PRIMARY PROCESSES
Stamping of metal coil
At STAC we are specialists in the manufacture of parts by the machining of metal spools and we accompany our customers from conception through to the mass production of the desired part.
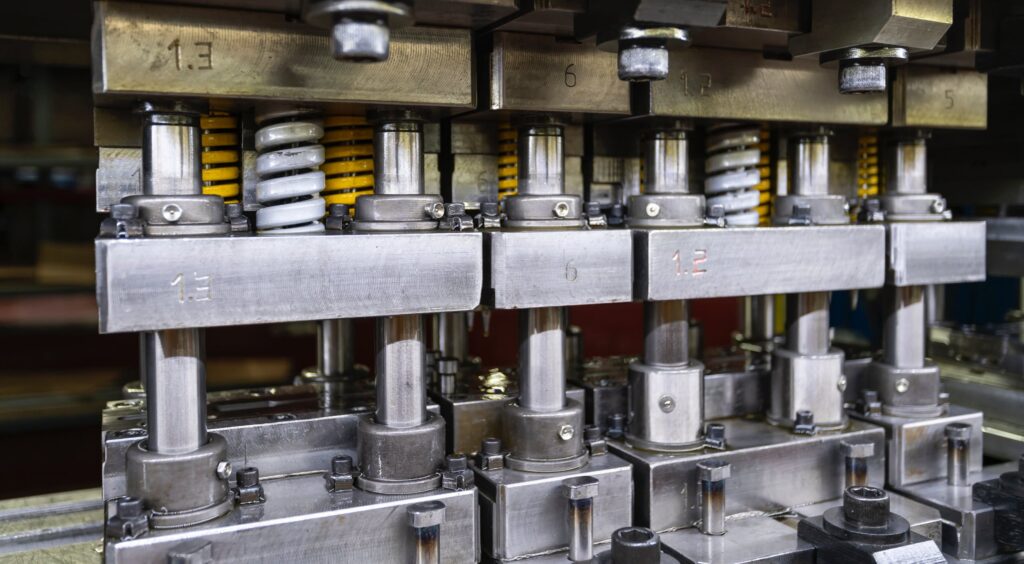
PRIMARY PROCESSES
Stamping of metal coil
At STAC we are specialists in the manufacture of parts by the machining of metal spools and we accompany our customers from conception through to the mass production of the desired part.
What is metal stamping?
Stamping from metal coil is a manufacturing process in which a continuous metal coil is stamp-cut to produce parts with specific shape and size.
The process begins with a metal coil that is usually made of steel or aluminium, although it could also be made of another metal. This coil is processed at room temperature, unrolled and fed into a stamping press. The press has a specific die mounted on its base, and these dies are the tools we design with specific shapes to bend, cut and shape the metal step by step, until the required geometry for the piece is attained.
