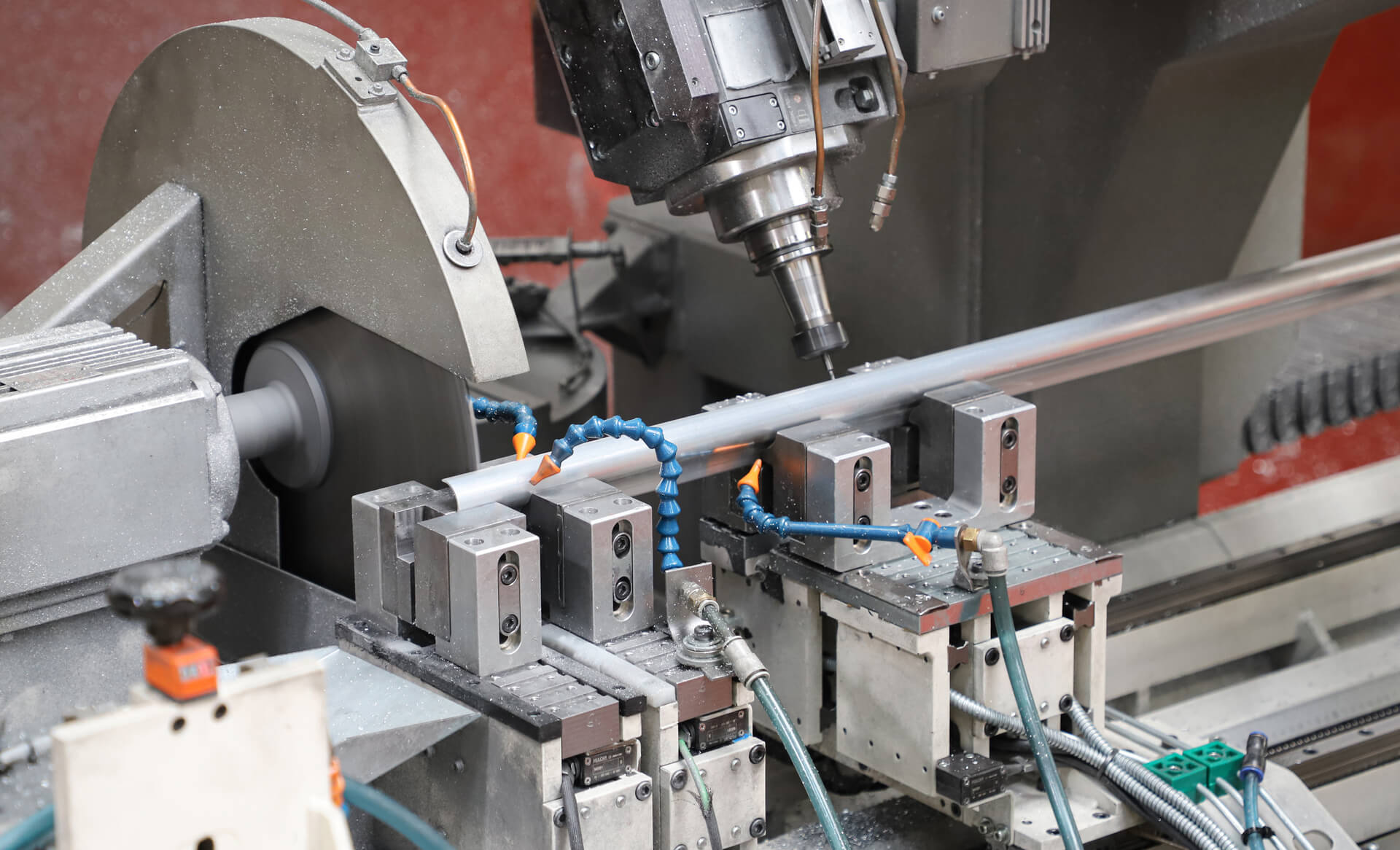
PRIMARY PROCESSES
Machining of aluminium profile
At STAC we are specialists in the manufacture of parts by the machining of aluminium profiles and we accompany our customers from conception through to the mass production of the desired part.
What is Aluminium Profile Machining?
Aluminium profile machining is an industrial manufacturing process which starts with extruded aluminium bars (profiles) to produce parts with specific shapes and sizes.
