemical resistance.
- High resistance to wear.
- Good resilience to compression.
- Good thermal resistance.
- Colour according to RAL chart.
- Less return from compression than rubber seals.
- Higher surface adhesion than flexible PVC.
- Gaskets or elastic components for all types of machines and systems.
- Seals for steel doors.
- Dynamic seals such as hinged or central.
- Static seals such as glazing joints, wedges, U-shaped…
- Joints for shutter guides.
- seals for refrigerators.
- Any seam you want to replace with rubber to use in colours or without the need for lubricant.
- Tilt&Turn window seams that are inserted by machine.
- End of shutter.
- Seams for sliding doors and windows, co-extruded or tri-extruded with polyethylene.
- Seams for wooden systems with dark tones.
- Window guides that are inserted into the channel.
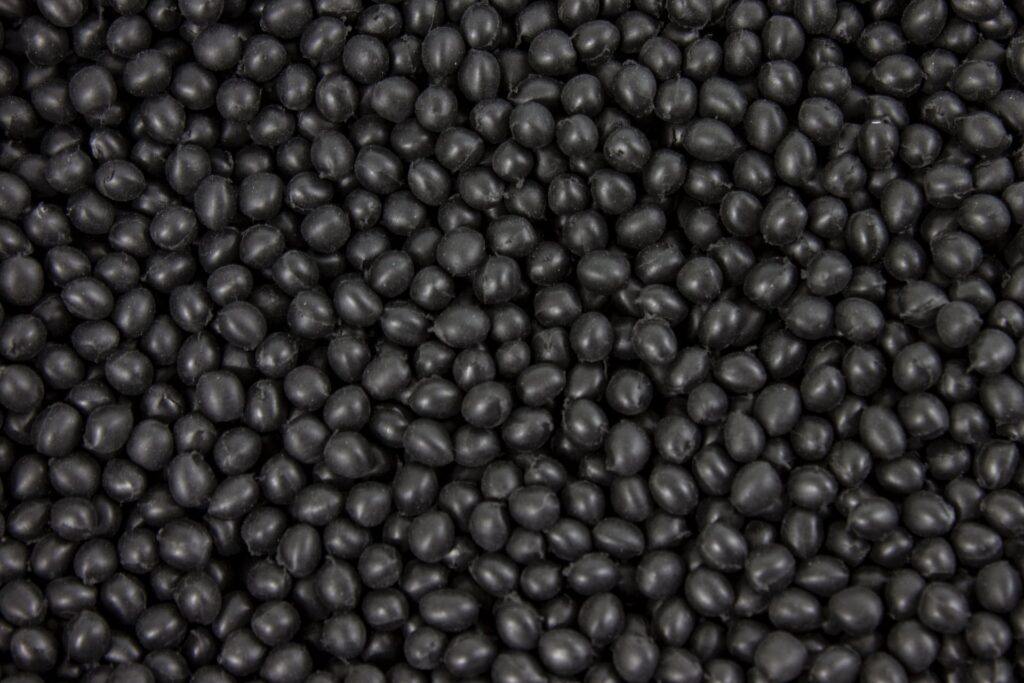
Other plastics
Acrylonitrile styrene acrylate is an amorphous rigid thermoplastic, a variant of acrylonitrile butadiene styrene (ABS), but it achieves better properties (up to 10 times more) in terms of weather resistance. This is due to the absence of double bonds, which enhances its mechanical strength as well as UV resistance. In addition, it has higher long-term heat resistance and better chemical resistance.
Furthermore, it retains the main characteristics of ABS, is resistant and rigid, has a low thermal conductivity coefficient, and cannot be lacquered. Its applications also include thermal bridge breaks, as well as for all the main industrial areas: automotive, machinery, electronics, construction, etc.
Its resistance to cracking due to environmental stress places it as one of the main options for outdoor solutions (cars, facades, naval sector, outdoor furniture, etc.).
ASA characteristics:
- Low thermal conductivity coefficient.
- Good impact resistance.
- Good resistance to UV radiation.
- Resistant to corrosion and most chemicals.
- Dimensional stability due to its low water absorption.
