Metals
Alloys are materials formed by the combination of different metals. Varying the metals that form them and the percentages of these, different properties are achieved such as greater mechanical resistance, resistance to corrosion in different environments, greater or lower electrical conductivity or different surface finishes. At STAC we handle a wide range of materials to adapt to the requirements of each application.
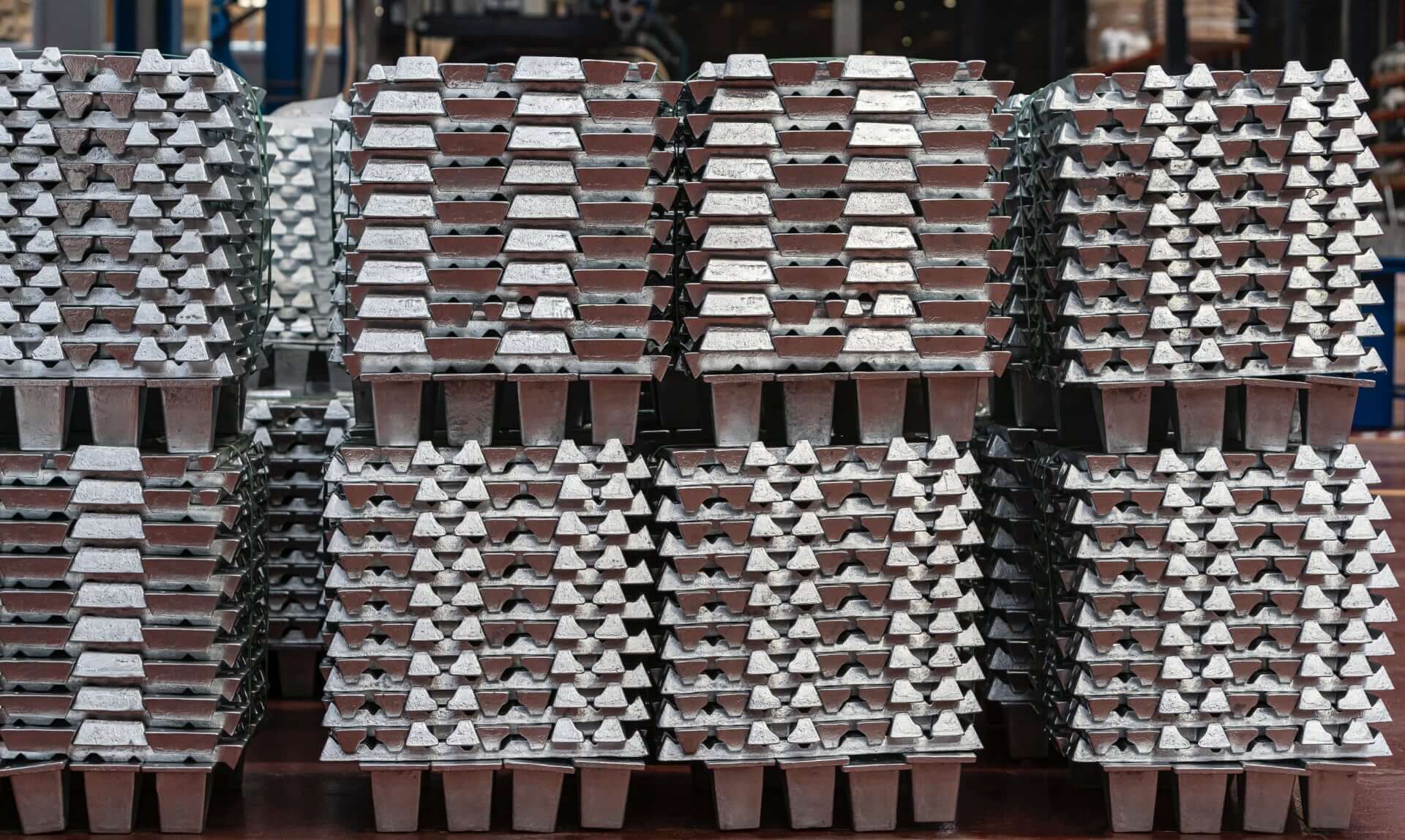
Metals
Alloys are materials formed by the combination of different metals. Varying the metals that form them and the percentages of these, different properties are achieved such as greater mechanical resistance, resistance to corrosion in different environments, greater or lower electrical conductivity or different surface finishes. At STAC we handle a wide range of materials to adapt to the requirements of each application.
