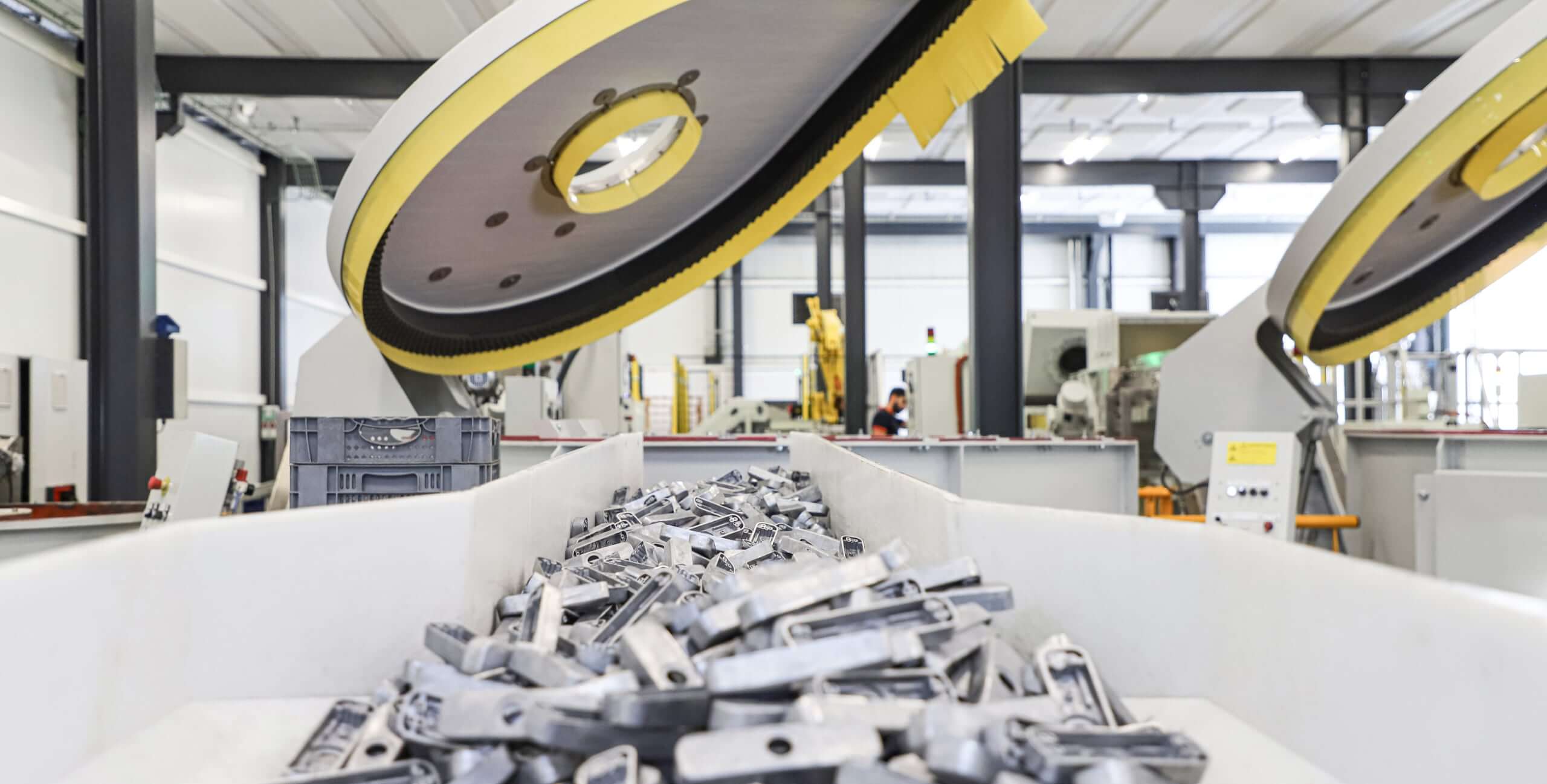
SECONDARY PROCESSES
Mechanical surface treatments
Mechanical surface treatments allow us to improve the surface properties of materials and components, both in aesthetic and functional terms, increasing their strength, durability and overall performance.
