Simplifying parts for molding or how can we help you reduce investment
The commercial success of an injection molded product depends on the combination of several key factors:
- An optimized design
- Efficient production
- The right choice of materials
- A well-positioned brand
- High-quality after-sales service.
Each of these elements contributes to the development of a competitive and reliable product capable of responding to market demands and expectations.
To achieve an optimized design, it is essential to comply with the functional and aesthetic specifications of the part, while ensuring its viability and efficiency in the manufacturing process. This will facilitate industrialization, optimize production, and reduce both initial investment and defects, part rejection, and, consequently, the final costs of the product.
An example of this could be the industrialization project for a ball joint that we carried out some time ago for a client, which we will describe below.
In the case in question, the customer sent us an enquiry for the manufacture of a ball joint/articulation consisting of two pieces, manufactured by HPDC (high-pressure injection molding) in zamak. This project also prioritized the complete functionality of the ball joint, along with its aesthetic finish (as it is a visible part).
In the initial analysis of the parts, carried out during the tender phase of the project, the following was detected:
Problems in the initial designs for the manufacturing process:
- Highly mechanical parts (the interior was completely solid). In die casting, “wall” type parts should be chosen to standardize thicknesses and thus the solidification of the part, since uneven solidification causes deformation. In addition, a solid part has a larger volume, which means greater consumption of raw material, resulting in a higher cost per part.
- Areas impossible to mold because they are “in shadow” with respect to the primary molding direction and cannot be molded laterally using slides due to interference with other parts of the piece.
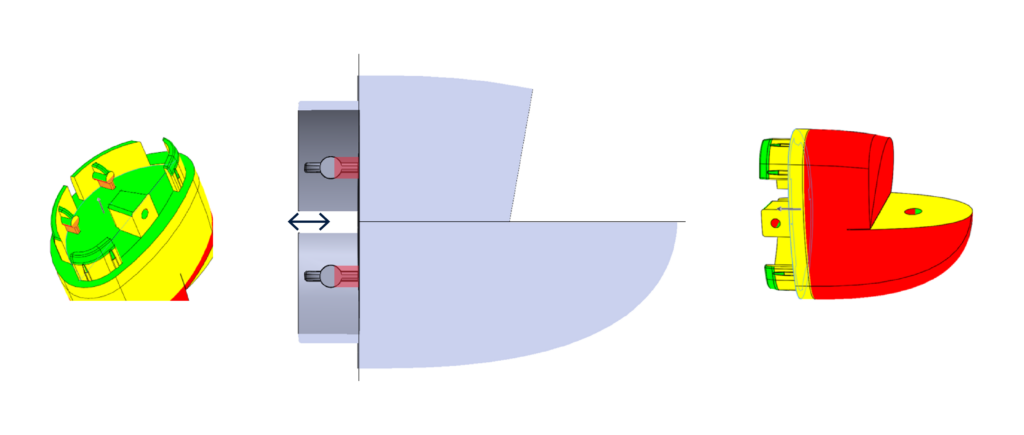
- Areas that, although moldable, pose a very high risk to the life of the mold. This happens when areas with weak steel geometries are created; in this case, the slides would generate a very low steel thickness in relation to the part. There were also other critical areas, but these were due to imperfections in the surface design.
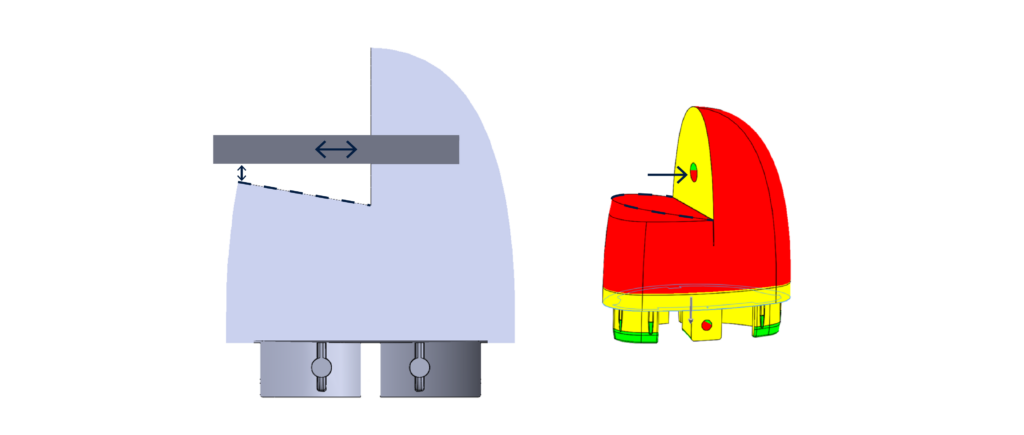
- Complex mold due to the need to place multiple slides. The parts had multiple areas and holes that could not be molded in the primary molding direction. These slides in turn generate marks on the part in the “closure” areas, and many of these would remain in visible/aesthetic areas.

