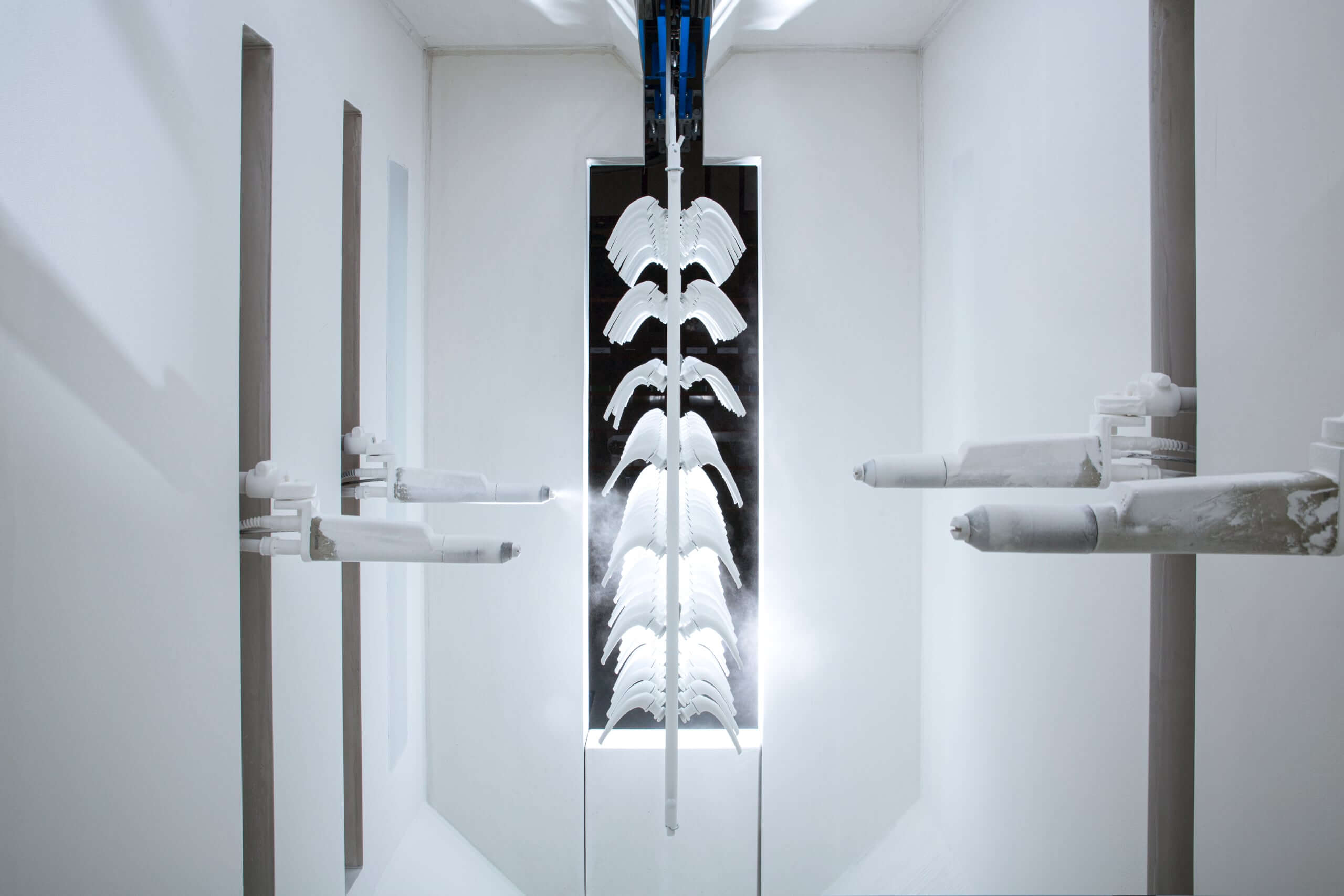
SECONDARY PROCESSES
Finishing treatments: decorative or protective
Beyond the manufacture of the piece and its geometry, at STAC we have several auxiliary processes that allow us to give the pieces a decorative or protective finish, from a mirror finish in the colour of your choice from the RAL chart, to a decorative finish, or even just a simple protection to ensure its durability.