STAC offers various possibilities in terms of mechanical surface treatments. Each process has its own characteristics that will be chosen according to the finish sought in the part. STAC has a team of Design and Industrialization Engineers who advise our customers for the choice of the right surface treatments for each project.
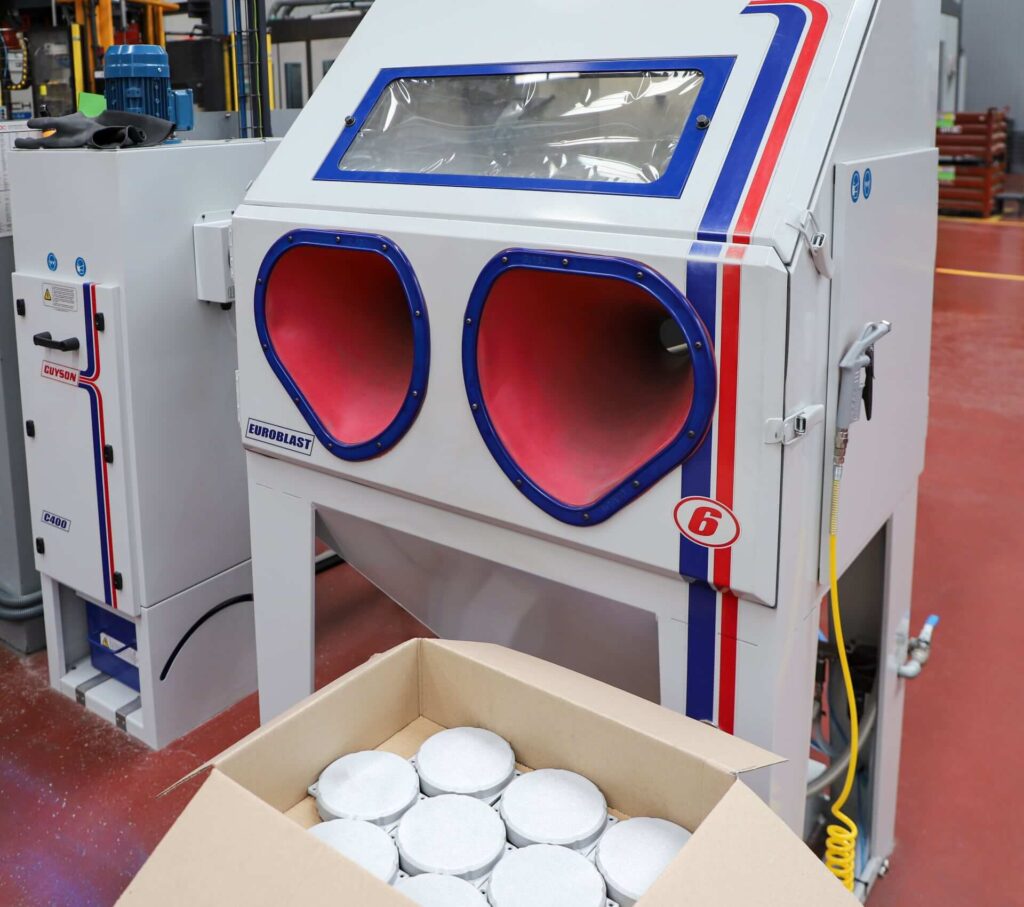
Shot blasting
It is a mechanical surface treatment process that involves the pressurised firing of particles against the surface of a product to reduce irregularities and obtain a more uniform surface, whether it is to clean, wear, texture or prepare it for coatings.