- Stiffness, hardness and toughness even at low temperatures.
- High resistance to abrasion.
- High resistance to cracking due to environmental stress.
ASA applications:
- All kinds of parts through the injection process. Almost any geometry can be manufactured; ABS replacement is recommended for applications with high temperatures or high sunlight exposure.
- Injected thermal bridge break components that are not to be lacquered.
High density polyethylene is a thermoplastic whose main quality is its high strength-density ratio. It is structurally composed of ethylene monomers, the same as low density polyethylene (LDPE), but with less branching, which strengthens the intermolecular forces and consequently the tensile strength of the material. Its density, 0.94 g/cm3, is not much higher than that of LDPE despite what their names may suggest, but it is the absence of branching that marks the differences.
HDPE has a very high specific strength, is hard, opaque, and can withstand temperatures up to 120ºC for short periods of time. It is resistant to many solvents, so it cannot be bonded by chemicals (chemical resistance), it can only be bonded by thermofusion welding.
Its low friction coefficient and shiny finish give it a very soft touch, for these reasons it is often found in water pipeline and drainage applications.
Characteristics of high density polyethylene:
- High strength, over a wide range of temperatures.
- Very high specific strength.
- Impermeable to gases and liquids.
- Minimal water absorption.
- High chemical resistance.
- Surface finish with low friction coefficient.
Applications of high density polyethylene:
- Parts that require a low friction surface finish or soft touch.
- Impermeable parts that will be in contact with all kinds of fluids.
- Packaging for chemicals as they do not deteriorate.
Neoprene is the trade name of chlorobutadiene or chloroprene synthetic rubber. It is a material with good chemical stability, with excellent resistance to degradation due to the sun (UV resistance), and is resistant to ozone and climate. The most common hardness of this material usually ranges between 60 ShA and 70 ShA. It has a density range around 1.48 g/cm3. It is a very elastic and flexible material that also has good flame resistance. Our extruded joints are certified as a level B-s2, d0, according to UNE-EN 13501:2007+A1:2010. One of the main attractions of chloroprene rubber is its ability to resist damage caused by bending and torsion.
Characteristics
- Excellent resistance to climate, ozone and UV radiation.
- Good chemical resistance.
- High resistance to bending and torsion.
- Very good thermal insulation.
- High return from deformation by traction and compression.
Single-component applications:
- Fire-fighting systems.
- All kinds of dynamic joints such as hinged, central.
- All kinds of static joints such as glazing joints, wedges, U-shaped for glazing.
- Joints for windows.
- Industrial joints.
Nitrile rubber is a copolymer of acrylonitrile and butadiene. It is a synthetic rubber characterized by its good resistance to oils and hydrocarbon-based chemicals. This makes it an ideal material for those seals that are going to be used in parts for machinery or engines. The most common hardness of this material usually ranges between 60 ShA and 70 ShA. It has a density range around 1.50 g/cm3. It is a material with mechanical characteristics of elastomers. Its ozone resistance is low, its conductivity is high, but it has good resistance to abrasion and heat.
Characteristics of nitrile rubber:
- Resistance to oils and hydrocarbons.
- Excellent resistance to high temperatures.
- Good adhesion to steel.
- They resist acids (except oxidizers).
- They resist alkalis and salts.
- Low permeability to air and natural gas, propane and butane.
- High conductivity.
Applications of nitrile rubber for injection:
- Sealing gaskets or components for all types of machines or systems.
Applications of nitrile rubber in single-component extrusion:
- Gaskets in motors.
- Automotive joints.
- Machinery joints.
- Joints in contact with greases and oils.
- Industrial joints
Silicone rubber is a synthetic elastomer characterized by its high resistance to temperature and UV rays. The most common hardness of this material is usually 70 ShA. It has a density range around 1.30 g/cm3. Silicone rubber is the most elastic and flexible rubber. It has excellent resistance to polar solvents, silicone putties, ozone, UV rays and wear. It is an easy rubber to colour, and can even be manufactured with translucent finish. Being a flame resistant material it is ideal for fire-fighting systems.