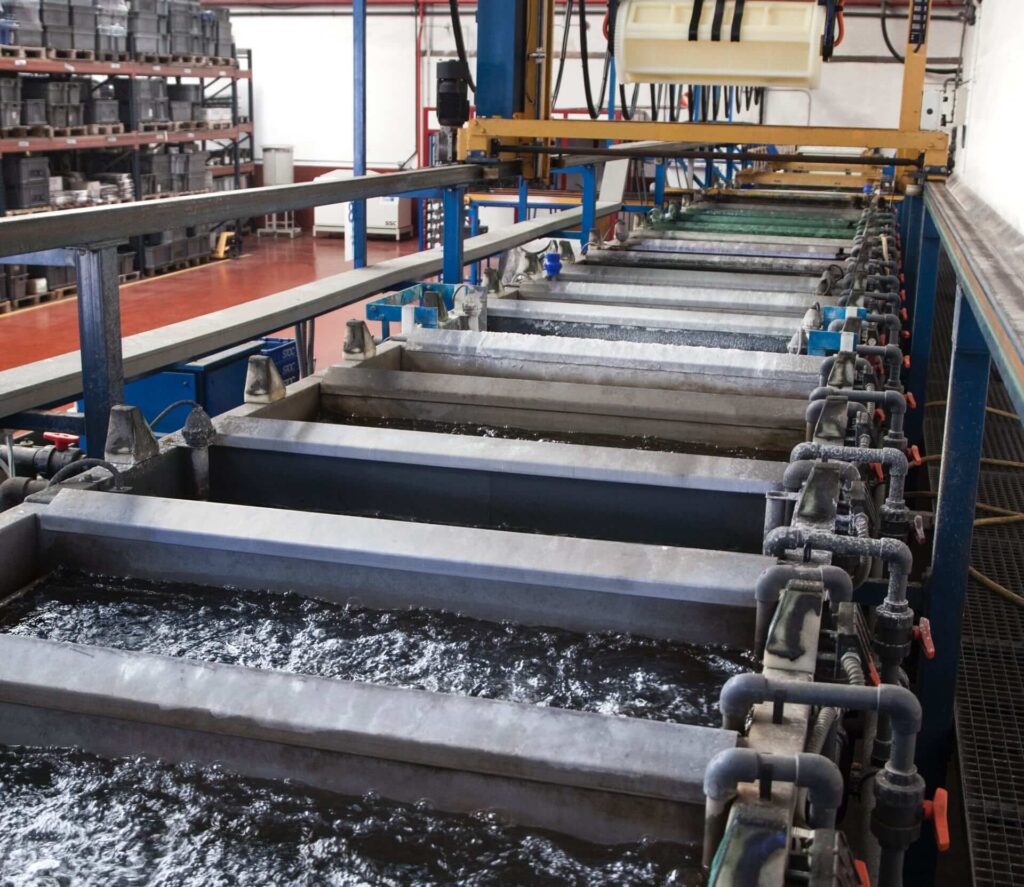
Electrolytic zinc plating
This treatment consists of an electrolytic bath of zinc and other elements that can be given to steels and zinc alloys (such as zamak). to generate a bonded protective layer throughout the surface which ensures protection against wear and corrosion during the life of the part.