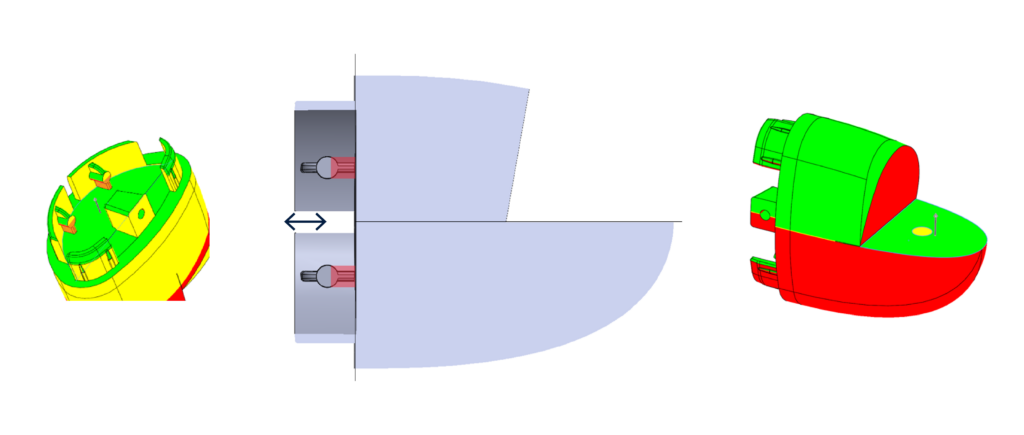
- Difficulty in removing the part from the mold without affecting its outer surfaces (aesthetic parts), as well as avoiding gate lines on them in any of the different molding options.
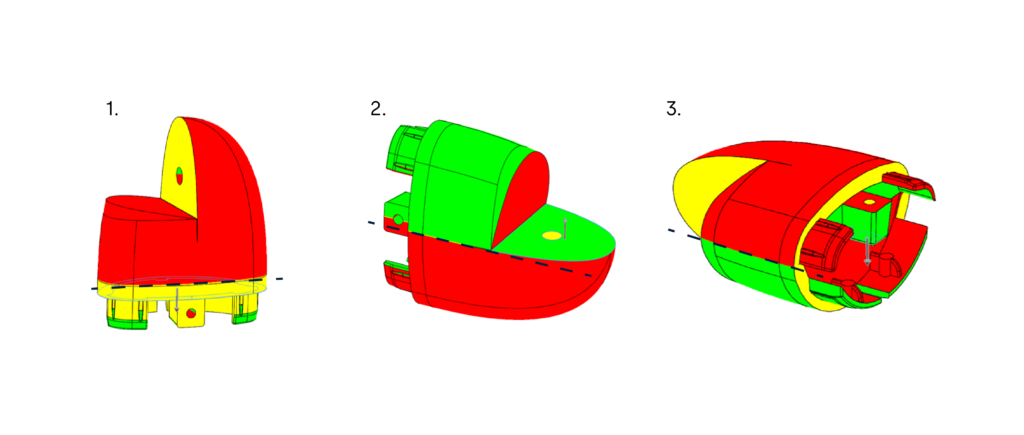
- Design flaws due to lack of refinement. This point is not usually important, but it is always necessary to bring it to light as soon as possible to avoid problems in later stages.
In this case, there were surfaces that joined together, creating non-moldable “grooves.”
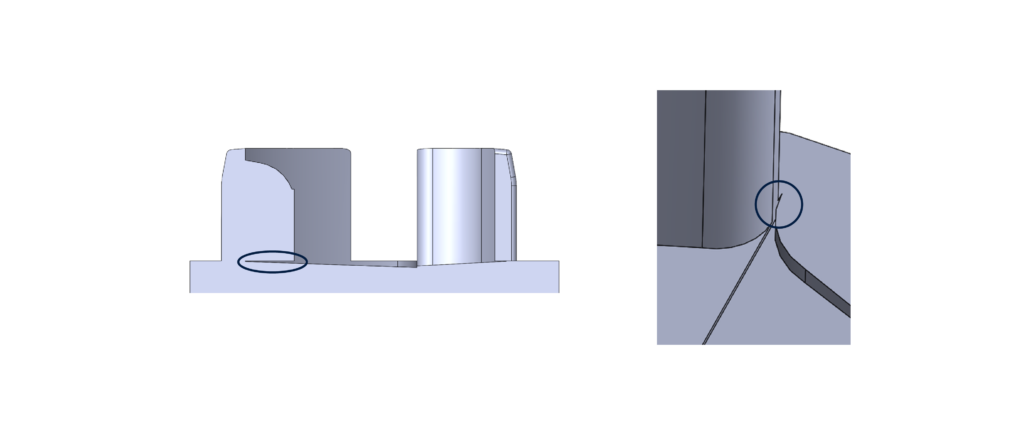
In light of these main issues, we initiated a close dialogue with the client to explore different options and proposals. This exchange allowed us to gain a deeper understanding of how the designs worked and the environment in which they operated.
This dialogue is key to proposing solutions that maintain the characteristics of the final product and improve its performance and optimization.
If you would like to learn more about how this process progressed and how we addressed each challenge to arrive at a perfect solution, we invite you to subscribe to our blog. Gain access to exclusive content, interviews, and case studies detailing how we turned every challenge into an opportunity.
Contact us
We’ll be happy to provide help for your projects and resolve any doubts as soon as possible