After uncoiling, the metal coil is flattened by a roller train and fed into the die which is mounted on the press by a step-by-step feeder. The simplest parts can be made in a single step whilst others of greater complexity need 20 or even more steps to obtain the desired geometry. Each of these phases performs an additional operation on the metal such as: bending, inlay, embossing, punching, cutting…
Stamping uses the mechanical force of the press to deform and trim the metal at room temperature. The press applies a large force on the metal which causes it to deform plastically until it acquires the desired shape permanently. Depending on the complexity of the piece the stamping process will require more or less steps.
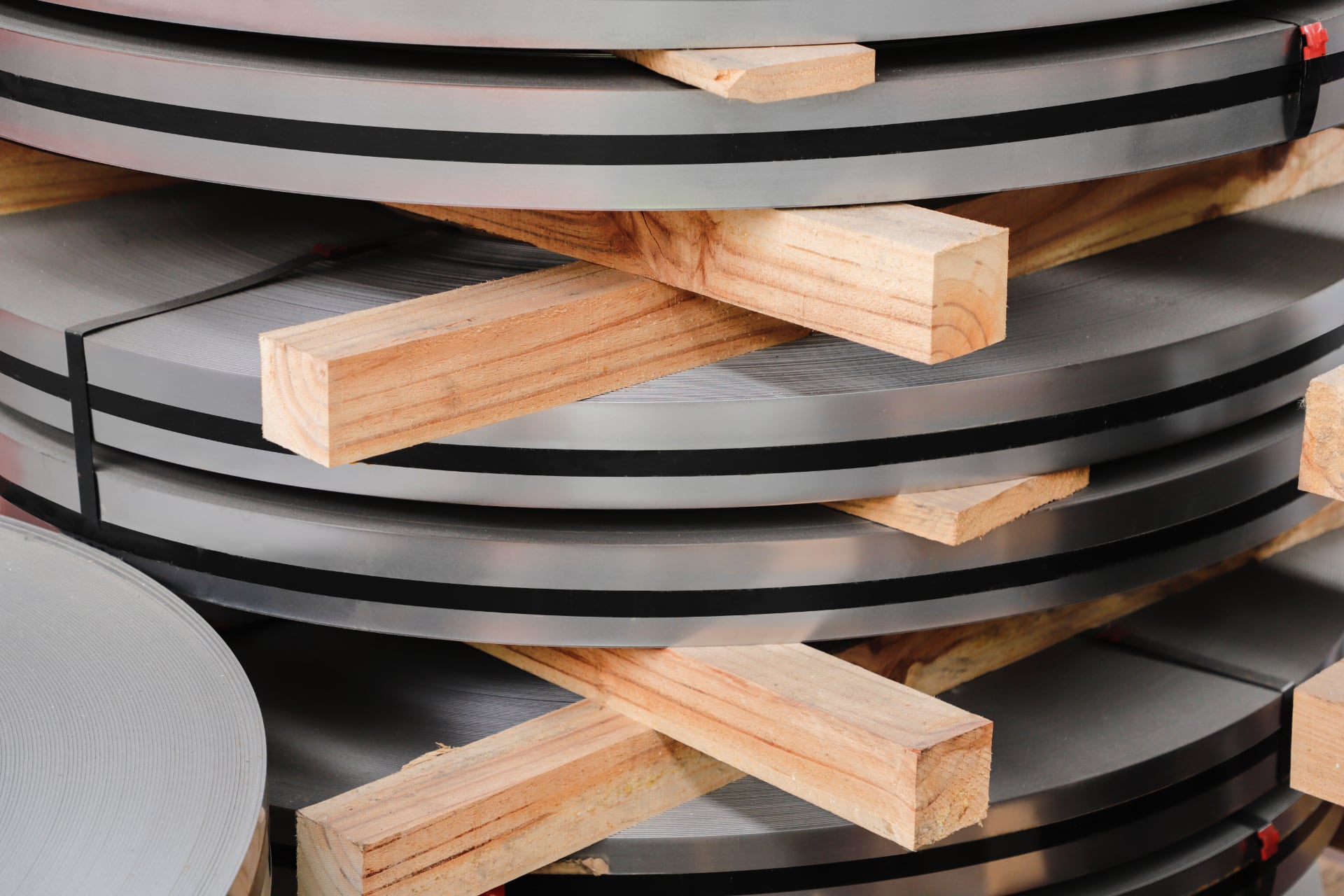
Advantages of manufacturing parts by stamping
Stamping offers several advantages in the manufacturing process of metal parts: It allows fast and efficient manufacturing of parts in high production volumes. In addition, it provides dimensional precision, uniformity in the shape and finish of the parts. This is a cost-effective process when large quantities of identical parts are produced.