The temperature range for use of silicones ranges from -40ºC to 200ºC continuously.
Characteristics of silicone rubber:
- Resistant to extreme temperatures.
- Great resistance to compression deformation.
- High chemical resistance and good fire resistance.
- Resistant to weathering, ozone and humidity.
- Long service life.
- Colour according to RAL chart.
Applications of silicone rubber for injection:
- Gaskets or elastic components for all types of machines or systems.
Applications of mono-component silicone rubber:
- Gaskets for solar panels.
- Gaskets for fire-fighting systems.
- Industrial joints.
- Joints for steel doors.
- All kinds of dynamic joints such as hinged, central.
- All kinds of static joints such as glazing joints, wedges, U-shaped for glazing.
- Gaskets for ovens.
- LED diffusers.
It is a vulcanized thermoplastic. A mixture between a thermoplastic material and a rubber capable of internal vulcanizing. Its commonly used hardness is usually 60 ShA, but it is available across the entire range of the ShA hardness scale. It has a density range around 0.98 g/cm3. TPV has a smoother surface than TPE, which gives it excellent wear resistance and still retains very good properties for dynamic joint behaviour. In co-extrusion it is usually combined with polypropylene. In injection we frequently work with it in all types of hardness, since it has very good characteristics for the manufacture of parts that suffer constant deformations. Its temperature range can go from -50ºC to 110ºC, making this the ideal thermoplastic to use for extreme temperature applications.
TPV characteristics:
- Wide scale of hardness available.
- Resistance in a very wide fork of temperatures.
- Highly resistant to abrasion.
- Soft touch.
- Color according to RAL letter.
TPV applications for injection:
- All kinds of parts or elastic components: Cleats, squares, bumpers, etc.
Applications of Single-component TPV:
- Joints for steel doors.
- Dynamic joints as hinged, central.
- Static joints such as glazing joints, wedges, U-shaped for glazing.
- Joints for shutter guides.
- Gaskets for refrigerators.
- Joints for solar panels.
- Cover joints for decorative conduit.
TPV applications in co-extrusion/tri-extrusion:
- Window joints that are inserted by machine.
- End of shutters.
- Joints for sliding systems co-extruded or tri-extruded with polyethylene
- Joints for wood systems in dark tones.
- Window guides that are inserted in the channel.
It is a thermoplastic polymer, with a foamy texture, formed by the combination of ethylene and vinyl acetate monomers, in varying percentages depending on the grade. It is a very versatile material, with numerous industrial applications. In the doors and windows sector it is usually used for extrusion joints of very low hardness, transparent for indoor use, or films. It has low water absorption, is easy to handle (lightweight), easy to cut, and is recyclable.
Characteristics of EVA:
- Resistance to low temperatures.
- Resistance to water.
- Resistance to UV radiation.
- Ozone resistance.
- Glassy finish.
Applications of single-component EVA:
- Static joints such as glazing joints, wedges, U-shaped for glazing.
Applications of co-extrusion/tri-extrusion:
- Joints with peel-off strip.
Polycarbonate is a thermoplastic with high transparency (89% transmittance), which allows it be used in countless applications in the industry. It also stands out due to its high impact resistance, dimensional stability, V2 flammability without the use of additives, as well as excellent scratch resistance. In extrusion it is not the material that we work with the most, but due to its transparency properties, we have made profiles for LED diffusers, for example. In Injection we also manufacture components that take advantage of the properties of this material, but the majority of its applications take advantage of its transparency capacity. The density of polycarbonate is 1.2 g/cm3, it has minimal shrinkage (0.6-0.8%), and resists chemical attacks except for strong acids, bleaches or benzene.
Characteristics of polycarbonate:
- High transparency.
- High impact resistance.
- Dimensional stability.
- Scratch resistance.
- Good chemical resistance.
- Resistant to thermal deformation.
- Low resistance to UV rays.
Polycarbonate applications:
- Parts for any sector that require a transparent/translucent finish.
- Components that require high strength regardless of their fragility.
- Parts for the electronics and electro-technical sector.