AISI 304 Stainless Steel
It is the most common stainless steel due to its quality/price ratio. It has excellent corrosion resistance and is easily formed, allowing various types of parts to be produced.
- Excellent corrosion resistance in most media.
- Excellent weldability.
- Easily formable.
- Good value for money.
- Low resistance to corrosion in cracks, pitting and under stress in environments with chlorides.
Carbon ≤ 0.08 %
Silicon ≤ 1.00 %
Manganese ≤ 1.00 %
Phosphorus ≤ 0.045 %
Sulphur ≤ 0.030 %
Chromium 18.00- 20.00 %
Nickel 8.00 – 11.00 %
Iron % Remainder
- Cremone mechanisms.
- Stay arms for Tilt&Turn.
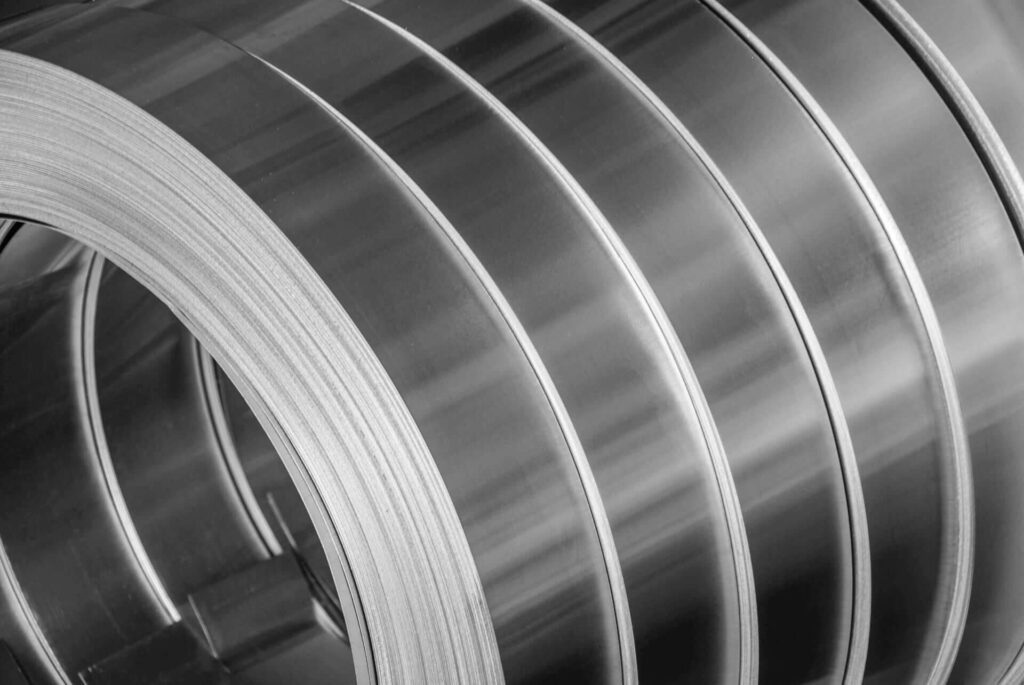
AISI 430 Stainless Steel
Steel with lower corrosion resistance, worse weldability and lower formability than 304. But in general it is more economical and with a better behaviour to stress corrosion. It has an excellent surface finish, which makes it suitable for aesthetic applications.