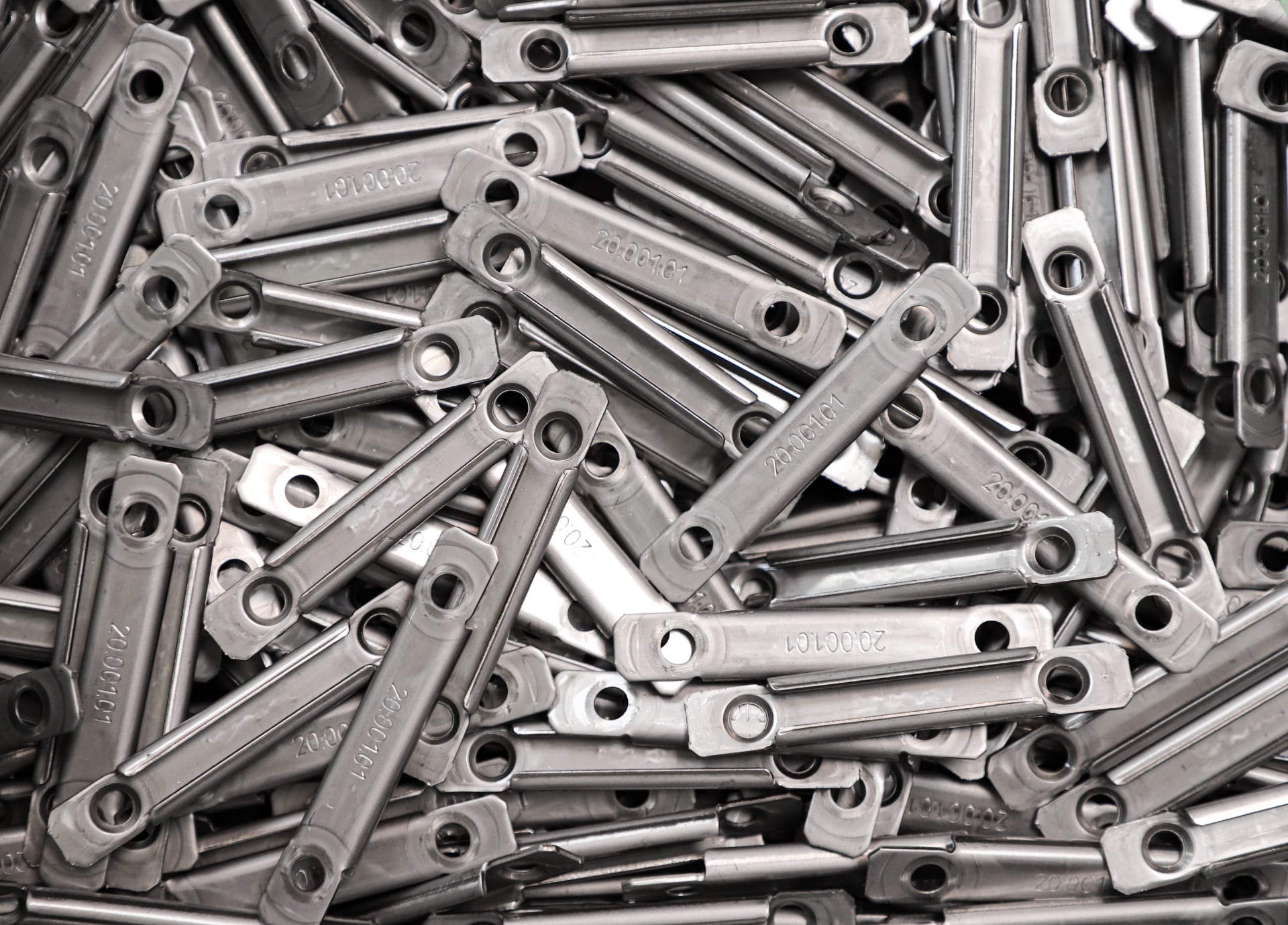
Sectors which use industrial metal stamping
Industrial stamping is a process that allows the transformation of various types of metal materials into a wide variety of parts for different purposes, so in practically all industrial sectors there is a high demand for stamped parts.
In industries such as automotive, aerospace, electronics and construction, stamping processes are used to manufacture mechanical components, structural parts and transmission components, among others.
At STAC we are specialists in this process and we accompany our customers from the initial idea to the final product.
Do you want to know how?
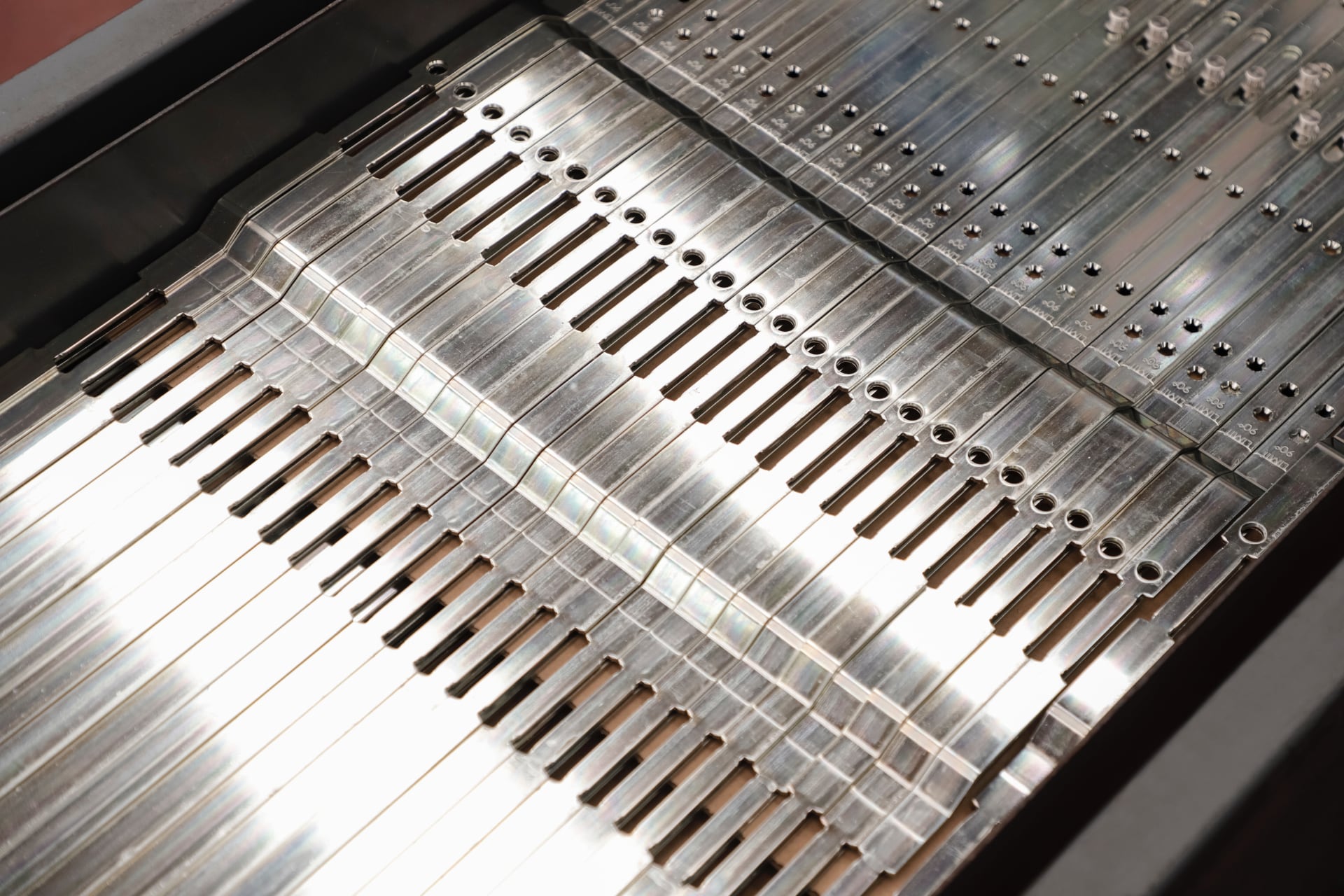
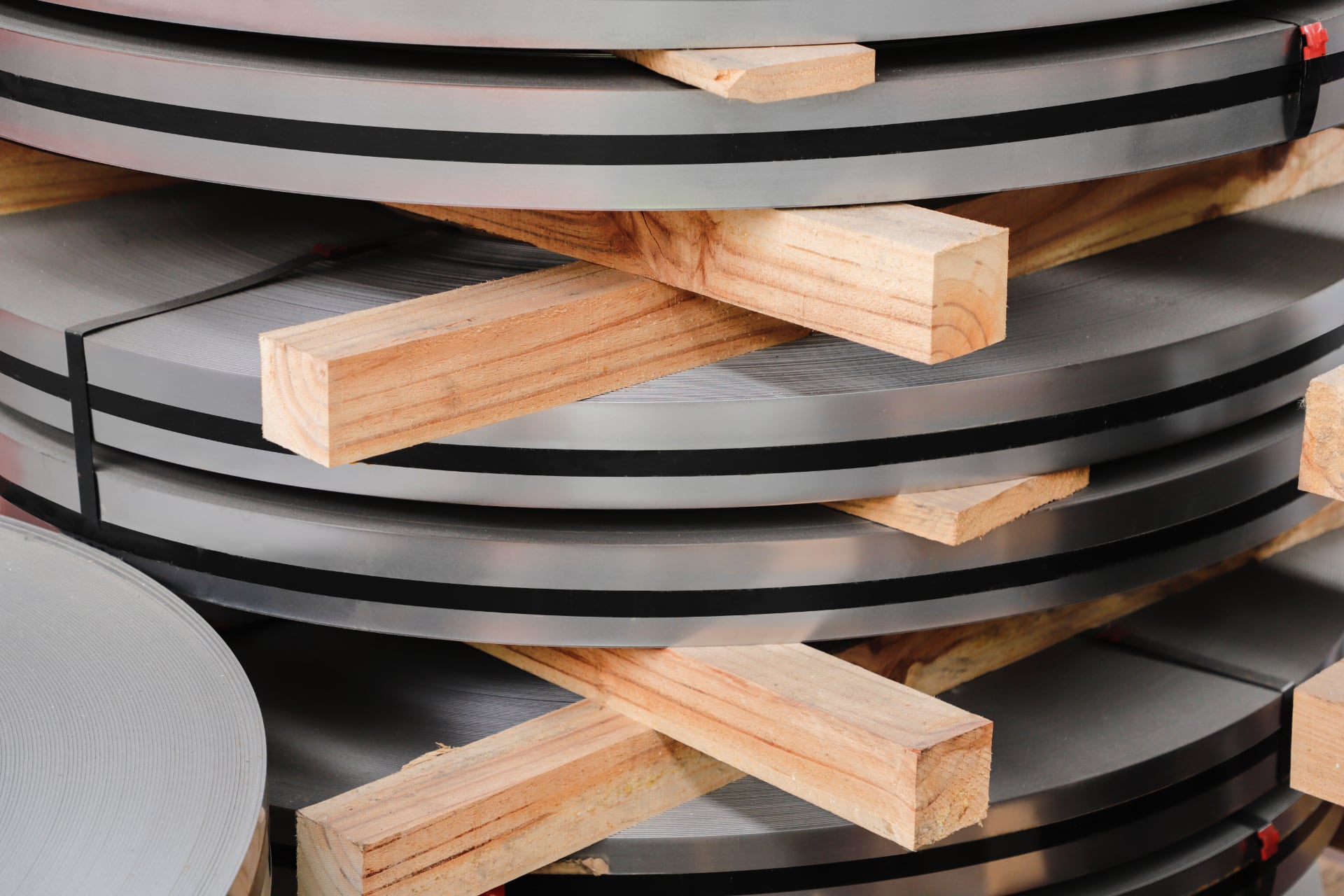
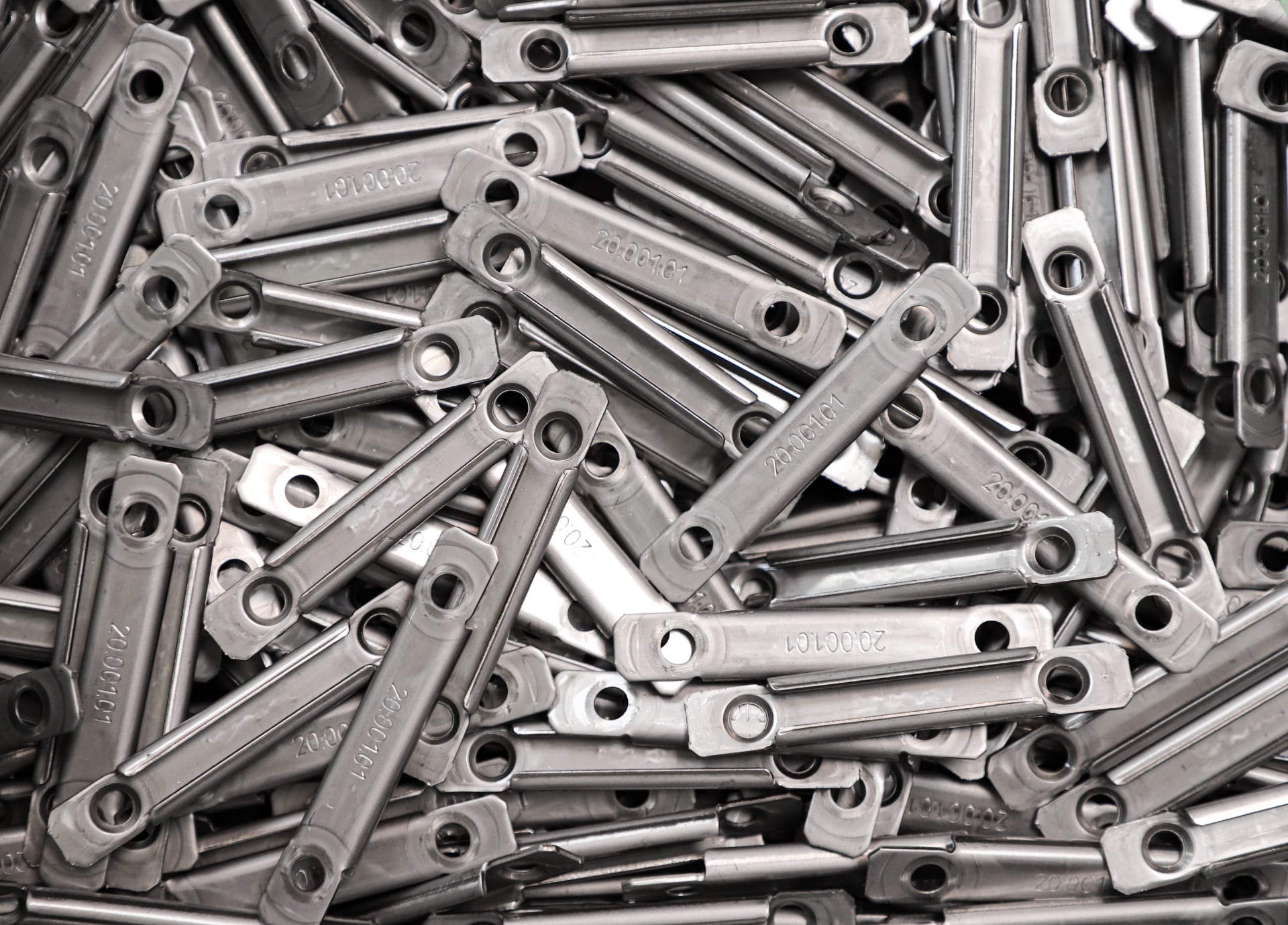
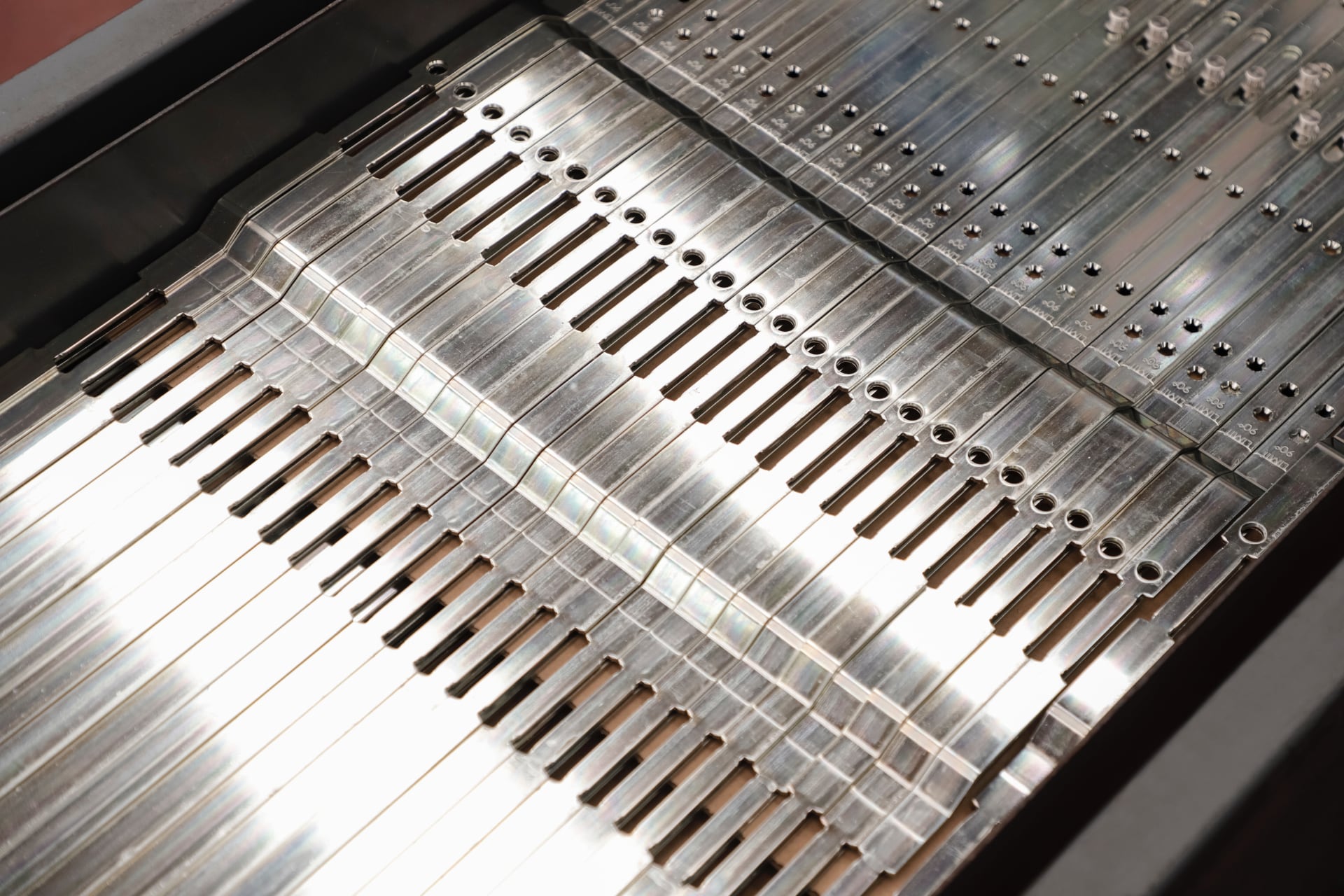
Frequently asked questions about stamping
The stamping process requires that the alloys are ductile, and that they have adequate strength, good formability, toughness and corrosion resistance. In addition, the alloy