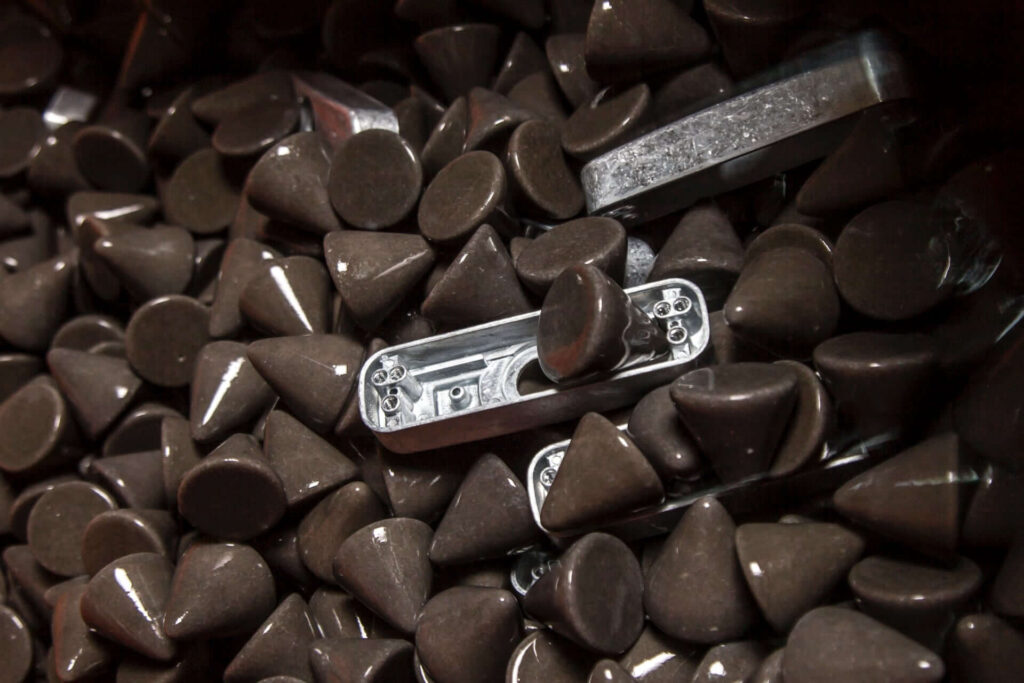
Vibration
The surface treatment by vibrating consists, as its name suggests, in vibrating the pieces inside a tank or drum together with abrasive particles of various geometries, sizes and qualities to homogenize the surface of the pieces and eliminate small burrs or sharp edges.
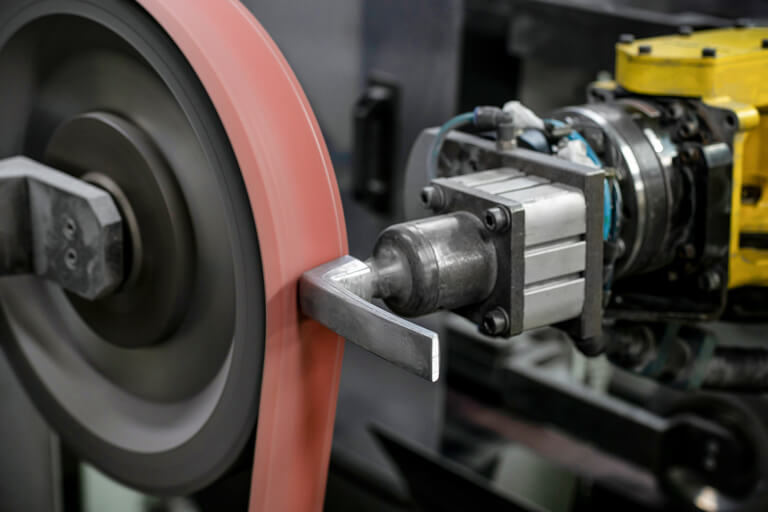
Sanding
Sanding is a mechanical surface treatment that consists of generating a relative movement between an abrasive element (sandpaper) and a surface, achieving a greater or smaller removal of material from the surface depending on the size of the grain (grit) of the sandpaper.