The process starts with aluminium profiles, usually 6063 or 6005 alloys, which can be unfinished, lacquered or anodized. These profiles are manufactured by extrusion, where the aluminium is heated to a certain temperature before softening and being passed through a die (designed with the desired shape) while cooling at the outlet until it solidifies to match that shape. In the machining process, the profile is cut to the required length, and modified by subtractive manufacturing process until the required geometry for the final piece is achieved.
The profiles are fed into our machining machines from a loading table and are introduced to the machining and cutting area by means of a feeder. It is in this way that the bars advance at the pace of the various operations that are carried out in the machine, with continuous profiles entering and pieces of the desired geometry coming out the end. Some of the common operations, in addition to cutting, are drilling, countersinking, threading, routing, reaming, stamping, milling, etc.
Profile machining is always linked to the cutting process, since the profiles are generally manufactured in lengths of between 6 and 7 metres. To achieve the desired length of the piece, cutting discs with tungsten carbide welded teeth are used, which guarantee the necessary repeatability and precision. Depending on the complexity of the part, more processes can be added to the machining.
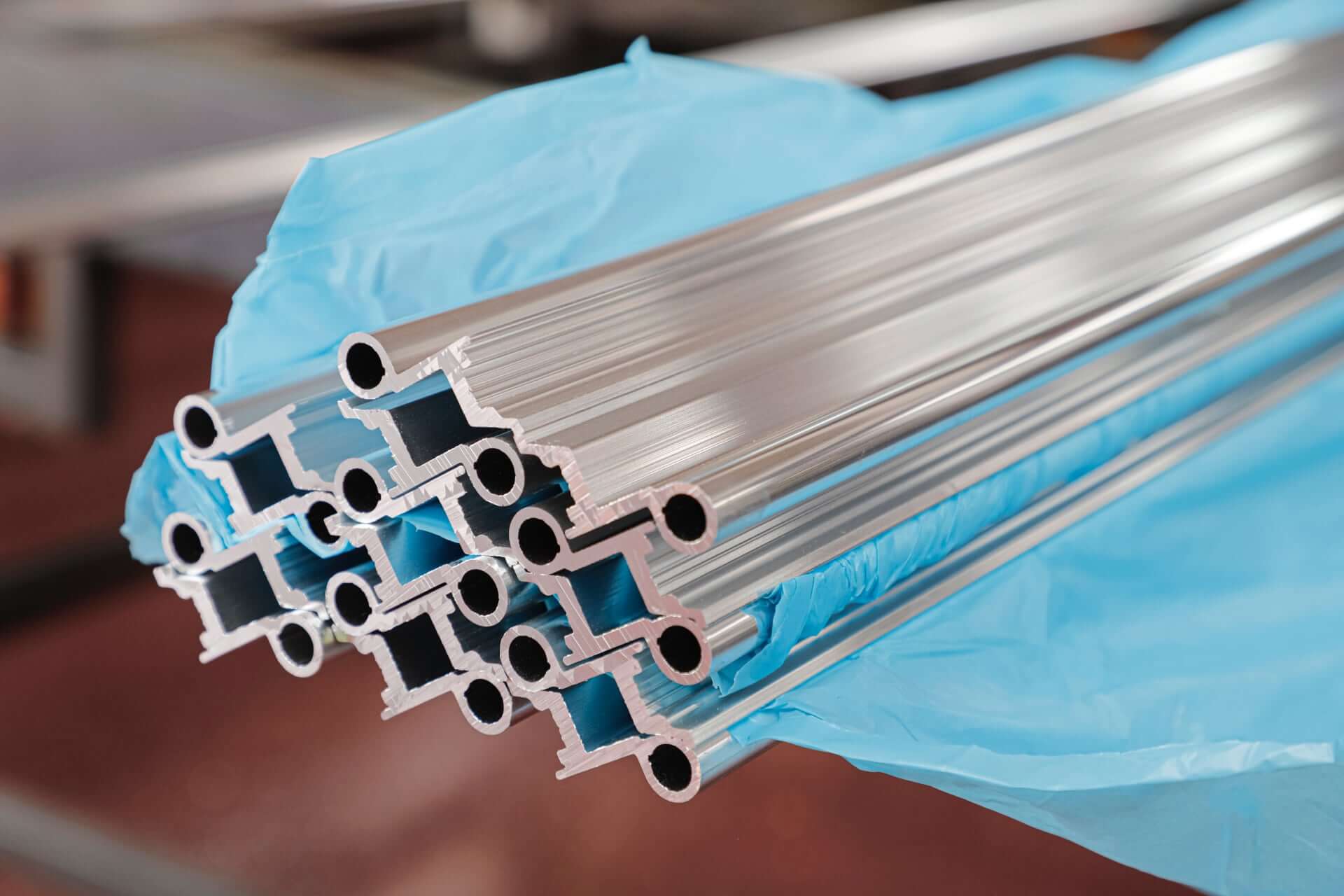
Advantages of manufacturing by machining aluminium profiles
Machining aluminium profiles offers several advantages: It allows us to save a lot of material since the profile has a geometry close to the final part (much better than starting with a solid bar). It enables fast and efficient production of serial parts thanks to high-speed