The copolymer of butylene terephthalate and polyalkylene-ether glycol in a commercial industrial material, belongs to the family of polyester thermoplastic elastomers. It is a resin developed for the automotive industry, both for moulding and extrusion, in the search for better properties for those components that are exposed on the outside of the vehicle. Its density is 1.14-1.27 g/ cm3, and its melting temperature is between 150 and 225ºC. It can be coloured, and has good chemical resistance, except against strong acids and oxidizing agents.
Characteristics:
- Good resistance to environmental exposure.
- Ease of manufacture both by injection and extrusion compared to other plastics.
- Wide range of working temperatures.
- It can be coloured.
- Good chemical resistance.
Some of its applications are:
- Parts for any sector that require environmental stability when exposed (automotive, architecture, aeronautics, naval, etc..)
Noryl is an amorphous thermoplastic, a modified resin formed by amorphous mixtures of resins together with styrene. These resins are either polyphenylene oxides or polyphenylene ethers. It has high heat resistance, as well as some electrical insulation capacity, although electrostatic powder coating is possible. It has excellent dimensional stability, ease of manufacture and processing, as well as low density. On the other hand, it can be sensitive in the presence of many organic liquids to environmental stress cracking. Its chemical resistance does not withstand contact with substances such as gasoline, kerosene or similar compounds that can cause cracking.
Characteristics of Noryl:
- Possibility of electrostatic powder coating.
- Ease of manufacture both by injection and extrusion compared to other plastics.
- Risk of environmental cracking.
- Great dimensional stability.
- Good chemical resistance.
Some of the applications of Noryl are:
- Parts for any sector that need to be powder coated.
Polyketone is a material in the high performance thermoplastic polymers family. It offers excellent mechanical properties, as it has a very high resistance to impacts, abrasion, and wear. Its chemical resistance is also remarkable, as well as its high viscosity, and dimensional stability. Its field of application covers those scenarios in which high wear resistance is necessary, as well as high precision: Industrial environments in general, automotive, aerospace, naval industries etc.
Features: Polyketone:
- High impact resistance.
- High resistance to abrasion and wear.
- Great dimensional stability.
- Good chemical resistance.
Some of the applications of polyketone are:
- Parts for any sector that require high resistance to abrasion and wear, maintaining dimensional precision: Mechanisms, bearings, bushings, etc..
It is a semi-crystalline thermoplastic polymer that stands out for its insulating properties. In addition, it is very resistant to temperature, stable up to 150ºC, as well as resistant to solvents. It has high hardness and rigidity. Compared to polyethylene terephthalate (PET) it has lower strength and stiffness, but slightly higher impact resistance. It is flammable, although it can be treated with flame retardants, and degrades in the presence of UV rays, which does not make it suitable for exterior applications exposed to sunlight, despite resisting very well to the weathering. The real interest of this material lies in those cases in which its insulating characteristic is of vital importance: Electronics, electricity and components for equipment that work with electrical circuits.
Characteristics of PBT:
- It provides a high degree of thermal and electrical insulation.
- Good resistance to impact.
- Low resistance to UV rays if not protected.
- Good weather resistance.
Some of the applications of PBT are:
- Parts for electrical / electronic systems: Housings, switches, connectors in general, mouldings of car headlights, etc.
- Production of masterbach (colourants).
- Manufacture of bristles for brushes with filaments.
Polystyrene is a thermoplastic polymer that has various types. In injection, the one used is known as “crystal”, which has a transparent solid finish, which has a high hardness, but also a high fragility. The main attraction of polystyrene is its insulating character, along with its surface brightness and dimensional stability. Its density is 1.05 g/cm3, and it can work up to about 100ºC. It is sensitive to UV, and also suffers from fatigue breakage. Chemically resists fats, oils, saline solutions or alcohols, but does not withstand contact with benzene, gasoline or solvents.
Polystyrene characteristics:
- It offers a high degree of thermal and electrical insulation.
- High hardness but fragile.
- Low resistance to UV rays.
- It suffers from fatigue breakage.
- Limited chemical resistance.
Some of the applications of polystyrene are:
- Parts for electrical / electronic systems: housings, components, etc.