should also be a widely used alloy that can be found on the market in sufficient quantities without forcing the foundry to smelt a new batch that may involve a very large amount of material.
Here are some of the main materials used:
- AISI 304 stainless steel: Austenitic stainless steel. It is one of the most common and widely used grades of stainless steel. It is chosen for numerous applications in different sectors due to several desirable characteristics and properties: corrosion resistance, widely available, good formability and weldability, high resistance to high temperatures.
- AISI 430 stainless steel: Ferritic stainless steel. It is also a very common grade of stainless steels but it is cheaper than AISI 304 because it does not have nickel in its composition. It has good corrosion resistance in normal atmospheric environments and in mildly corrosive environments. Its corrosion resistance is lower than AISI 304.
- AISI 301 stainless steel: Austenitic stainless steel. Its high corrosion resistance combined with its good deformability, elastic recovery and aesthetic appearance make it very versatile. It is suitable for applications in various sectors: automotive, electronics, medical and pharmaceutical. It is also suitable for food packaging and for the chemical and petrochemical industry, among others.
- Aluminium Alloy 5005: It is a commonly used aluminium alloy that belongs to the group of magnesium alloys. It is used, for example, in the construction of buildings and structures due to its light weight, corrosion resistance and ease of forming. It can be used in cladding, facade panels, ceilings, gutter systems and other architectural components. It is also used in the automotive industry, in the signage, container and packaging industries and is suitable for marine applications due to its corrosion resistance in saline environments. It can be used on ships, boats and other nautical equipment where good corrosion resistance and high strength-to-weight ratio are required.
- Aluminium Alloy 1050: It is a very pure aluminium alloy (99.5%) and is usually applied where mechanical resistance is not a critical factor such as electrical conductors, light reflectors, aesthetic covers and chemical components. It has very good deformability and allows varied finishes such as aesthetic anodizing.
- To select the correct alloy, it is necessary to know the final use of the part, its surface finish, the requirements of corrosion resistance, the mechanical requirements that the part should have, … and many more things.
Don’t worry, if you want to know more about this, please contact us.
The metal enters the die at room temperature and therefore in a solid state, the press is lowered and all the tons of force are applied to the tooling. This is why stamping dies have to be made of special steels. These are steels alloys specifically for these applications which come with high manufacturing costs. Before going into production and while they are being processed, they have to be subjected to various, highly-controlled heat treatments, so that their characteristics are optimal. These steels reach very high hardnesses while maintaining very high toughness; this is necessary to keep the cutting edges sharp and also so they can absorb impacts without breaking.