machining. In addition, it provides dimensional precision, uniformity in the shape and finish of the part. This is a cost-effective process when large quantities of identical parts are produced, but it also has a reduced cost for smaller productions compared to other manufacturing processes provided, of course, that the minimum order for raw material is respected, which can be a limiting factor on occasion.
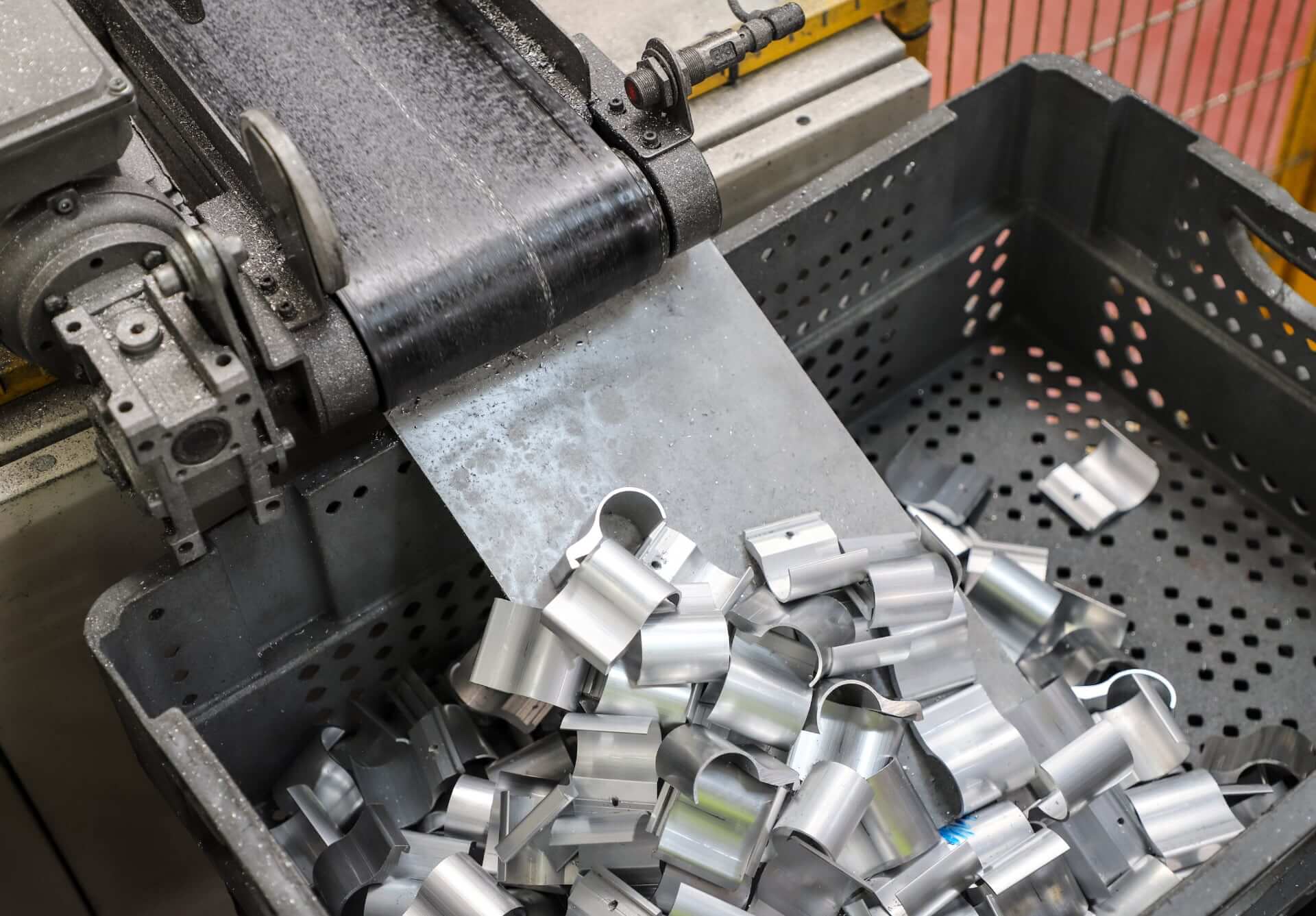
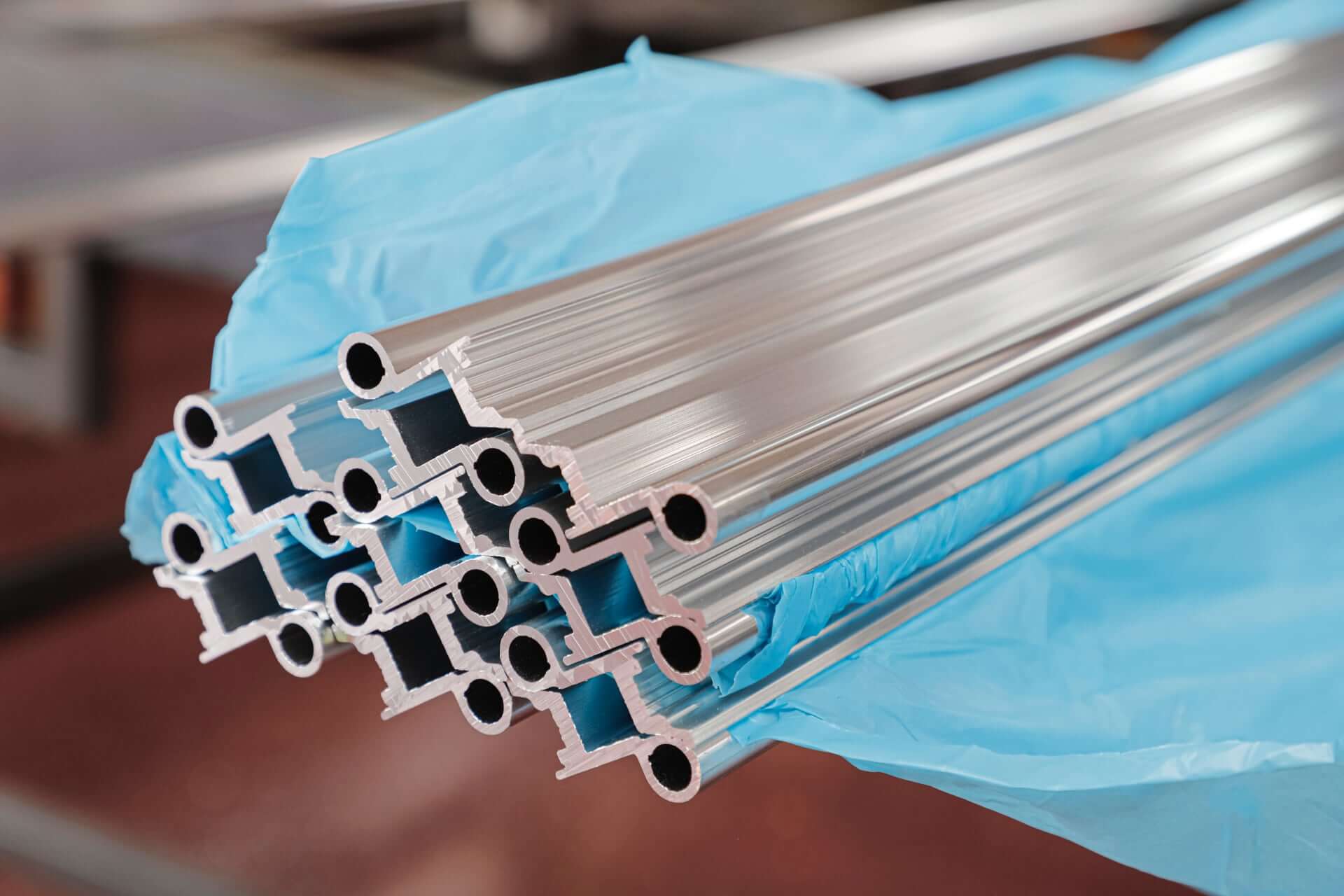
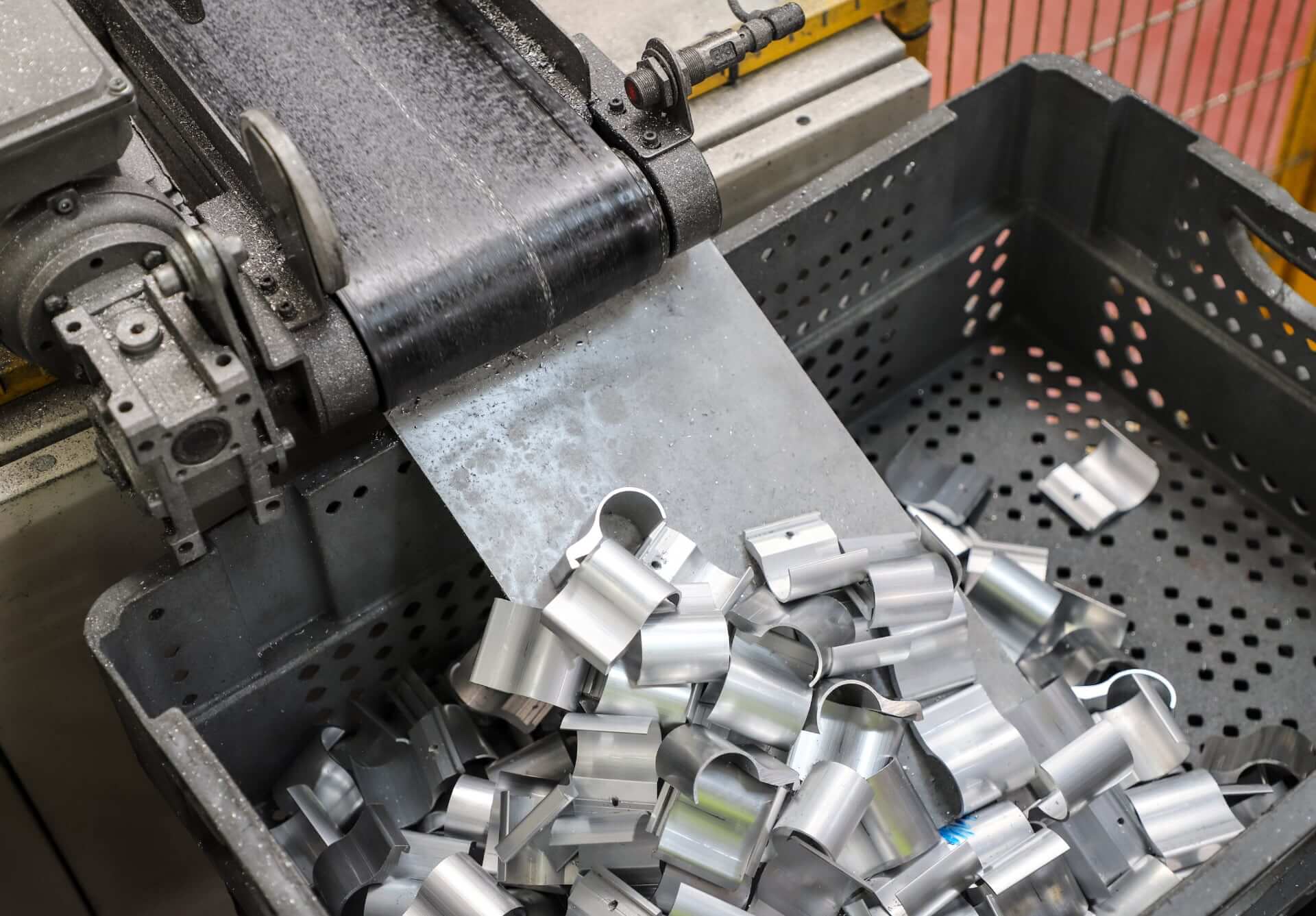
Frequently Asked Questions about Aluminium Profile Machining?