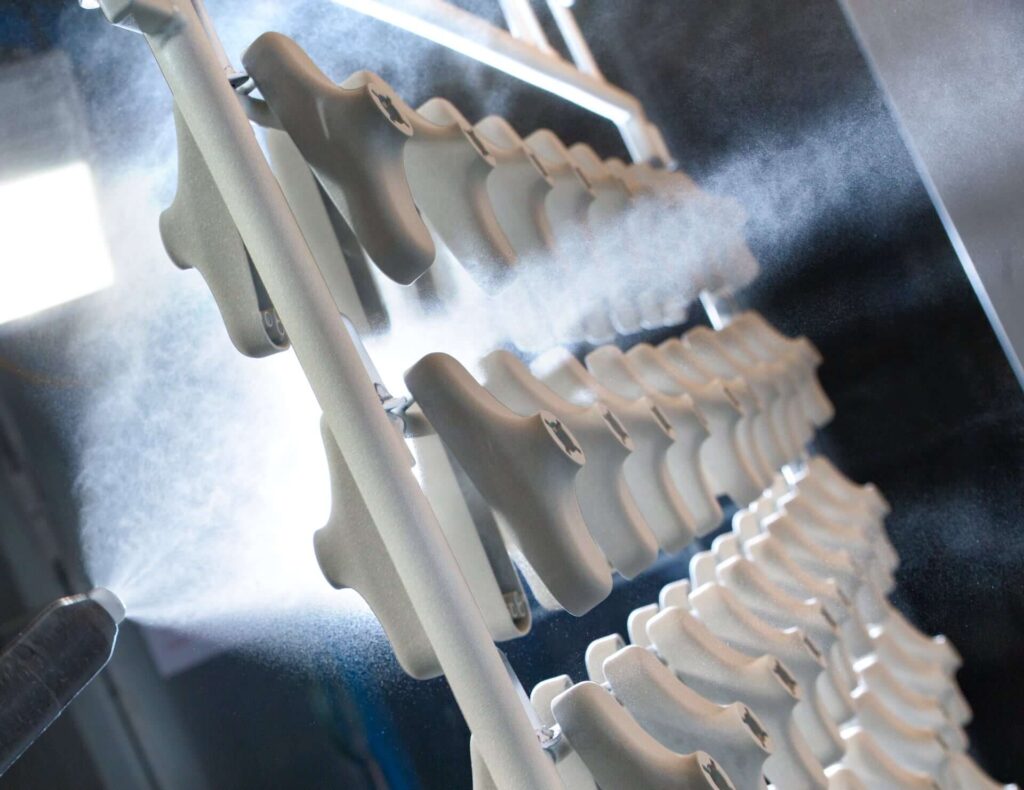
Powder coating
This decorative finishing treatment consists of the application of a powder paint on parts made of conductive materials With the application of an electrostatic current the particles adhere to the surface; the part is then baked in an oven to achieve the final fixing and a homogeneous surface.
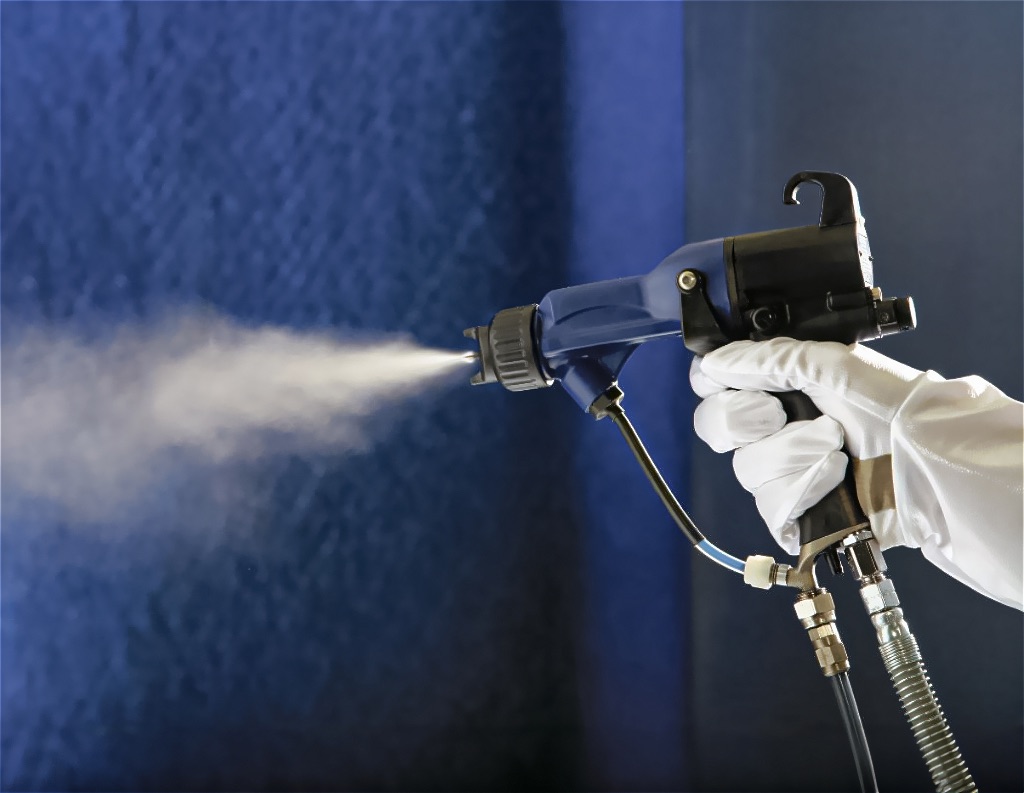
Liquid paint lacquering
A layer of liquid paint, known as lacquer, is applied to the surface of a piece in order to improve its appearance, protect it from corrosion and provide a durable and resistant finish. It is a widely used process in various industries.