At STAC we have a tooling manufacturing department that is responsible for the design and manufacture of the punch and die set and maintenance throughout their service life. In the stamping process the tooling require a lot of maintenance work since it is necessary that all the punches and dies are kept in perfect condition to perform the operation of cutting or forming correctly, this is something that we take care of after each manufacturing run.
Some of the most important characteristics to consider are:
- Materials for the different parts of the die: these materials must be strong and durable enough to withstand the high forces of the stamping process, depending on the part of the die we use specific steels depending on the thickness and the material of the part to be stamped.
- Materials and wear resistance: The materials used must also withstand abrasive and adhesive wear. To increase resistance we apply PVD coatings on steel when necessary, always looking for the balance between initial cost and savings on maintenance.
- Punches and dies: The die press consists of punches and dies to perform the different forming operations. These elements must be very precise and have a surface finish with high quality to ensure the repeatability of the parts and the durability of each component. It is very important to correctly define the gaps between punch and die depending on the material to be stamped and the thickness, as this will affect the quality of the piece and give a better finished product.
- Guiding and centring system: The die cutter must ensure that the part is in the correct position after each step and before the press comes down completely. Thus, it is necessary that we define the correct coil guiding system and the correct centring system so that the coil is located in the exact position to facilitate high repeatability.
- Coil width, steps and die size: The die cutter must be designed according to the part to be manufactured, the coil width should allow us to produce the part correctly with the least consumption of raw material. The metals used must be correctly dimensioned to withstand all the forces involved in the process and also the steps to be carried out must be rigorously analysed to achieve the desired final piece, sometimes making prototypes before defining the operations and / or their order.
- Wear and inserts: Stamping dies are very technical tools. When we work with stainless steels the wear on the various components is high, for this reason each die is full of small inserts to simplify and reduce maintenance costs after each manufacture.
STAC guarantees the die during the life of the tooling.