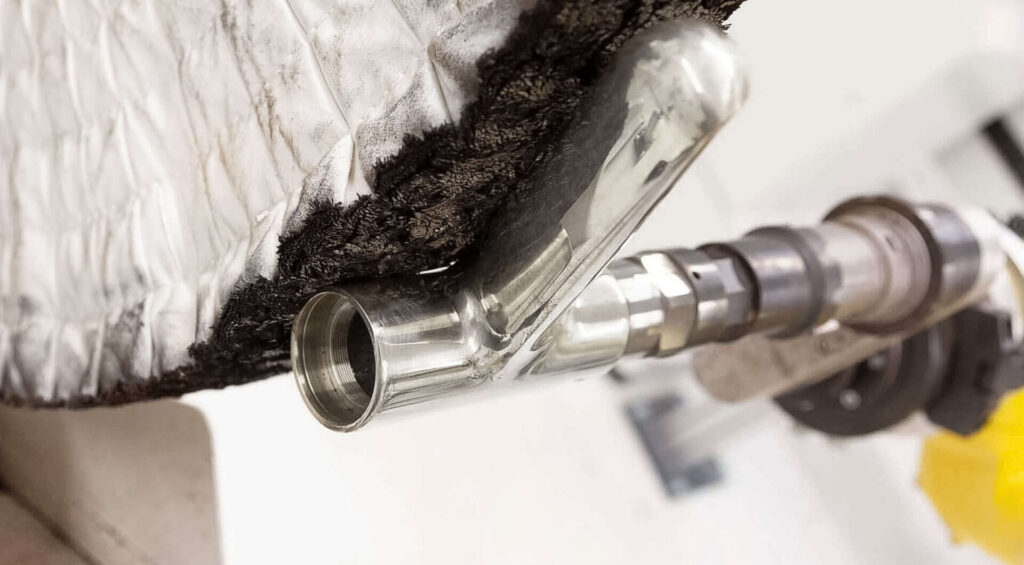
Polishing
Polishing is a mechanical surface treatment similar to sanding, but which allows to achieve finer finish surfaces, even mirror. Textile pads are used instead of sandpaper, which, together with various polishing products, allow very smooth surfaces to be obtained.
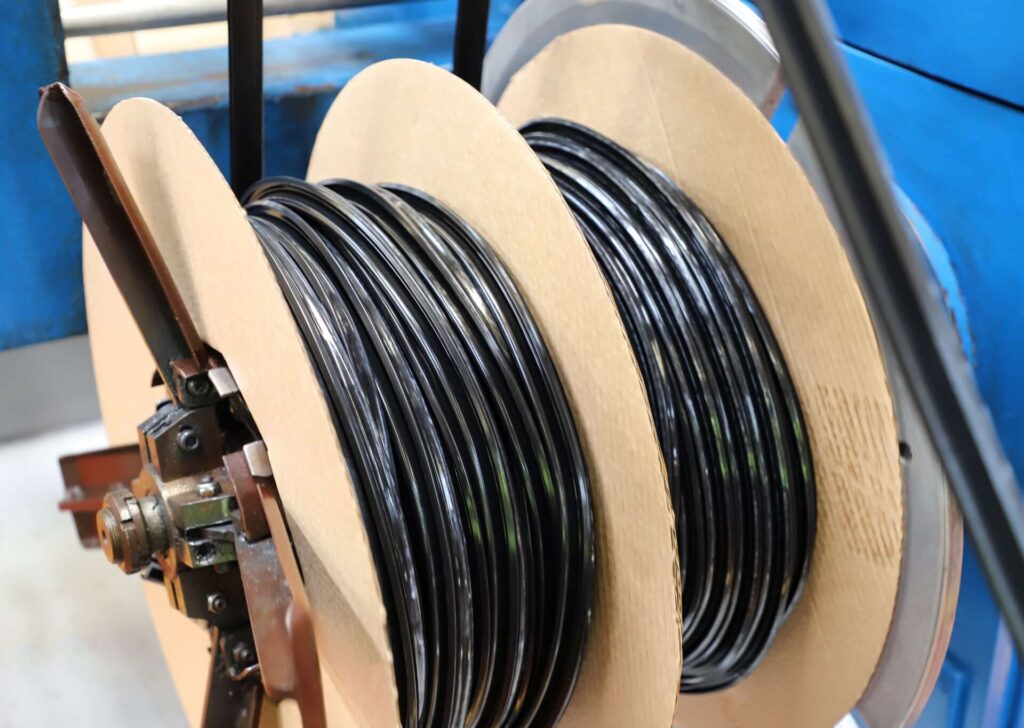
lubricant surface treatments
Lubrication is a surface treatment that is usually applied to rubber seals made of rubber, due to their high adhesion to surfaces. Rubber seals made of thermoplastic should not need this treatment since these materials have a friction coefficient lower than rubbers.