The process of machining aluminium profiles requires that the alloy has adequate strength, rigidity, toughness and corrosion resistance in addition to being an industrially available alloy that can be found on the market in adequate quantities.
These are some of the most commonly used alloys:
- Aluminium 6063: It is an aluminium alloy in the 6XXX series (AL-MG-Si), with magnesium and silicon as alloying elements. It generally has good mechanical properties and is thermally treatable and weldable. It is known as the architectural alloy due to its widespread use in all kinds of components in the architecture and construction sectors. It is thermally treatable, with different tempers applied (T5 or T6 normally) to provide greater hardness.
- Aluminium 6005: It is an aluminium alloy in the 6XXX series (AL-MG-Si), with magnesium and silicon as alloying elements, but with a notable Cr and Mn content, which produces an anti-crystallizing effect in the artificial ageing processes. It generally has good mechanical properties and is thermally treatable and weldable. It is used in architecture and construction, but also in sectors such as transport. Compared to 6063 aluminium, it does not need the same ageing process to achieve the same resistance levels, but it can also be tempered (T5, T6) to improve its properties.
For the correct definition of the alloy it is necessary to understand and evaluate the final use of the part, its surface finishes, the corrosion resistance requirements, the mechanical requirements, … and many more things.
Don’t worry, if you want to know more details about this, contact us and we will help you make the best deployment decisions.
On the one side, we have the tooling that is used to shape the aluminium profile in the extrusion process, which is known as the die. On the other side, aluminium is normally extruded in bars of between 6 and 6.5 metres, with a multitude of geometries, sizes and weights. For the management of these profiles, their transport, loading in machine, and subsequent machining, other tools are necessary such as: clamps and jaws, dies and custom designed tools (milling heads, discs, drill bits, etc.).
The tools and lubricant are also very important for correct high-speed machining. On the other hand, the material from which they are made and the coating we give them is also important for a better performance depending on the machining to be carried out. Likewise, the geometries of the specific cutting edge are also important for high-speed machining of extruded aluminium alloys.
Cutting discs, milling heads and stamping dies that can be incorporated into the aluminium profile machining process have to be manufactured and developed specifically. Extruded aluminium has a high tendency to stick to the tool due to its physical properties and the high temperature achieved in the high-speed machining process.
At STAC we have a tooling manufacturing department that is responsible for the design, manufacture and maintenance throughout the life of tooling and tools.
Some of the most important features to consider in the industrialization of an aluminium profile machining process are:
- Machine selection: we have various machines with different capabilities to incorporate processes (and tools) for the task of profile machining; the part to be manufactured must be correctly analysed, taking into account the machining operations involved and their complexity to assign the best possible machine. This machine has to be the one that allows us to manufacture the part correctly, with all the necessary tools, with the shortest cycle time.
- Tools: Discs, drill bits, milling heads, thread tappers, reamers… are necessary to perform the different material removal operations. These tools must be very precise and must have a high-quality surface finish to ensure the repeatability of the parts and the durability of each component, as well as the appropriate materials, coatings and cutting geometries.
- Guiding and profile clamping jaws: The machining machine must ensure that the part is in the correct position before the tool starts machining. In addition, during machining the profile cannot move or vibrate because this would impair the surface finish of the part and also affect the durability of the tool. For this reason, it is necessary that we define the correct guiding system, as well as clamping tools so that the bar is fixed and positioned with very high repeatability in the exact position. This helps to achieve a product with good manufacturing tolerances and repeatability between all parts in the manufacturing batch.
- Wear: The components involved in machining are very technical tools and sometimes they are subject to high wear. For this reason, each machine is equipped with lubrication, swarf removal and cleaning systems which, together with maintenance, aim to extend the life of the tools and tooling .
STAC guarantees its customers the life of the different tools during the life of the product.
If you want to know more about this point, we help you. Please contact us.