If you want to know more about this point, we can help you. Contact us.
To manufacture stamped parts, in addition to the importance of the tooling, the press and the whole production line are also important. For these reasons our stamping production lines have:
- Motorized winder to unwind the coil in a controlled and automatic way.
- Roller train at the winder outlet to ensure both horizontal and vertical flatness of the coil.
- CNC feeders to the presses that allow us to correctly advance the material step by step.
- Our presses have a loop system that allows us to efficiently and continuously control the coordination between the function of the winder and the function of the CNC feeder.
- Process speed, the revolutions per minute that the press can provide is also an important parameter that we take into account to be able to offer our customers a competitive process.
- Process monitoring and data logging capabilities that allow us to identify how manufacturing runs are done and ensure that they are performed under the same production parameters to ensure in the most reliable way that we always work under the same conditions.
- Safety: Our machines are fully robotised so that no worker comes into contact with the moving areas of the press when they are in production.
If you want to know more about our stamping capabilities, please contact us.
Comprehensive manufacturing solution
we take care of every stage of the manufacturing process of stamped parts, ensuring quality and efficiency at every step.
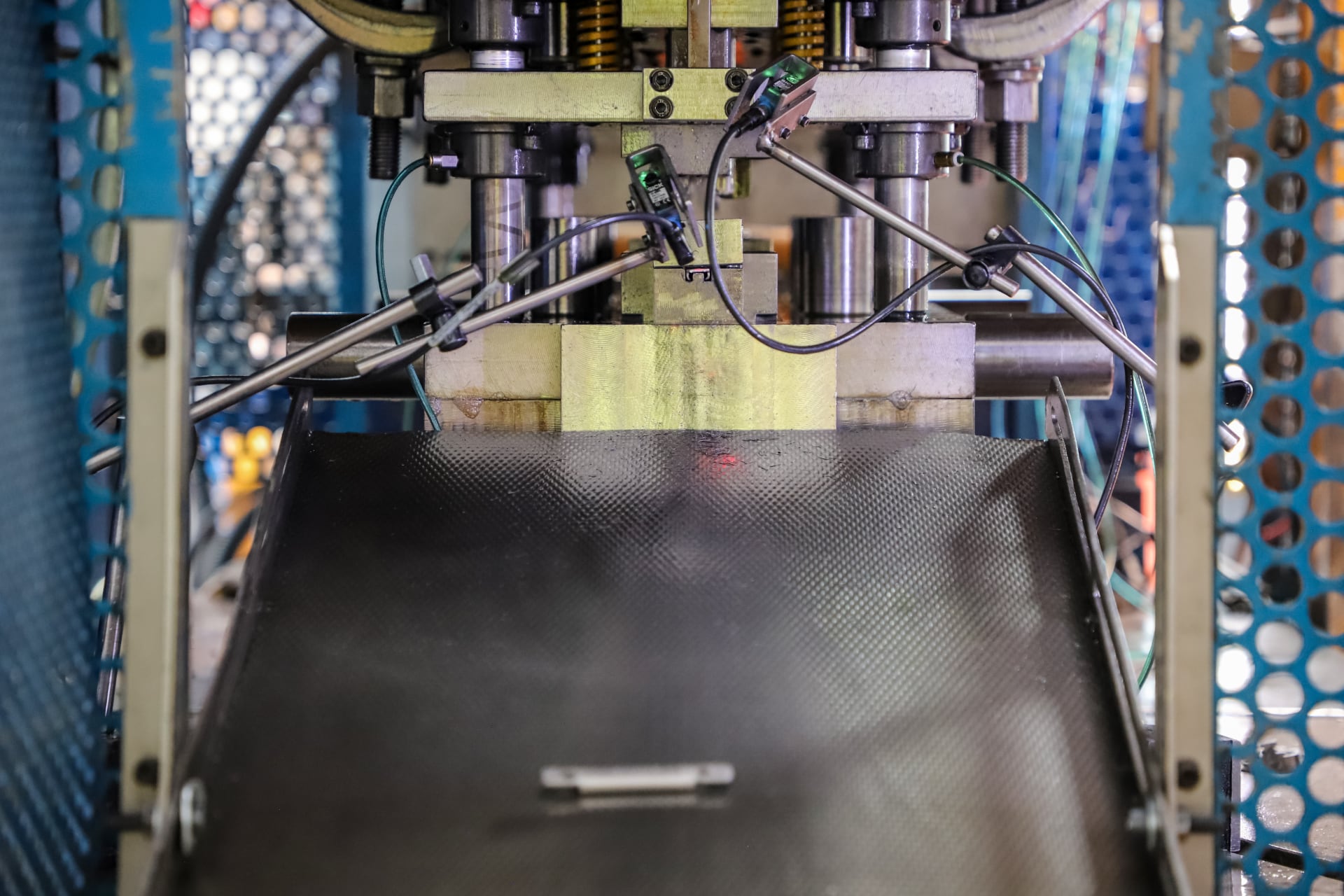
At STAC, we want to be your comprehensive supplier of stamped parts.
We want to provide you with a comprehensive service and we take care of the entire process, from the initial design to the final delivery of the finished product where you request it.
Our priority is to help the customer achieve their goals
At STAC, we are committed to excellence and customer satisfaction. We would like to be your integral partner in the manufacture of stamping parts, offering high quality solutions and added value at every step of the process. We are ready to work closely with you and meet your specific requirements.
Don’t hesitate to contact us to discuss your projects and how we can help you achieve your goals.
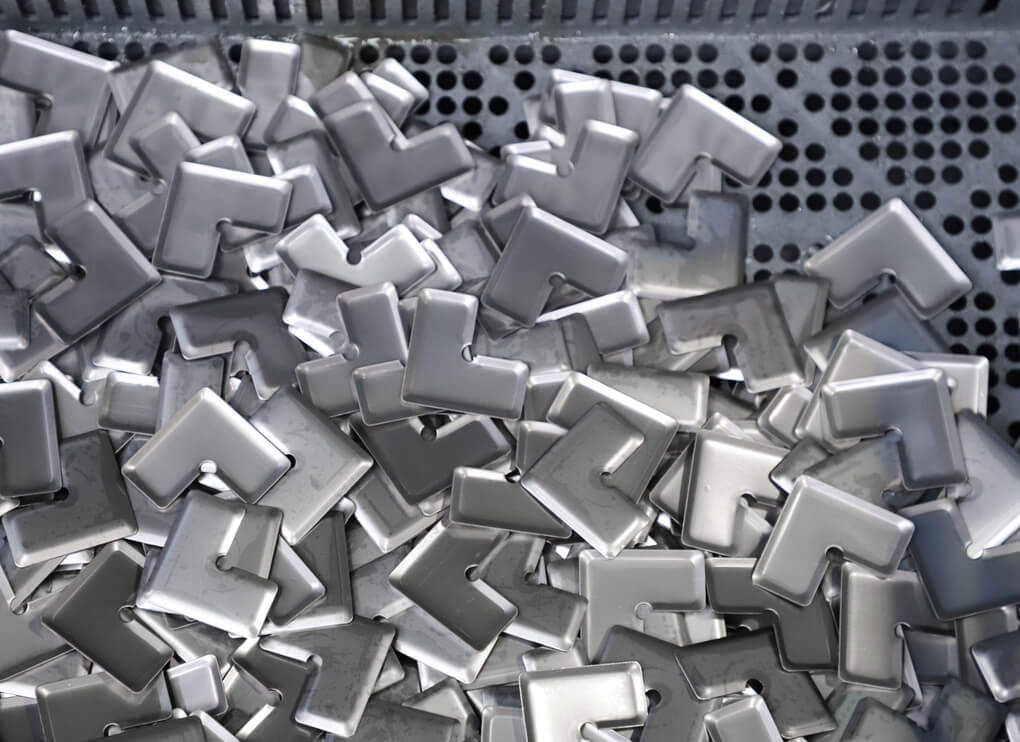
Post-stamping processes
The most common post-stamping manufacturing processes are the following:
Deburring
It consists of removing burrs, sharp edges or unwanted protrusions from the moulded piece. This can be done by manual or mechanical methods, or using specialized machinery.
Contact us
We’ll be happy to provide help for your projects and resolve any doubts as soon as possible