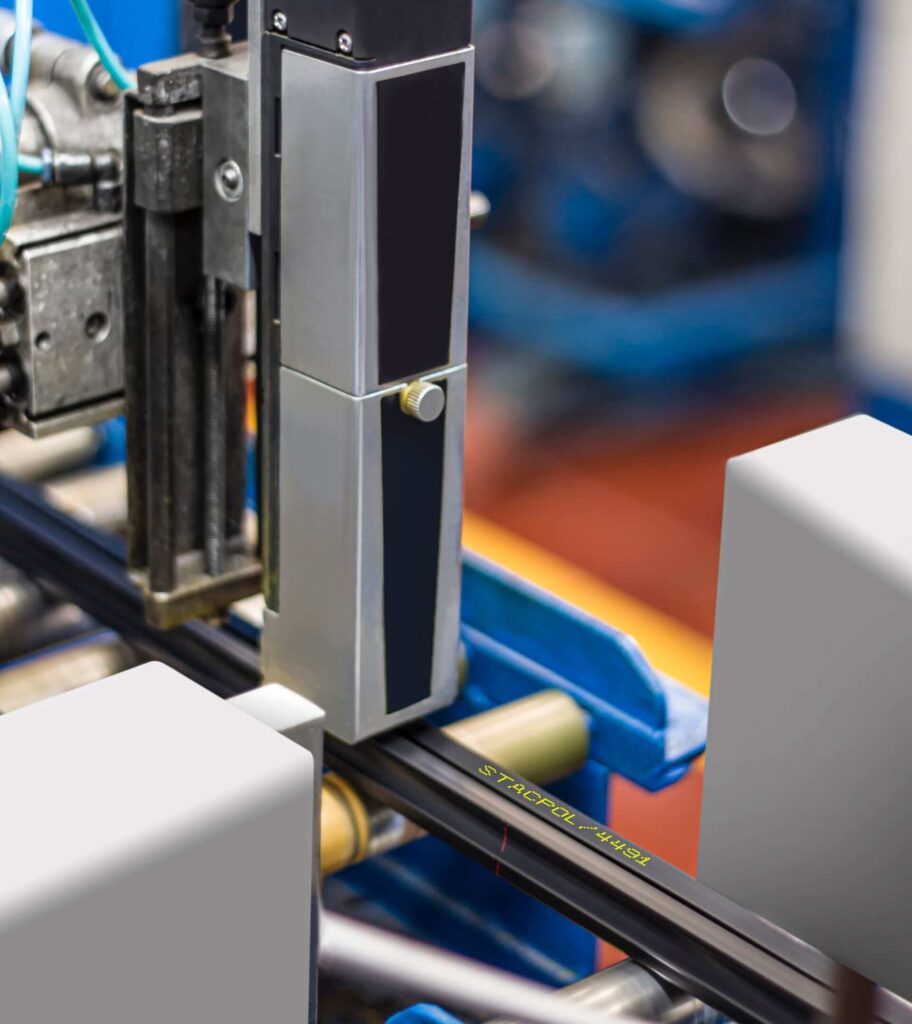
Labelling
Used to mark the surface of the product with a text with relevant traceability information. The ink is sprayed on by a machine positioned at the exit of the extruding die and dries quickly, adhering to the surface.