- For components of lighting systems due to its transparency: lamps, housings, covers, etc.
Methacrylate is a technical plastic obtained by polymerization of methyl methacrylate. Its properties make it share applications with polystyrene (PS) and polycarbonate (PC), since they are also transparent plastics with similar characteristics. Compared to those, methacrylate is more resistant to weather, more transparent and has greater resistance to scratching. Its density is 1.18 g/ cm3, it has remarkable dimensional stability, and its optical properties are among the best of transparent plastics (92%). It is dielectric, hard but fragile, and its chemical resistance is limited (it does not withstand acids, acetones, hydrocarbons, etc.). It has very good resistance to UV rays, but is susceptible to fatigue breakage.
Characteristics of methacrylate:
- The greatest transparency of plastics.
- Hard, but low impact resistance (fragile).
- Very good resistance to UV rays.
- Susceptible to fatigue breakage.
- Good weather resistance.
Some of the applications of methacrylate are:
- Parts for all kinds of uses and sectors that require high transparency, both for indoor and outdoor.
In addition to all these materials, we can also mix with them different types of additives and fillers to improve some of their properties, or simply give them a different appearance. Some of these additives have already been cited for their frequent combination with some of the materials on the list, but we can extend their application to the rest of the list by studying the case and manufacturing process.
The main additives available are:
- Fiberglass filler.
- Mineral filler.
- Thermally and electrically conductive additives.
- Metal fillers.
- Masterbach dyes.
- Wood fillers.
- Fire retardant additives.
Comparison of flexible materials
Parameter
Shore Hardness Range
Compression set
Tensile strength
Elongation at breakage
Continuous/punctual lower tª limit
Continuous/punctual upper tª limit
TPE (SEBS)
35A-50D.
GOOD
GOOD
EXCELLENT
-40 ºC/ -55 ºC
90º/ 110 ºC
TPV
35A- 40D
GOOD
SUFFICIENT
GOOD
-50 ºC/ -60 ºC
110 ºC / 130 ºC
PVC
35A-80D.
POOR
EXCELLENT
SUFFICIENT
-20 ºC/ -30 ºC
60 ºC/ 80 ºC
PVC + Elastomer
35 A – 50D
GOOD
EXCELLENT
SUFFICIENT
-25ºC/ -50 ºC
70 ºC/ 80 ºC
EPDM
35A-85A.
EXCELLENT
GOOD
SUFFICIENT
-35 ºC/-45 ºC
70 ºC/ 100 ºC
Silicone
70A-80A.
GOOD
EXCELLENT
SUFFICIENT
-30 ºC / -40 ºC
190 ºC/ 200 ºC
NBR
35A-85A.
EXCELLENT
EXCELLENT
SUFFICIENT
-20 ºC/-30 ºC
80 ºC/100 ºC
CR
70A-80A.
EXCELLENT
EXCELLENT
SUFFICIENT
-35 ºC/-50 ºC
80 ºC/100 ºC
Resistance of flexible materials*
Parameter
Acids
Bases
Poor polar solvents
Hydrocarbons
Silicone mastics
Ozone
UV rays
Friction
Flame
Colour
TPE (SEBS)
GOOD
GOOD
EXCELLENT