To manufacture aluminium profile machining parts, in addition to the importance of tooling, the machinery and the whole production line are also important. For these reasons our lines have:
- Storage area for the profiles as they leave the extruder.
- Bridge crane for loading profiles in the different production lines of each of the machining machines.
- Versatile machining machines with high-speed electrospindle that allow us to machine in any position within 180º around the extrusion plane. Therefore, we can directly machine 3 of the 4 faces if the profile is square section.
- Transfer type machining machines perform several operations simultaneously, which allow very good production rates to be achieved. They have the limitation of not being very versatile.
- Cutting and drilling machines are simpler machines for simpler parts.
- Process speed: The cycle time of the parts is something that we optimize in each case, always selecting the most appropriate machine, evaluating and taking into account the entirety of the necessary production processes and the functionality of the part.
- Process monitoring and data logging capabilities that allow us to identify how manufacturing is done and ensure that it is done under the same production parameters to ensure that we work in the most reliable way with the same conditions.
- Safety: Our machines are fully automated so that no worker comes into contact with moving areas when they are in production. Furthermore, we use the necessary PPE for proper protection in each process.
If you want to know more about our aluminium profile machining capabilities, please contact us.
Comprehensive manufacturing solution
Our comprehensive approach means we take care of every stage of the manufacturing process of machining parts, ensuring quality and efficiency at every step.
Below, we summarize the main services we offer.
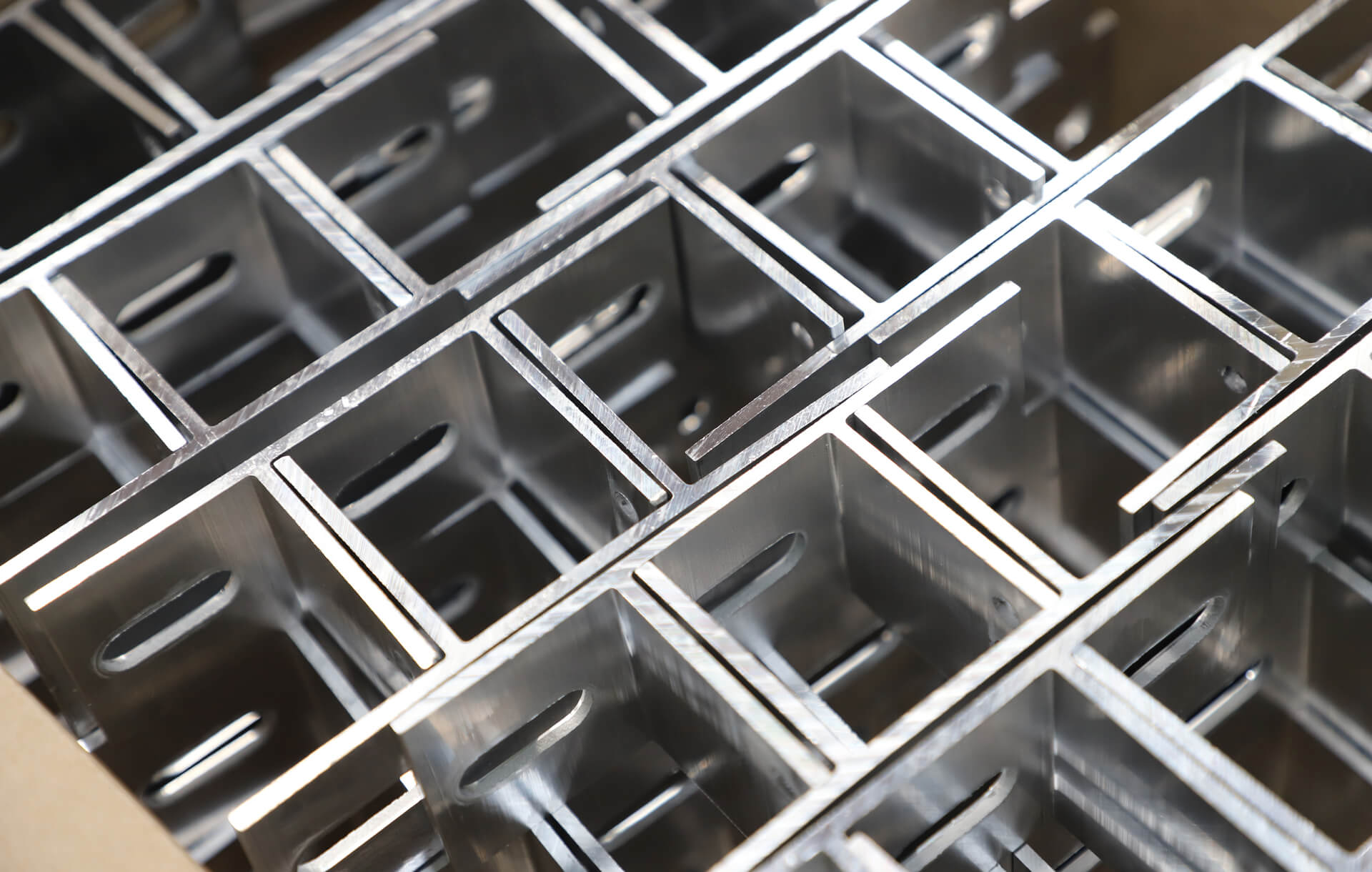
We want to be your integral partner in manufacturing machined aluminium profile parts.