- Good corrosion resistance in most media.
- Good surface finish.
- Worse weldability than 304. The thermally affected area can become fragile and sensitive (loses its corrosion protection).
- Low resistance to corrosion by cracks, pitting and under stress in environments with chlorides.
Carbon ≤ 0.10 %
Silicon ≤ 1.00 %
Manganese ≤ 1.00 %
Phosphorus ≤ 0.04 %
Sulphur ≤ 0.02 %
Chromium 16.00 – 18.00 %
Iron % Remainder
- Cremone mechanisms.
- Stay arms for Tilt&Turn.
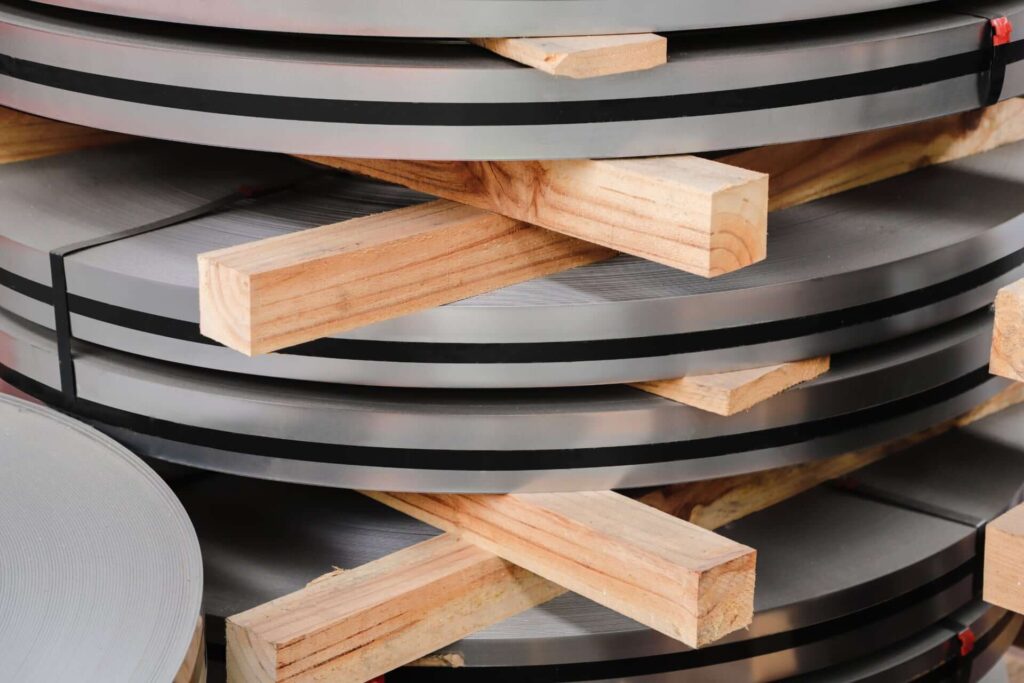
AC46000
Aluminium and silicon alloy. It is a light and electrically conductive alloy, which can be easily lacquered.
- Light alloy.
- Among the aluminium alloys it provides good mechanical resistance.
- Low resistanceto atmospheric corrosion.
- Poor solderability by conventional processes.
Copper 2.00-4.00 %
Magnesium 0.05 – 0.55 %
Iron ≤ 1.30 %
Lead ≤ 0.35 %
Tin ≤ 0.15 %
Níckel ≤ 0.55 %
Zinc 1.20%
Manganese 0.55%
Silicon 8.00 – 11.00 %
Chrome 0.15%
Titanium 0.25%
Trace metals ≤ 0.25 %
Aluminium % Remainder
- Handles.
- Trims.
- Pull handles.
- Hinges.