SUFFICIENT
POOR
EXCELLENT
EXCELLENT
GOOD
BURNS
RAL CHART
TPV
GOOD
GOOD
GOOD
POOR
POOR
GOOD
GOOD
EXCELLENT
BURNS
RAL CHART
PVC
GOOD
GOOD
GOOD
GOOD
SUFFICIENT
GOOD
GOOD
GOOD
SELF-EXTINGUISHING
RAL CHART
PVC + Elastomer
GOOD
GOOD
GOOD
GOOD
POOR
GOOD
GOOD
GOOD
SELF-EXTINGUISHING
RAL CHART
EPDM
EXCELLENT
EXCELLENT
EXCELLENT
POOR
POOR
EXCELLENT
EXCELLENT
EXCELLENT
BURNS
BLACK/GRAY
Silicone
SUFFICIENT
GOOD
EXCELLENT
POOR
EXCELLENT
EXCELLENT
SUFFICIENT
EXCELLENT
DOESN'T BURN
RAL CHART
NBR
SUFFICIENT
GOOD
POOR
EXCELLENT
POOR
GOOD
EXCELLENT
POOR
BURNS
BLACK/GRAY
CR
SUFFICIENT
GOOD
POOR
GOOD
POOR
GOOD
EXCELLENT
EXCELLENT
DOESN'T BURN
BLACK/GRAY
Comparison of rigid materials
Parameter
Density
Tensile strength
Elongation at breakage
Elastic modulus
Impact resistance
Melting point
Bending temperature under load, 1.8 MPa
Vicat 50ºC/h
Maximum temperature (continuous/peak)
Minimum temperature (continuous/peak)
POM
1.41
GOOD
SUFFICIENT
EXCELLENT
EXCELLENT
178
95
175
77/ 97
-7/ -43
PA 66
1.14
EXCELLENT
GOOD
EXCELLENT
GOOD
262
100/70*
244
90/ 170
-7/ -43
PA 6
1.13
EXCELLENT
GOOD
EXCELLENT
GOOD
221
80/60*
190
80/ 160
-7/ -43
ABS
1.05
GOOD
SUFFICIENT
GOOD
EXCELLENT
106
85
95
62/ 77
-7/ -43
PC
1.21
GOOD
GOOD
GOOD
GOOD
144
127
145
101/ 116
-7/ -43
HDPE
0.956
SUFFICIENT
EXCELLENT
SUFFICIENT
POOR
131
60
121
110/ 130
-13/ -63
LDPE
0.914
POOR
EXCELLENT
POOR
EXCELLENT
103
30
78
77/ 97
-13/ -63
PP
0.91
SUFFICIENT
GOOD
SUFFICIENT
GOOD
165
58
87
92/ 107
-7/ -43
PS
1.05
SUFFICIENT
POOR
EXCELLENT
SUFFICIENT
130
82
86
70/ 94
-7/ -43
PVC
1.44
SUFFICIENT
EXCELLENT
GOOD
GOOD
130
67
78
53/ 66
-7/ -43
Units
g/ml
MPa
%
MPa
kJ/m2
ºC
ºC
ºC
ºC
ºC
Resistance of rigid materials***
Parameter
Friction resistance
Strong acids
Weak acids
Strong bases
Weak bases
Oxidisers
Organic solvents
Hydrocarbons
Exterior (UV, ozone…)
POM
EXCELLENT
POOR
GOOD
EXCELLENT
EXCELLENT
POOR
GOOD
GOOD
EXCELLENT
PA 66
GOOD
POOR
GOOD
GOOD
EXCELLENT
POOR
EXCELLENT
GOOD
GOOD
PA 6
GOOD
POOR
GOOD
GOOD
EXCELLENT
POOR
EXCELLENT
GOOD
GOOD
ABS
POOR
SUFFICIENT
EXCELLENT
EXCELLENT
GOOD
POOR
POOR
POOR
POOR
PC
AVERAGE
EXCELLENT
EXCELLENT
POOR
GOOD
POOR
AVERAGE
POOR
GOOD
HDPE
AVERAGE**
GOOD
EXCELLENT
EXCELLENT
EXCELLENT
POOR
AVERAGE
POOR
POOR
LDPE
AVERAGE**
GOOD
EXCELLENT
EXCELLENT
EXCELLENT
POOR
AVERAGE
POOR
POOR
PP
AVERAGE**
EXCELLENT
EXCELLENT
EXCELLENT
EXCELLENT
POOR
EXCELLENT
POOR
POOR
PS
POOR
SUFFICIENT
EXCELLENT
GOOD
EXCELLENT
POOR
POOR
POOR
SUFFICIENT
PVC
AVERAGE
EXCELLENT
EXCELLENT
EXCELLENT
EXCELLENT
POOR
SUFFICIENT
POOR
EXCELLENT
*** The resistances are indicative. Always consult specific cases providing temperature, concentration and exposure time.
Contact us
We’ll be happy to provide help for your projects and resolve any doubts as soon as possible