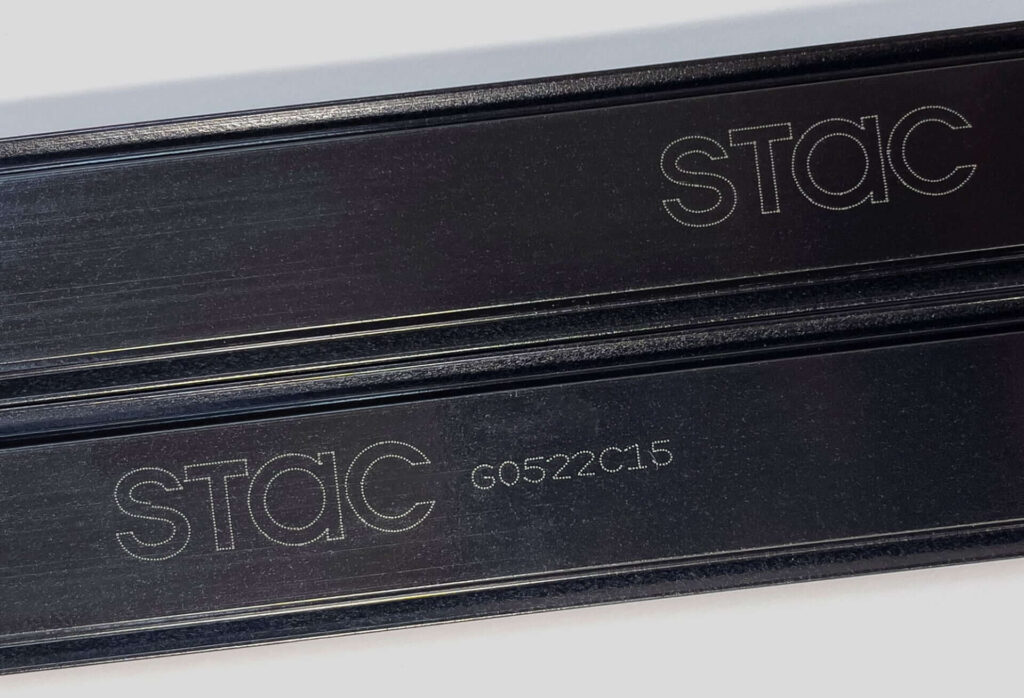
Laser marking
In order to have control of the quality of our products, we identify the profiles by means of a laser engraved code which provides traceability. This way, if there is a claim or incident, we can identify the day, the shift and the line on which it was manufactured.
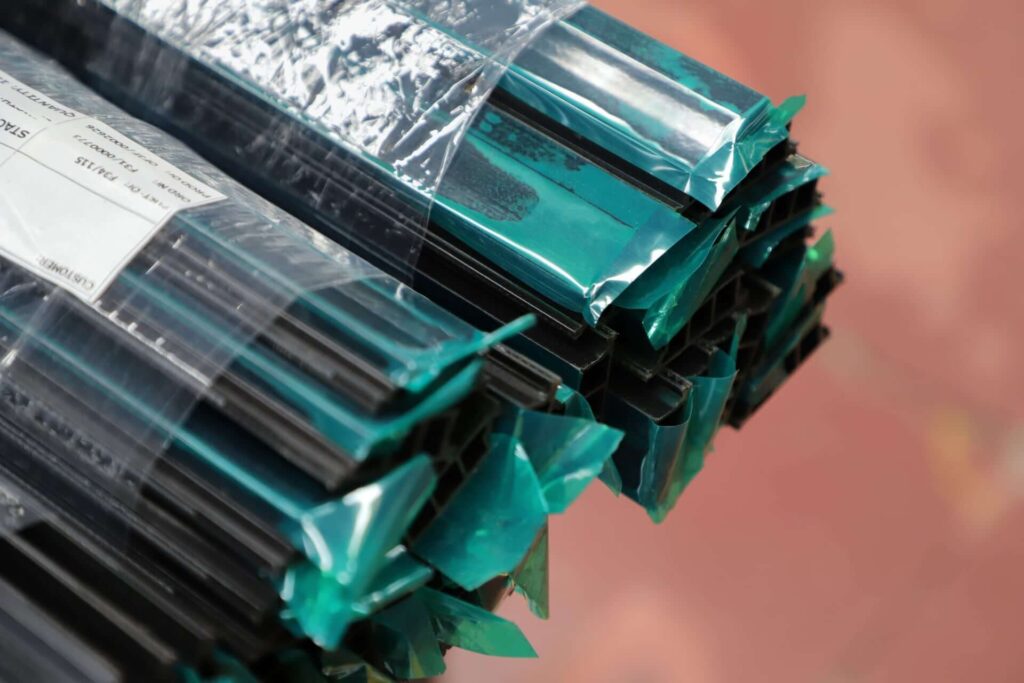
Masking tape
This process consists of using a protective tape called masking tape that protects the polyamide profile during lacquering, ensuring a good surface finish once the tape is removed.
Contact us
We’ll be happy to provide help for your projects and resolve any doubts as soon as possible