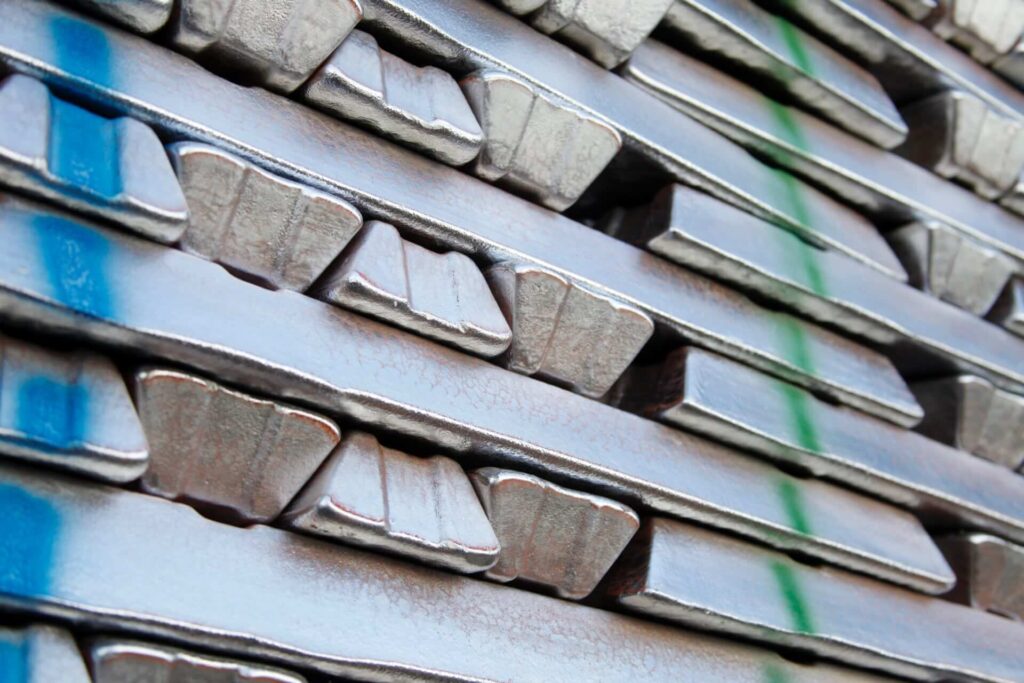
Aluminium 6063
6000 series aluminium alloys are appreciated for their versatility and ability to offer a good combination of mechanical properties, corrosion resistance and overall ease of extrusion processing, making them valuable for a wide variety of industries and applications. They mainly contain aluminium as the base element, with magnesium and silicon as the main elements in the alloy. Other elements, such as manganese and copper, may be present in smaller amounts to adjust properties.
- Can be precipitation hardened.
- Mechanical properties depending on heat treatment.
- Excellent resistance to atmospheric corrosion.
- Very good resistance to pitting in the presence of chloride ions.
- Good resistance to stress corrosion cracking and stress cracking.
- Acceptable machinability.
- Poor chip fragmentation (generates long chips during machining). .
- Intermediate cold formability.
- Good weldability.
- Mechanical strength in HAZ decreases significantly.
- Excellent for decorative anodising.
Magnesium 0,45 – 0,9 %
Silicon 0,2 – 0,6 %
Manganese < 0,1%
Copper< 0,01%
Aluminium > % Remainder
- Profiles for window and door frames.
- Solar panel systems.
- Building structures.
- Aircraft components.
- Auto parts.
- Parts for furnishings, handrails and showcases.
- Parts for bicycles.