We offer three main types of lubrication
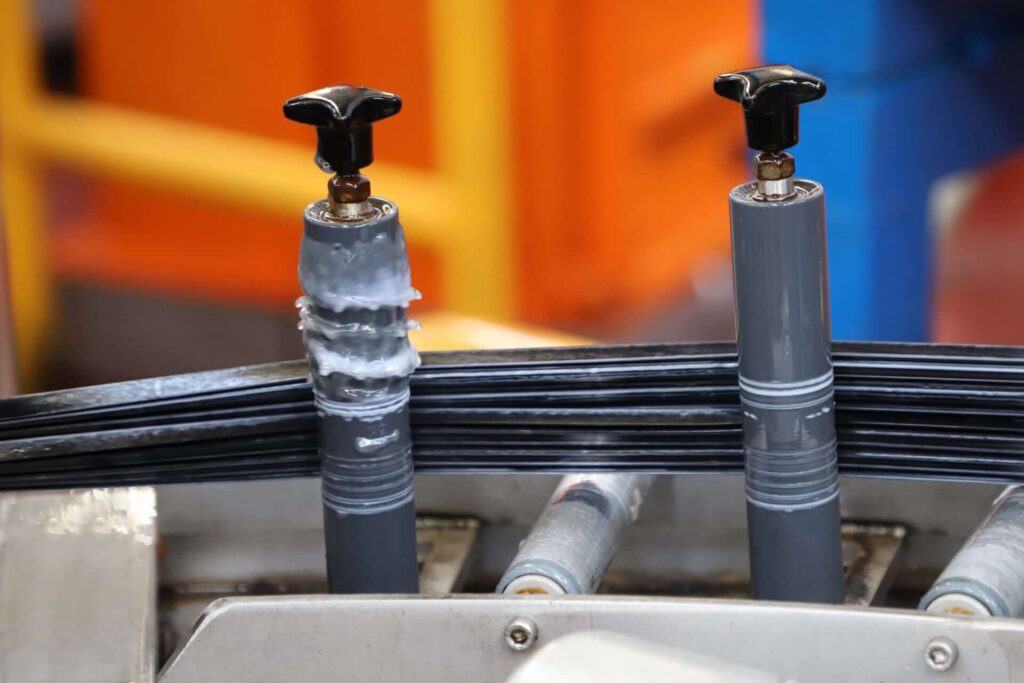
Lubrication by silicone emulsion
It is the most widespread and economical lubrication method. It is a lubricating silicone that is evenly dispersed in water. It is a thermostable and non-toxic product. It is widely used in industrial applications.