We provide high quality solutions and added value at every step of the process.
We are ready to work closely with you.
Our priority is to help the customer achieve their goals
At STAC, we are committed to excellence and customer satisfaction.
We are ready to work closely with you and meet your specific requirements.
We have the means for our customers to receive their finished parts and only have to worry about their product.
Don’t hesitate to contact us to discuss your projects and how we can help you achieve your goals.
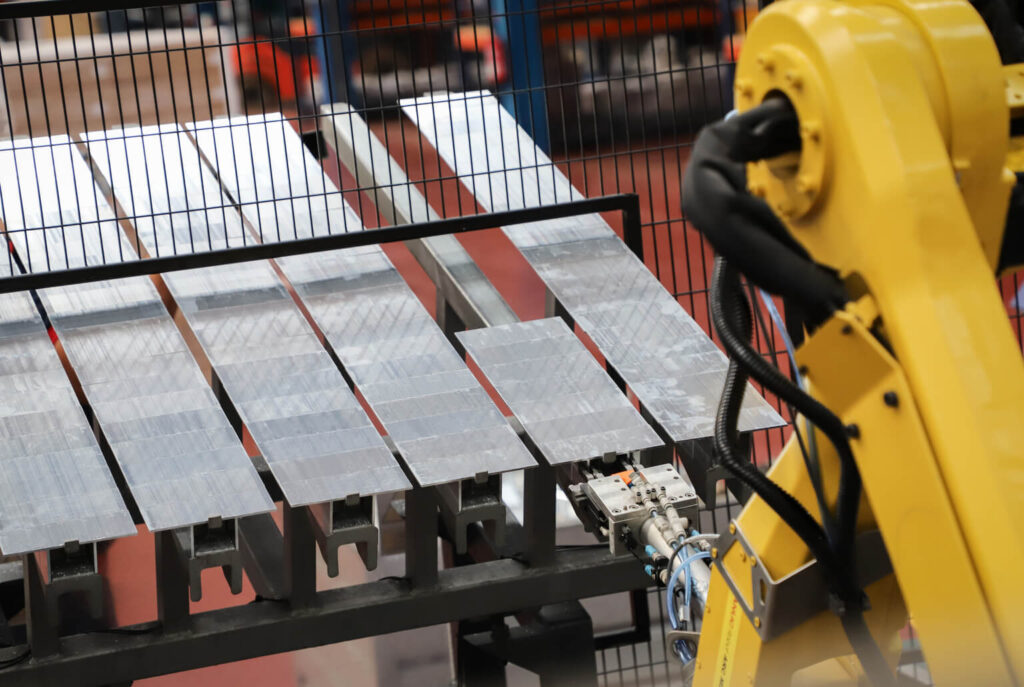
Post-machining processes of aluminium profiles
After machining the part has subsequent processes, the most common for aluminium profile parts are the following.
Deburring
It consists of removing burrs, sharp edges or unwanted protrusions from the piece. This can be done by manual or mechanical methods, or using specialized machinery.
Contact us
We’ll be happy to provide help for your projects and resolve any doubts as soon as possible