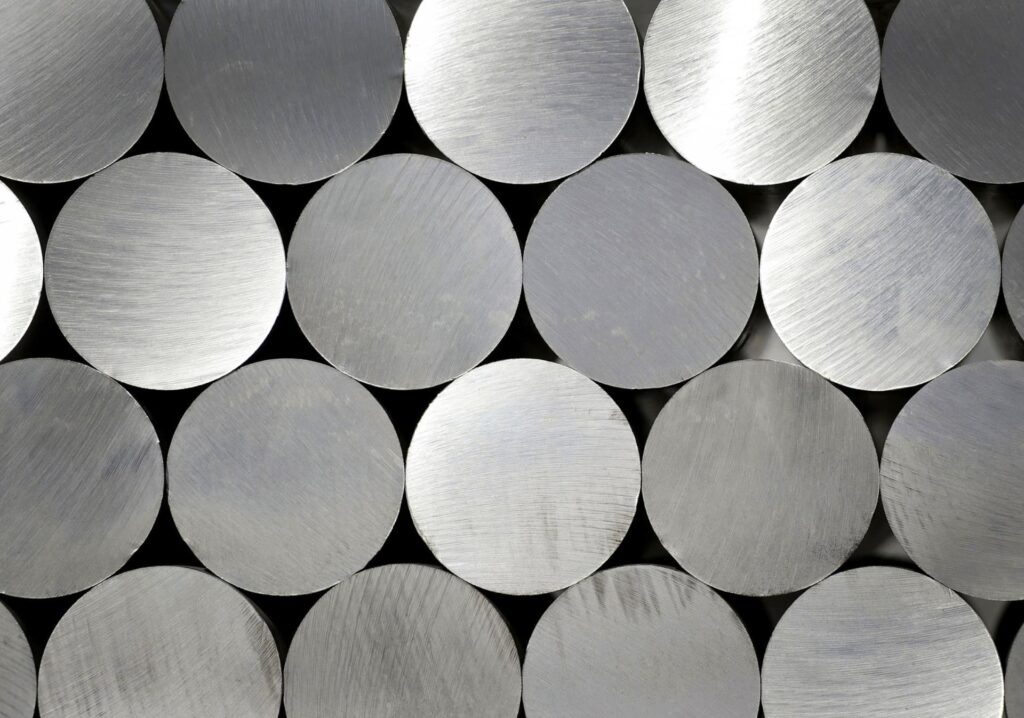
Zamak
This is a family of zinc, aluminium, magnesium and copper alloys. They are lighter than steels but less so than aluminium alloys. It has high mechanical strength, so it can be used for structural parts. It is an economical material that allows multiple processes such as chromium plating, lacquering and machining. The most commonly used zamak alloy in Europe is zamak-5.
- Better finishes and lower cost that aluminium pieces.
- Complex geometries can be injected.
- Heavier than aluminium pieces.
Aluminium 3.50 – 4.30 %
Cadmium ≤ 0.004 %
Copper 0.75 – 1.25 %
Iron ≤ 0.10 %
Lead ≤ 0.005 %
Magnesium 0.03 – 0.08 %
Tin ≤ 0.003 %
Zinc 94.25 – 95.72 %
- Small parts mounted on the window frame.
- Small parts of the mechanisms.

Selection of materials depending on the treatment to be applied
Parameter
Surface finish
Painted
Chrome plating
Machining
Anodizing
AISI 304
GOOD
GOOD
–
POOR
–
AISI 430
GOOD
GOOD
–
POOR
–
AISI 301
GOOD
GOOD
–
POOR
–
AL 6063
EXCELLENT
EXCELLENT
–
EXCELLENT
EXCELLENT
AL 6005
EXCELLENT
EXCELLENT
–
EXCELLENT
GOOD
AL 1050
EXCELLENT
EXCELLENT
–
EXCELLENT
EXCELLENT
AL 5005
EXCELLENT
EXCELLENT
–
EXCELLENT
EXCELLENT
AL 5754
EXCELLENT
EXCELLENT
–
EXCELLENT
EXCELLENT
AC46000
EXCELLENT
EXCELLENT
–
EXCELLENT
POOR
AC44100
EXCELLENT
EXCELLENT
–
EXCELLENT
POOR
ZAMAK 5
EXCELLENT
EXCELLENT
GOOD
EXCELLENT
–
Contact us
We’ll be happy to provide help for your projects and resolve any doubts as soon as possible