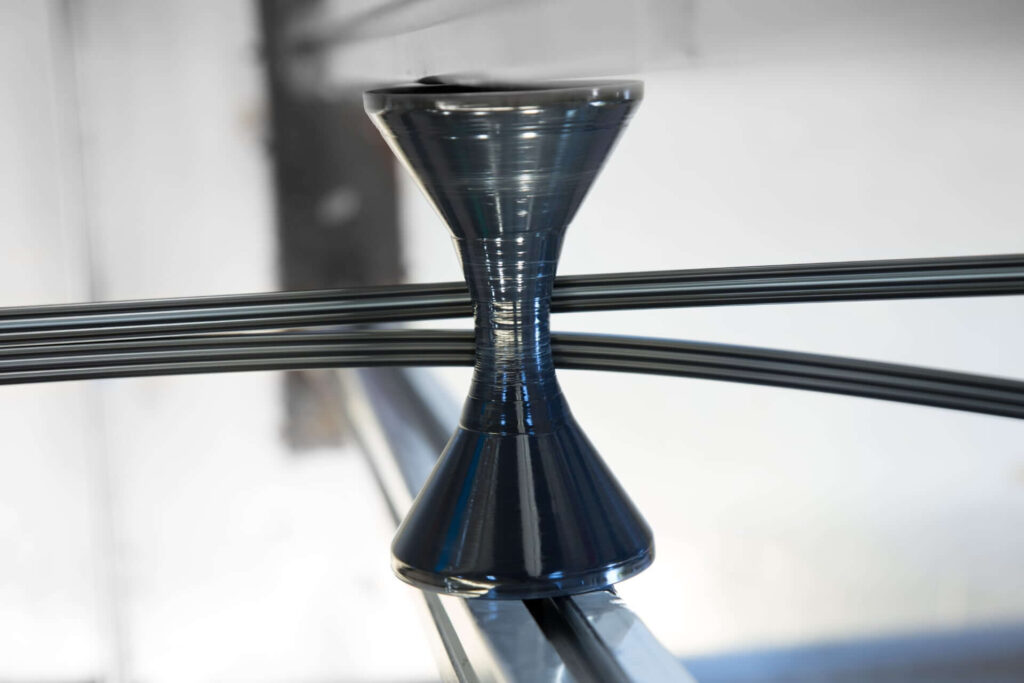
Organic lubricant
It is a polymeric, silicone-free lubricant free. Once dry it forms a film on the seals. It is used to substitute silicone emulsion.
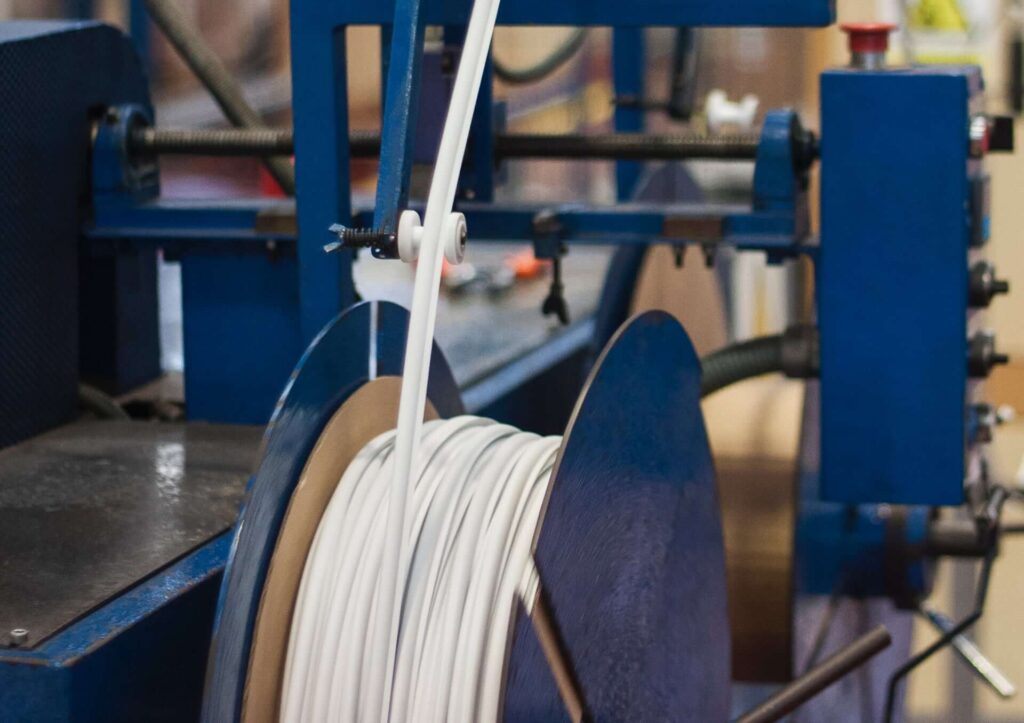
Lubrication by talc powders
It is a finely-ground, white, magnesium silicate hydrate powder. It provides a dry finish and eliminates any possibility of dripping. It is usually applied on any type of rubber gasket made of rubber to facilitate assembly.
Contact us
We’ll be happy to provide help for your projects and resolve any doubts as soon as possible